Introduction
An air compressor is a must-have item for any woodworking shop. The uses for an air compressor in the shop are numerous, allowing you to sand, paint, and work with projects without constantly having to replace the compressor or readjust settings. With its powerful motor, the air compressor can help make a job easier and faster – saving time and money! It also helps to protect you from breathing in harmful dust particles as it creates a more stable airflow that allows you to finish up quickly.
Beyond sanding, painting, and working with projects, an air compressor can also be used to power your tools. Air compressors provide energy to pneumatically driven tools such as nail guns and staplers so that they work better and faster than manual models do. This can save you time and effort since all the necessary power is already available right at your fingertips. In addition, an air compressor is perfect for powering spray guns for finishing paint jobs without needing to swap out spray cans constantly. It’s also ideal for inflating tires on larger woodworking projects like carts or wheelbarrows.
Overall, an air compressor is an essential part of any woodworking shop”both big and small. Its flexibility combined with its power makes it a great tool to have on hand whenever starting a new project or trying out something new. With just a few basic connections, it’s easy to get started sending enough pressure through hoses so that your equipment takes over most of the hard work – leaving you free to focus on what’s important: creating beautiful pieces made with care and precision!
Comprehensive Guide to Different Types of Air Compressors
When it comes to having a woodworking shop, having an air compressor is essential. Air compressors are powerful pieces of machinery that help inflate objects and help power pneumatic tools. There are many different types of air compressors with varying degrees of power and performance. Before settling on one particular air compressor for your work shop, it’s important to consider what type would fit best in comparison to the tools you plan on using.
Some of the most common types of air compressors include reciprocating piston, rotary vane, rotary screw, centrifugal, and diaphragm models. Each type is designed to meet different needs and come in a variety of sizes and shapes.
Reciprocating piston air compressors use pistons that move back-and-forth inside a cylinder in order to generate compressed air. This action creates both a suctioning and flushing effect which allows for increased efficiency when compared to other types of compressors. Typically this model can produce high amounts of pressure up to 175 psi which makes them ideal for powering impact wrenches or painting equipment.
Rotary vane air compressors use spinning blades set into casings that pump out high-pressure air when pressurized air is introduced into the system pump chamber. These pumps are more compact than the previous one mentioned but they have limitations regarding their maximum discharge pressure as well as their ability to handle extreme cold temperatures. Additionally they require frequent maintenance due to their moving parts which make them less suitable for industrial applications where uninterrupted performance is necessary.
Rotary screw designs use two closely fitted helical screws inside a chamber that draw in ambient surrounding air then pressurize it when turning into each other with great force making them well suited for continuous operations such as powering multiple tools at once or supporting direct cabin pressurization applications on aircrafts . However their cost is much higher than other models and their size can be somewhat bulky due its two motor design but this feature makes them also very durable and reliable when handling tough applications involving heavy dust particles or oil based liquids compared to others .
Centrifugal models provide similar levels of output pressure with less energy used than reciprocating designs making them perfect for large industrial practices since they will take up far less space while still providing enough pressure to get the job done whatever it may be especially those involving combustible gasses or hazardous materials that need precise control under tight conditions . Their main downside includes limited noise level tolerance due their internal fan system along with more complex settings meaning more time to train operators on how they work correctly before deployment .
Diaphragm models have been growing in popularity lately due their intrinsically simple components meaning they require fewer maintenance sessions while being capable of running under rather low operational noises , being some kind typically used on portable purposes like inflating bicycle tires , pool toys or sports balls etc ;; though bear in mind larger diaphragm units can produce widespread gas dispersion be those combustible elements so special precautions must always taken when adjusting these settings accordingly .
Finding the Right Air Compressor for Your Woodworking Needs
Choosing the right air compressor for your woodworking shop is an important decision. There are many factors to consider, including size, power, storage capacity and portability. For a woodworking shop, you will need an air compressor that is powerful and reliable enough to run a wide range of tools, but not so large that it consumes too much space or becomes difficult to manage. An ideal compromise between portability and power is a small-sized, but powerful piston-driven portable air compressor. Not only does this type of air compressor have enough power for most woodworking tasks, but it’s also portable in case you ever need to move it around your workshop. Many models feature adjustable pressure settings so you can tailor them to fit the needs of different tools. Additionally, they typically feature onboard storage tanks that allow you to store compressed air when not in use – reducing wear on your engine while helping improve energy efficiency. Ultimately, with today’s technology, finding the best air compressor for your particular workshop should be easier than ever before – so make sure to do your research and choose one that fits all of your requirements.
Important Considerations Before Installing an Air Compressor
When installing an air compressor for a woodworking shop, there are a few important considerations to keep in mind. The first is how much air pressure the woodworking machinery needs, as this will guide selection of the correct compressor size. It is also important to consider the voltage needs of the compressor and ensure that the electrical wiring can support its requirements. Lastly, it is essential to check for proper ventilation for any motors to avoid overheating, as well as noise produced by these machines which should be contained within acceptable CCM standards. Finally, it is important to note that any air compressors used must comply with local codes and regulations prior to installation.
Step-by-Step Guide to Installing an Air Compressor in Your Workshop
1. Choose the right compressor for your woodworking shop. Consider factors such as size and type, portability, power and capacity to choose the best compressor for your workspace.
2. Ensure that you have the necessary equipment for installation ” air hoses and air filters, for example ” and ensure that all of your electrical requirements meet safety standards.
3. Fit a non-return valve near the compressor to protect against sudden pressure losses from overstresses on the system, e.g., when an air tool starts up or stops abruptly while in use.
4. All connected pipes should be insulated in order to prevent moisture build-up inside them, which can damage tools or make it difficult to get a consistent flow of air pressure through them during operation.
5. Install an air regulator near the compressor outlet to provide a constant level of airflow during operation regardless of fluctuating load pressures across various tools used throughout your shop.
6. Add an emergency shut off switch on the main lead of the compressor so that it can be easily switched off in case of any problems resulting from overpressure settings or mechanical failures within the unit itself.
7. Place secure insulation around exposed hoses, cables and wires which connect from your compressor to any other outlets around your workshop area to avoid potential hazards brought about by friction between them (this is particularly important if LED lighting systems are being used).
8. Test out each component before finalizing installation to make sure that everything is running properly and at optimal performance levels before putting into full operational use within your workspace setting
The Significance of Regular Air Compressor Maintenance
For any woodworking shop that uses an air compressor, regular maintenance is of utmost importance in keeping the machine running at optimal performance. Air compressor maintenance starts with inspecting the oil levels to ensure they meet the manufacturer’s recommendations and draining off any accumulated water. Change filters regularly and keep the environment free from dust that can clog up some parts of the machine. Keep all seals tightly fit to prevent leakage and make sure they are lubricated as per manufacturer guidelines. Inspect belts, hoses, fittings and other components for signs of wear or damage. Identify any potential leaks before they become a bigger problem and repair them immediately. This prevents further issues and potential contamination of the air supply used to operate your equipment. Lastly, set up a schedule for regular maintenance tasks based on each component’s expected lifespan. Following the above steps will not only help you increase productivity in your shop, but also prolong the life of your air compressor!
Essential Tips for Caring for Your Air Compressor
Caring for your air compressor is essential for a safe and efficient woodworking shop. To keep it running in tip-top condition, here are some important tips to follow:
1. Regularly Scheduled Maintenance: It’s best to stick to a regular maintenance schedule to help prevent breakdowns and preserve optimal performance. This includes regularly checking the oil viscosity and level of oil, as well as changing filters, spark plugs and other components according to manufacturer recommendations – typically every 12 months or after 500 hours of usage.
2. Keep It Clean: Woodworking shops generate various dust particles which can enter through air intake vents and affect engine performance by clogging intake valves or polluting the engine oil. To prevent this, make sure you check the filter at least once a month, keeping it clean at all times, with no visible dirt accumulation.
3. Monitor Performance Levels: Track your compressor’s performance levels on a regular basis, listening closely for any abnormal noises coming from the machine when it’s working. Any loud noise or unusual vibrations could indicate that some adjustment or repair is needed before the issue gets worse and causes extensive damage.
4. Quality Brand Air Filters: Invest in quality brand filtration material from credible suppliers as these will last longer than discount products yet provide exceptional particle capture efficiency when properly maintained.
5. Inspect Connections/Piping: Make sure that all hoses, pipes and connections are secure by inspecting them frequently for potential leaks or other damage that may have occurred over time.
6. Protection From Harmful Elements: Outdoor air compressors need constant protection from harsh weather conditions such as rain, extreme temperatures and strong winds so cover those units with proper shielding whenever possible when not in use, even if they’re left outside in between jobs while filling up tanks elsewhere on site
Summary
Having the proper air compressor for your woodworking shop is essential for making sure that all of your projects come out perfect. When working with wood and other materials, a compressed air system can be invaluable. A good air compressor helps with dust collection, spray painting, staining and finishing, nailing, sanding and much more. It’s important to choose the right unit for the tools you are using. Consider the size of your shop and what type of power requirements will be needed by your tools and machinery.
Choosing an appropriate air compressor goes beyond just picking something that matches your budget and is within your tool set’s power requirements. It’s also important to consider factors such as duty cycles, output performance, noise level, portability, recovery times, maintenance needs and efficiency. Depending on how often you are likely to use the air compressor (as well as how long you will be using it for) you may need to opt for heavier-duty models with higher levels of storage capacity or a larger motor in order to meet the demands. Additionally, if your shop is large or busy then considerations such as noise control should also be taken into consideration when choosing an air compressor.
A further important factor is energy efficiency ” as not only does this affect running costs but it can also contribute immensely towards environmental friendliness in woodworking shops. Compliance with relevant local noise regulations should also be checked before purchasing any unit “along with reliability figures reported by users in online forums ” in order to make informed decisions when shopping around. Ultimately this should help ensure that whatever model you decide upon exceeds expectations both now and years down the line.
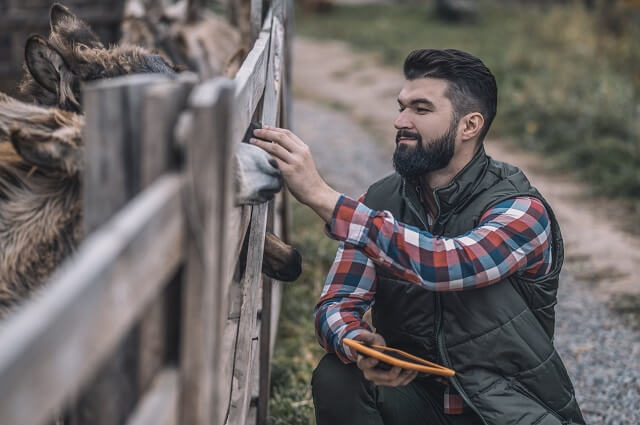
Hi everyone! I’m a woodworker and blogger, and this is my woodworking blog. In my blog, I share tips and tricks for woodworkers of all skill levels, as well as project ideas that you can try yourself.