De Duster woodwork is a remarkable and timeless art form that has captivated woodworking enthusiasts for centuries. This introductory section will delve into the significance of De Duster woodwork in the industry, as well as explore its allure and unique features.
Woodworking as an art form has always held a certain fascination, but De Duster woodwork takes this craftsmanship to new heights. This technique involves meticulous attention to detail and precision, resulting in exquisitely finished pieces. The process consists of carefully removing any dust or debris from the wood’s surface before applying finishes or coatings, ensuring a flawless end result.
The allure of De Duster woodwork lies not only in its immaculate finish, but also in the skill and artistry required to master this technique. The ability to transform a simple piece of wood into a work of art is truly captivating. Each piece showcases the craftsmanship and dedication of the artisans who have perfected their skills over generations.
Throughout this article, we will explore the origins and history of De Duster woodwork, tracing its roots back to ancient civilizations. We will also provide a comprehensive step-by-step guide on how to achieve flawless results in De Duster woodwork, as well as explore inspiring examples of designs and patterns commonly used in this art form.
So join us on this journey as we uncover the beauty and intricacy of De Duster woodwork, discover its advantages and applications, tackle common challenges faced by artisans, showcase famous masterpieces around the world, and explore modern trends and innovations that have shaped this captivating art form.
Historical Background
De Duster Woodwork is an ancient technique that has its roots in the early civilizations of Mesopotamia and Egypt. It is believed to have originated around 3000 BCE and was initially developed as a means to create intricate patterns and designs on wooden surfaces. The technique quickly spread throughout the Mediterranean region, with Greece and Rome adopting it as their own.
Notable artisans played a crucial role in perfecting De Duster Woodwork during this time. One such artisan was Pytheas, a Greek sculptor who introduced innovative tools and techniques that revolutionized the art form. His contributions allowed for greater precision and intricacy in De Duster Woodwork designs.
During the Renaissance period, De Duster Woodwork experienced a revival, with artists like Leonardo da Vinci and Michelangelo incorporating it into their masterpieces. This period saw the refinement of the technique, with artisans experimenting with different wood types, finishes, and decorative motifs.
In the modern era, the influence of De Duster Woodwork can be seen in various architectural structures around the world. The intricate carvings on wooden facades of buildings in India and China are prime examples of how this ancient technique continues to inspire contemporary craftsmanship.
Understanding the historical background of De Duster Woodwork allows us to appreciate its significance in today’s woodworking industry. By tracing its roots back to ancient civilizations and recognizing the contributions of notable artisans across history, we gain a deeper understanding of the craftsmanship involved in this art form.
Understanding the Process
De Duster Woodwork is a meticulous and intricate woodworking technique that requires careful attention to detail. To successfully execute this technique, woodworkers must have a thorough understanding of the step-by-step process involved. Here is a comprehensive guide to help you navigate through the De Duster Woodwork process:
Selection of the Right Wood
The first step in De Duster Woodwork is the careful selection of the right type of wood. Different types of wood have unique characteristics that can influence the final outcome of the project. It is essential to choose a wood species that is durable, stable, and suitable for carving intricate patterns.
Preparing the Tools and Materials
Before diving into the De Duster Woodwork process, ensure that you have all the necessary tools and materials at hand. Some essential tools include carving knives, chisels, files, gouges, and sandpaper. Additionally, gather safety equipment like gloves and goggles to protect yourself during the woodworking process.
Carving and Shaping
Once you have selected your wood and prepared your tools, it’s time to start carving and shaping the wood according to your desired design. Begin by roughing out the basic shape using chisels or carving knives. Gradually refine the details by using finer tools like gouges or files.
Adding Decorative Patterns
One of the distinguishing features of De Duster Woodwork is its elaborate decorative patterns and motifs. This step involves adding these intricate designs to enhance the aesthetic appeal of your project. Common decorative elements include floral motifs, geometric patterns, or even figurative sculptures.
Sanding and Finishing
To achieve a smooth and flawless surface on your De Duster Woodwork piece, sanding is crucial. Use sandpaper with different grits to gradually smoothen the wood surface. Once satisfied, apply a suitable finish, such as varnish or oil, to enhance the natural beauty of the wood and protect it from wear and tear.
By following these steps, you can create exquisite De Duster Woodwork pieces that showcase the beauty of this unique technique. Remember to practice patience and precision throughout the process for truly remarkable results.
The Artistry of De Duster Woodwork
The artistry of De Duster Woodwork showcases the immense skill and creativity involved in this woodworking technique. Craftsmen who specialize in De Duster Woodwork have honed their skills over years of practice, resulting in breathtaking designs that captivate the eye and elevate the beauty of any woodwork project.
Intricacy and Attention to Detail
One of the defining characteristics of De Duster Woodwork is its intricate and elaborate designs. Artisans meticulously carve delicate patterns and motifs into the wood, showcasing their attention to detail and precision. Whether it’s a floral motif or an abstract geometric pattern, each design in De Duster Woodwork tells a unique story.
These exquisite designs not only add visual interest but also enhance the overall value of the woodwork piece. The interplay of light and shadow created by the carved patterns adds depth and dimension, capturing the observer’s imagination.
Common Decorative Patterns and Motifs
De Duster Woodwork incorporates a wide range of decorative patterns and motifs. Some common motifs include scrolls, rosettes, acanthus leaves, arabesques, or even animal forms such as birds or mythical creatures. These elements are intricately carved into the wood using specialized tools to create a three-dimensional effect.
One popular decorative pattern in De Duster Woodwork is marquetry – an art form that involves cutting small pieces of different colored woods to create intricate pictorial designs. This technique allows for stunning creations with vivid images ranging from landscapes to portraits.
Another commonly used pattern is fretwork – a delicate lattice-like design created by cutting out intricate geometric shapes from thin wooden boards. Fretwork adds elegant ornamentation to furniture, cabinet doors, screens, and other architectural elements.
Advantages and Applications
De Duster Woodwork is not just an art form, but also a practical choice in the woodworking industry. In this section, we will explore the advantages and applications of choosing De Duster Woodwork for different projects, such as furniture, cabinetry, and flooring. We will also compare the benefits of De Duster Woodwork to other woodworking techniques.
One of the main advantages of De Duster Woodwork is its ability to create smooth and flawless surfaces. The meticulous process of removing dust particles and impurities ensures that the wood is clean and ready for further treatment or finishing. This level of precision guarantees a high-quality end result that is both visually appealing and durable.
Furthermore, De Duster Woodwork allows for better absorption of finishes and coatings. By eliminating dust particles from the surface, the wood becomes more receptive to stains, paints, varnishes, or sealants. This enhances the overall appearance and longevity of the piece.
Aesthetically, De Duster Woodwork offers a unique appeal that sets it apart from other woodworking techniques. The attention to detail and craftsmanship involved in removing every speck of dust results in a pristine finish that showcases the natural beauty of the wood grain. This makes De Duster Woodwork particularly suitable for projects where visual appeal is paramount, such as high-end furniture or decorative architectural elements.
In summary, De Duster Woodwork offers several advantages that make it a preferred choice in the woodworking industry. Its ability to create smooth surfaces, enhance finish absorption, and showcase exquisite wood grain patterns contributes to its timeless beauty and durability. Whether you are working on furniture, cabinetry, or flooring projects, considering De Duster Woodwork can elevate your craftsmanship to new heights.
Advantages | Applications |
---|---|
Creates smooth and flawless surfaces | High-end furniture |
Enhances finish absorption | Cabinetry |
Showcases exquisite wood grain patterns | Flooring |
Challenges and Resolutions
Common Challenges in De Duster Woodwork
Despite its allure and unique features, De Duster Woodwork is not without its challenges. Like any intricate woodworking technique, it requires skill, precision, and patience. Carrying out this artistry of woodwork can present various obstacles that artisans must overcome to achieve flawless results.
One of the common challenges in De Duster Woodwork is selecting the right wood. The quality of the wood can greatly affect the final outcome. It is important to choose a wood type that allows for intricate carving while maintaining its structural integrity. Additionally, finding a piece of wood with consistent grain patterns can be a challenge, as irregularities in the grain may impact the overall design aesthetic.
Another challenge lies in achieving smooth and even finishes on complex surfaces. When working with intricate designs and patterns, it can be difficult to ensure all areas receive equal attention during sanding and polishing. Areas with tight corners or recesses may require specialized tools or techniques to reach efficiently.
Effective Solutions for Flawless Results
To overcome these challenges and achieve flawless results in De Duster Woodwork, artisans employ various solutions:
- Proper wood selection: Artisans are advised to work with high-quality hardwoods such as mahogany or walnut that have fine and consistent grain patterns. Additionally, utilizing kiln-dried wood helps prevent warping or cracking during the carving process.
- Detail-oriented craftsmanship: To address the challenge of applying finishes on complex surfaces, artisans take a meticulous approach by using smaller tools that allow for precise sanding and polishing in hard-to-reach areas. They also pay close attention to each detail of their design, ensuring consistency throughout the entire piece.
- Professional training and experience: Overcoming challenges in De Duster Woodwork often comes with time and experience. Learning from experienced craftsmen through apprenticeships or attending specialized workshops can provide valuable insights into effective techniques and problem-solving strategies.
Tips and Tricks for Success
To achieve flawless results in De Duster Woodwork, artisans can benefit from the following tips and tricks:
- Patience is key: It is important to take the time needed to properly prepare the wood and execute each step of the process with care and precision. Rushing can lead to mistakes or inconsistent results.
- Test and adjust: Before diving into a complex project, it is advisable to test carving techniques, finishes, and tools on a small sample piece of wood. This allows artisans to refine their approach, make necessary adjustments, and gain confidence before working on the main piece.
- Attention to detail: Paying close attention to every detail, no matter how small or seemingly insignificant, ensures a cohesive and polished final product. Artisans often use magnifying glasses or specialized lighting to aid in their focus.
By understanding common challenges, utilizing effective solutions, and incorporating time-tested tips and tricks, artisans can overcome obstacles in De Duster Woodwork and achieve exceptional results that showcase the true beauty of this remarkable woodworking technique.
Showcasing Masterpieces
De Duster Woodwork has produced some truly remarkable masterpieces around the world. From architectural structures to intricate furniture pieces, these works of art showcase the immense skill and attention to detail that goes into De Duster Woodwork craftsmanship. In this section, we will explore some of the most famous examples of De Duster Woodwork from different parts of the globe and delve into the stories behind these iconic pieces.
One such masterpiece is the Alhambra in Granada, Spain. Known for its stunning Islamic architecture, the Alhambra features exquisite woodwork throughout its palaces and courtyards. The intricate carvings and geometric patterns are a testament to the precision and artistry of De Duster Woodwork. Each piece was meticulously crafted by skilled artisans who spent hours upon hours creating these breathtaking designs.
Another iconic example of De Duster Woodwork can be found in Japan’s Himeji Castle. This UNESCO World Heritage site is renowned for its beautiful wooden interiors, including its elaborate ceiling woodwork. The delicate wooden lattice work, known as “kumiko,” showcases the versatility and intricacy of De Duster techniques. These patterns provide both structural support and decorative elements, creating a harmonious blend of form and function.
Moving to Morocco, we encounter the stunning Moulay Ismail Mausoleum in Meknes. This architectural marvel features elaborate wood ceilings adorned with intricate geometric patterns executed through De Duster Woodwork techniques. The combination of precise detailing, craftsmanship, and artistic vision makes this mausoleum a true masterpiece.
These are just a few examples of famous De Duster Woodwork pieces around the world. Each one represents a unique blend of cultural influences, historical significance, and refined craftsmanship that continue to inspire woodworkers today.
Masterpiece | Location | Description |
---|---|---|
Alhambra | Granada, Spain | The Alhambra features exquisite woodwork throughout its palaces and courtyards, showcasing intricate carvings and geometric patterns. |
Himeji Castle | Himeji, Japan | The wooden interiors of Himeji Castle display delicate lattice work known as “kumiko,” highlighting the versatility and intricacy of De Duster Woodwork. |
Moulay Ismail Mausoleum | Meknes, Morocco | The Moulay Ismail Mausoleum features elaborate wood ceilings adorned with intricate geometric patterns executed through De Duster Woodwork techniques. |
Modern Trends
In recent years, De Duster Woodwork has seen a resurgence in popularity due to the innovations and contemporary approaches that have been incorporated into this traditional woodworking technique. This section will explore some of the modern trends that have emerged in De Duster Woodwork, showcasing how artisans are pushing the boundaries of creativity and craftsmanship.
One notable innovation in De Duster Woodwork is the integration of technology and machinery. Traditional hand tools still play a vital role in the process, but advancements in technology have allowed for greater precision and efficiency. For instance, computer-aided design (CAD) software can aid artisans in creating intricate patterns and designs with utmost accuracy before executing them on the wood.
Additionally, CNC (Computer Numerical Control) machines can automate certain aspects of the process, such as carving out specific motifs or designs on multiple pieces of wood. These technological advancements not only save time but also enable artisans to achieve complex patterns that were once deemed nearly impossible to create by hand alone.
Contemporary approaches to De Duster Woodwork have also opened up new possibilities for incorporating other materials into the process. Artisans are now experimenting with combining wood with other elements such as metal or glass to create striking contrasts and add unique textures to their creations. This fusion of materials adds another layer of complexity and interest to De Duster Woodwork pieces, making them even more visually captivating.
Moreover, contemporary designers are challenging traditional design conventions by exploring new forms and aesthetics within De Duster Woodwork. While traditional patterns and motifs continue to hold their charm, there is an increasing trend towards incorporating elements of minimalism and abstract art into this craft. The use of clean lines, negative space, and unconventional shapes brings a fresh and modern perspective to De Duster Woodwork.
Conclusion
In conclusion, De Duster Woodwork is a truly remarkable and timeless woodworking technique that deserves recognition and appreciation in today’s world. Its significance in the woodworking industry cannot be overstated, as it showcases exquisite craftsmanship and attention to detail that is unparalleled.
Throughout history, De Duster Woodwork has evolved and perfected by notable artisans who have dedicated their lives to this art form. Their contributions have played a crucial role in shaping the technique into what it is today. By tracing the roots of De Duster Woodwork, we gain a deeper understanding of its historical background and the passion that drives artisans to create such breathtaking pieces.
The process of De Duster Woodwork may seem complex, but with the right tools and materials, anyone can achieve flawless results. The step-by-step guide provided in this article offers valuable insights on how to embark on your own journey into this enchanting world of woodworking. From selecting the right wood to applying final finishing touches, each step is essential in creating masterpieces that showcase the artistry of De Duster Woodwork.
Frequently Asked Questions
Is a dust extractor better than a shop vac?
A dust extractor and a shop vac are both effective tools for removing dust and debris, but they have some differences that may make one better suited for certain applications than the other. A dust extractor is typically designed with specialized filtration systems that are capable of capturing very fine particles, such as those produced by sanding or cutting materials like wood or drywall. These extractors often provide a higher level of suction power and have features like automatic filter cleaning to maintain performance over time.
On the other hand, a shop vac is more versatile and can handle a wider range of tasks beyond just dust extraction, such as wet vacuuming or pumping water when necessary. So, while a dust extractor may excel at collecting fine dust in woodworking shops or construction sites, a shop vac might be preferred for general-purpose cleaning and maintenance tasks in homes or workshops.
Can you use a shop vac as a dust collector?
Yes, a shop vac can be used as a makeshift dust collector in some cases. A shop vac is essentially a smaller version of an industrial-style dust collector and is designed to handle various types of debris, including sawdust, shavings, drywall dust, and dirt.
Although it may not have the same level of filtration capabilities as dedicated dust collectors, a well-maintained shop vac with suitable filters can effectively capture large particles of airborne debris during woodworking projects or cleanup tasks in the workshop. It’s important to note that using appropriate attachments and accessories with the shop vac will enhance its effectiveness as a dust collector by providing better airflow control and maximizing suction power.
Do dust collectors work?
Dust collectors are widely used in many industries because they are efficient at removing harmful airborne contaminants and maintaining cleanliness within work environments. These devices work by creating negative pressure inside an enclosed area or system where air is circulated. As the air moves through the collector, larger particles are separated from the airflow through mechanisms like cyclonic action or gravity settling chambers.
Smaller particles then pass through filters specifically designed to capture fine dust particles, preventing them from being released back into the surrounding environment. The collected dust is typically deposited into a collection bag or drum, making it easy to dispose of or reuse in some cases. While the effectiveness of a dust collector depends on factors like its design, filtration efficiency, and proper maintenance, when used correctly and matched with appropriate tools and systems, they can significantly improve air quality and reduce health risks associated with harmful airborne particles in industrial settings.
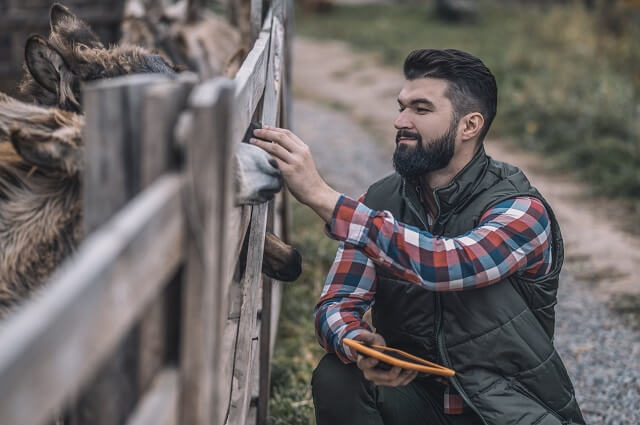
Hi everyone! I’m a woodworker and blogger, and this is my woodworking blog. In my blog, I share tips and tricks for woodworkers of all skill levels, as well as project ideas that you can try yourself.