Are you interested in learning how to make mechanical boxes woodworking? Mechanical boxes, also known as puzzle or secret boxes, are a unique and fascinating aspect of woodworking that appeals to DIY enthusiasts and woodworkers alike. In this article, we will explore the concept of mechanical boxes in woodworking, their history, the materials and tools needed to create them, design and planning tips, joinery techniques, assembly and construction instructions, adding mechanical elements, and finishing touches.
The appeal of mechanical boxes lies in their intricate design and hidden mechanisms that can surprise and delight those who interact with them. Whether used for functional purposes or as decorative pieces, these boxes require precision and craftsmanship to create. Throughout history, mechanical boxes have held significance in the craft of woodworking, evolving over time to become more complex and creative in their designs.
To embark on your own journey of crafting mechanical boxes, it is essential to understand the materials and tools required for the task. Additionally, familiarizing yourself with design principles, joinery techniques, assembly methods, adding mechanical elements, and finishing touches will equip you with the knowledge needed to successfully create these captivating wooden creations. Join us as we delve into the world of mechanical boxes woodworking and discover the artistry behind their construction.
History of Mechanical Boxes
The history of mechanical boxes in woodworking dates back to ancient times, where artisans and craftsmen would create intricate and cleverly designed boxes with hidden compartments and movements. These early examples showcase the creativity and ingenuity of woodworkers who were able to combine both form and function in their designs. Mechanical boxes have continued to evolve over the centuries, with different cultures and time periods putting their own unique spin on these creations.
One significant era for mechanical boxes was during the Renaissance period, where elaborate puzzle boxes and automata were highly sought after as luxury items. Artisans during this time utilized complex mechanisms to create boxes that could only be opened through a series of secret movements or combinations. These marvels of engineering became prized possessions among nobility, showcasing not only the craftsmanship of the woodworkers but also their ability to incorporate ingenious mechanical elements into their designs.
Moving forward in history, the Victorian era saw a resurgence of interest in mechanical boxes, particularly those featuring intricate clockwork mechanisms. Wooden music boxes with revolving figurines and other moving parts became popular keepsakes, once again highlighting the fascination people have with objects that possess both beauty and functionality. The Industrial Revolution further contributed to advancements in mechanical box making, as new technologies allowed for more precise manufacturing of gears, cogs, and other moving components.
Overall, understanding the history of mechanical boxes provides valuable insight into the evolution of woodworking techniques and design principles. By delving into the past, modern woodworkers can gain inspiration from traditional methods while also incorporating contemporary innovations into their own creations.
Finally how important is it that we recognize all these steps when making wooden mechanical work pieces? After all creates a sort blend between artistry(making them attractive) & mechanized use(full functionality). Regular wood art doesn’t always bring about as captivating artwork as these mechanical wooden artifacts so it’s important we never overlook any details because they matter even tho woodworking has evolved since then hence its importance even today at our present technological world.
Materials and Tools
Creating mechanical boxes in woodworking requires specific materials and tools to achieve the desired results. When it comes to wood types, it is essential to select high-quality hardwoods that are durable and can withstand the mechanisms associated with mechanical boxes. Some popular options include oak, maple, cherry, and walnut. Additionally, it is crucial to have a variety of hinges and joints on hand to ensure smooth movement and functionality in the box.
Tools play a significant role in the creation of mechanical boxes. A set of quality chisels, a dovetail saw, and a mallet are essential for precise cutting and shaping of the wood. Specialized equipment such as a drill press or router may also be necessary to create holes for intricate designs or mechanisms within the box. Furthermore, having reliable clamps will assist in securing pieces together during assembly.
In addition to wood types and hardware, it’s important to consider miniature machinery components like gears, levers, springs or pistons that may need to be incorporated into the design of the box for desired movement or functionality. Crafters should also take into account that unique designs when not only raise aesthetic appeal but add value by demonstrating complexity.
Design and Planning
Measurements and Sketches
Before starting the construction of a mechanical box, it is important to create detailed measurements and sketches. These will serve as a guide throughout the project, ensuring that the dimensions are accurate and that the design meets the intended functionality. Accurate measurements will guarantee that all components fit together seamlessly, while sketches can help visualize how the box will operate once complete.
Considerations for Movement and Mechanisms
One of the key aspects of designing a mechanical box is considering its movement and mechanisms. Whether incorporating gears, levers, or springs, it’s essential to plan out how these elements will interact with each other and with the box itself. Understanding how these mechanisms work together will ensure that the end result is not only aesthetically pleasing but also fully functional.
Unique Designs
Creating unique designs for mechanical boxes allows woodworkers to showcase their creativity and craftsmanship. Consider incorporating personalized engravings, inlays, or intricate patterns into the design to make the box stand out. Additionally, exploring unconventional shapes or adding unexpected elements can make a mechanical box truly one-of-a-kind.
By taking these design and planning tips into consideration when creating a mechanical box through woodworking, enthusiasts can ensure that their final product is both visually appealing and fully functional. Attention to detail during this stage of the process will set a solid foundation for successful construction and assembly in subsequent steps.
Joinery Techniques
Creating mechanical boxes requires careful consideration of joinery techniques to ensure the structural integrity and functionality of the final product. Dovetail joints, mortise and tenon, and box joints are widely used in woodworking and are especially relevant when constructing mechanical boxes due to their strength and precision. Dovetail joints, in particular, are favored for their resistance to being pulled apart and their decorative appeal.
Mortise and tenon joints offer a strong connection between two pieces of wood, making them suitable for the moving parts of a mechanical box. Box joints, on the other hand, provide a large gluing surface for increased stability.
When deciding on the appropriate joinery technique for a mechanical box, it’s essential to consider the specific requirements of the design and movement mechanisms. Dovetail joints may be ideal when creating drawers or sliding components within the box, while mortise and tenon joints could be more suitable for connecting rotating or pivoting components. Box joints can also be utilized for stationary sections or those that require additional reinforcement due to frequent use.
Furthermore, experimenting with combinations of joinery techniques can lead to innovative designs that enhance both the aesthetic appeal and functionality of a mechanical box. By incorporating various joint types within a single project, woodworkers can create visually striking pieces that showcase their skill and attention to detail.
Joinery Technique | Best Use |
---|---|
Dovetail Joints | Creating drawers or sliding components |
Mortise and Tenon Joints | Connecting rotating or pivoting components |
Box Joints | Stationary sections or those requiring additional reinforcement |
Assembly and Construction
When it comes to making mechanical boxes through woodworking, the assembly and construction process is a crucial and intricate part of the overall project. To ensure that your mechanical box functions as intended, it is essential to carefully follow step-by-step instructions for cutting, shaping, and fitting the components together. Below are detailed guidelines on how to effectively assemble and construct a mechanical box:
1. Cutting the Wood: The first step in constructing a mechanical box is to accurately cut the wood components according to your design and measurements. Use a high-quality table saw or bandsaw for straight cuts, and a scroll saw for more intricate shapes or curves. It’s important to pay close attention to detail during this stage to ensure precision and accuracy in the final product.
2. Shaping the Components: After cutting the wood pieces, the next step is shaping them according to your design. This may involve using a router for creating decorative edges, chamfering corners, or creating specific profiles on the wood. Additionally, drilling any necessary holes for hinges or other moving parts should be done at this stage using a drill press or handheld drill.
3. Fitting the Components Together: Once all the individual pieces are cut and shaped, it’s time to fit them together according to your design plan. Utilize woodworking clamps to hold pieces in place as you attach them with wood glue or screws. Pay careful attention to alignment and ensure that all joints are snug and secure before allowing any adhesive or fastener to set.
By following these step-by-step instructions, you can successfully assemble and construct a mechanical box that showcases both precision woodworking techniques and functional moving elements.
For those who are new to woodworking or unfamiliar with certain tools used in this process, seeking guidance from experienced woodworkers or professional instruction can be beneficial in ensuring successful construction of mechanical boxes.
Adding the Mechanical Elements
When it comes to making mechanical boxes in woodworking, one of the most exciting parts of the process is incorporating the mechanical elements that bring the box to life. Gears, levers, and springs are key components that give mechanical boxes their unique functionality and appeal. Whether you’re a seasoned woodworker or a DIY enthusiast, adding these elements requires careful planning and execution to achieve the desired movement and functionality.
To begin incorporating mechanical elements into your box, you will need to gather the necessary materials and tools. This may include gears of different sizes and shapes, levers for controlling movement, springs for adding tension or bounce, and other specialized components depending on the specific design of your mechanical box. You may also need small screws or fasteners to secure these elements into place within the box.
Once you have gathered your materials and tools, it’s time to carefully plan out how these mechanical elements will fit into your design. Considerations such as space constraints, movement range, and interaction between different components should be taken into account during this phase. Sketching out a detailed plan can help ensure that all parts work together seamlessly once assembled.
Additionally, testing each individual component before final assembly can help identify any potential issues early on in the process. By thoughtfully incorporating gears, levers, springs, and other mechanical elements into your woodworking project, you can create a stunning and functional piece that is sure to impress.
Finishing Touches
In conclusion, making mechanical boxes in woodworking can be a rewarding and enjoyable endeavor for DIY enthusiasts and woodworkers alike. The history of mechanical boxes demonstrates their significance in the craft, as well as the evolution of designs and functionality over time. By understanding the materials and tools needed, as well as the joinery techniques and design considerations, individuals can create unique and functional mechanical boxes that showcase their craftsmanship and creativity.
As with any woodworking project, attention to detail is crucial, especially when it comes to finishing touches. Sanding the surfaces to a smooth finish, choosing the right stain or finish to enhance the wood’s natural beauty, and adding final touches like hardware or decorative elements can elevate a mechanical box from a simple creation to a professional-looking piece.
These tips on sanding, staining, and finishing are essential to achieving a polished final product that reflects the time and effort put into its creation.
Ultimately, learning how to make mechanical boxes in woodworking involves mastering various skills, from precise measurements during planning to intricate joinery techniques during construction. However, with dedication and practice, individuals can create stunning mechanical boxes that not only showcase their woodworking abilities but also add a touch of elegance and functionality to any space. Whether for personal use or as a gift for others, these custom-made pieces are sure to be cherished for years to come.
Frequently Asked Questions
How Do You Make a Woodworking Box?
Making a woodworking box involves several steps, including measuring and cutting the wood to the desired size, assembling the pieces using techniques like dovetail joints or rabbets, sanding the surfaces to smooth them out, and then applying a finish such as stain or varnish to enhance the appearance and protect the wood.
What Is the Best Wood to Make a Box Out Of?
The best wood to make a box out of depends on personal preference and the intended use of the box. Hardwoods like oak, cherry, maple, and walnut are popular choices due to their durability and attractive grain patterns. Softwoods like pine and cedar are also commonly used for their affordability and ease of working with hand tools.
What Tools Do I Need to Make a Wood Box?
The tools needed to make a wood box include a saw for cutting the wood to size, chisels for shaping joints and removing material, a plane for smoothing surfaces, clamps for holding pieces together during assembly, a hammer or mallet for driving in fasteners, sandpaper for finishing touches, and a brush or cloth for applying a finish to protect the wood.
Additionally, some woodworkers may use power tools like table saws or routers for more efficient shaping and joinery work.
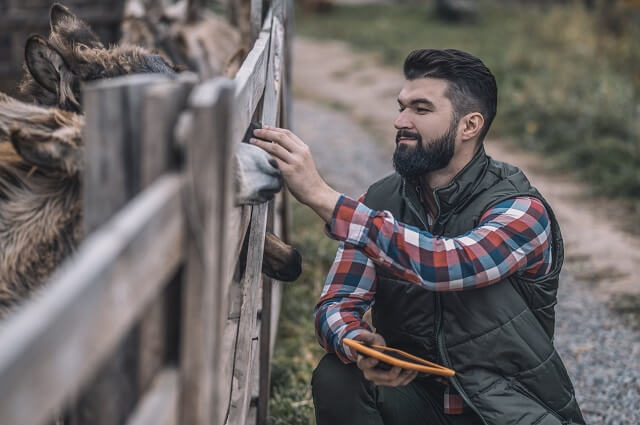
Hi everyone! I’m a woodworker and blogger, and this is my woodworking blog. In my blog, I share tips and tricks for woodworkers of all skill levels, as well as project ideas that you can try yourself.