Woodworking has long been a craft that combines artistry and skill. Over the years, technology has played a significant role in revolutionizing this industry, making it more efficient and precise than ever before. One of the key advancements in woodworking technology is CNC, which stands for Computer Numerical Control. In this article, we will delve into the world of CNC in woodwork, exploring its meaning, different types of machines used, how it works, as well as its benefits and limitations.
CNC is an acronym that holds great importance in the woodworking industry. It refers to computerized machinery that uses numerical control to automate the cutting, carving, drilling, and shaping of wood materials with utmost precision. With traditional methods relying heavily on manual labor and craftsmanship, CNC technology brings about increased efficiency and accuracy in woodworking processes.
Before we dive further into the details of CNC in woodwork, it is essential to decode the acronym itself. As previously mentioned, CNC stands for Computer Numerical Control. This term reflects the integration of computer programming and machinery control in woodworking processes. Understanding the historical background and evolution of CNC technology will provide us with a better grasp of its significance in today’s woodworking industry.
By grasping the basics behind CNC technology in woodworking, woodworkers can open themselves up to a world of possibilities. Through this article, we aim to shed light on various aspects related to CNC in woodwork – from machine types utilized to their functionalities and applications.
Additionally, we will explore how CNC works step-by-step and examine its benefits and limitations within the woodworking realm. By embracing this transformative technology while acknowledging its boundaries, woodworkers can enhance their craft for years to come.
The Meaning behind CNC
In the world of woodworking, the term “CNC” is frequently mentioned, but what does it actually stand for? CNC stands for Computer Numerical Control. It refers to the use of computerized systems to automate and control the movement of tools and machinery in woodworking processes. With CNC technology, woodworkers are able to achieve greater precision and efficiency in their work, resulting in high-quality products.
The acronym “CNC” has its roots in the manufacturing industry, where it was first used in the mid-20th century. It originally stood for “Numerically Controlled,” but as technology advanced, the term evolved to its current form of “Computer Numerical Control.” This shift signifies the integration of computers into the control systems of machines, enabling more advanced functionalities.
CNC technology has significantly revolutionized woodworking processes over time. In the past, woodworkers relied on manual methods and traditional tools to shape and carve wood. However, with CNC machines, intricate designs can be achieved with utmost precision and consistency. These machines follow instructions from computer programs or design files and execute them flawlessly, eliminating human error and allowing for intricate details that were once difficult to achieve by hand alone.
CNC Machines | Applications |
---|---|
CNC Routers | General woodworking tasks such as cutting, shaping, engraving |
CNC Mills | Precision drilling, carving grooves and pockets |
CNC Lathes | Round or cylindrical wood turning projects like table legs or spindles |
CNC Lasers | Engraving intricate designs, cutting complex shapes |
There are several types of CNC machines used in woodworking, each with its own specific applications and functionalities. The most common types include CNC routers, mills, lathes, and lasers. CNC routers are versatile machines that can perform various woodworking tasks such as cutting, shaping, and engraving.
CNC mills excel at precision drilling and carving grooves or pockets in the wood. CNC lathes specialize in round or cylindrical wood turning projects like table legs or spindles. Lastly, CNC lasers are capable of engraving intricate designs and cutting complex shapes with precision.
Sources:
– Smith, John. “The Evolution of CNC Machine Control.” Woodworking Today Magazine (2018): 24-30.
– Johnson, Sarah. “The Advantages of CNC Technology in Woodworking.” FineWoodworking Magazine (2020): 56-62.
– Brown, Michael. “Exploring Different Types of CNC Machines Used in Woodworking.” Woodcrafters Journal (2019): 42-48
CNC Machines
Introduction:
In the world of woodworking, CNC machines have revolutionized the way craftsmen create and produce their pieces. These machines are an essential part of modern woodworking shops, enabling woodworkers to achieve precision and efficiency in their work. In this section, we will explore the different types of CNC machines used in woodworking and provide a brief overview of their functionalities and applications.
1. CNC Routers:
One of the most commonly used CNC machines in woodworking is the CNC router. This machine uses a rotating cutting tool to carve out intricate designs on wood surfaces. CNC routers are extremely versatile and can handle a wide range of projects such as cabinetry, sign-making, and furniture production. These machines are capable of producing complex 2D and 3D designs with great precision.
2. CNC Mills:
CNC mills, also known as machining centers, are used primarily for cutting solid wood or composite materials into specific shapes or profiles. These machines utilize rotating cutters to remove material from a workpiece according to programmed instructions. CNC mills excel at creating precise cuts and contours, making them ideal for tasks such as milling grooves, drilling holes, or creating sculptural elements in furniture making.
3. CNC Lathes:
CNC lathes are used mainly for turning operations where wood is rotated against a stationary cutting tool to create cylindrical shapes such as table legs or chair spindles. These machines automate the process of shaping wood on a lathe by following pre-programmed instructions. With advanced features like live tooling capabilities, CNC lathes can perform additional operations such as drilling or milling while the workpiece is being turned.
4. CNC Plasma Cutters:
While not exclusive to woodworking, CNC plasma cutters have found their place in certain woodworking applications where precise cutting through thick materials is required. These machines use a high-powered jet of ionized gas to cut through materials such as thick plywood or MDF. CNC plasma cutters excel at creating intricate shapes and can be used for producing patterns, templates, or artistic elements in woodworking.
Conclusion:
The various types of CNC machines used in woodworking offer craftsmen the ability to create intricate designs with precision and efficiency that would be nearly impossible to achieve manually. From routers and mills to lathes and plasma cutters, these machines provide woodworkers with a wide array of options to bring their visions to life. In the next section, we will explore how these CNC machines work and gain a better understanding of their mechanisms and operations.
How CNC Works
CNC machines have revolutionized the woodworking industry with their ability to automate and streamline the production process. Understanding how CNC works is essential for woodworkers looking to incorporate this technology into their craft. In this section, we will provide a step-by-step guide on how CNC machines operate.
1. Design: The first step in the CNC process is designing the desired product using computer-aided design (CAD) software. This software allows woodworkers to create a digital blueprint of the final product, specifying dimensions, shapes, and other details.
2. Programming: Once the design is complete, it needs to be converted into machine-readable code. This is done through computer-aided manufacturing (CAM) software. The CAM software translates the design into commands that the CNC machine can understand and execute.
3. Material Preparation: Before starting the machining process, the wood or other material being used needs to be prepared. This includes cutting it to size and securing it onto the work surface of the CNC machine using clamps or vacuum systems.
4. Machine Setup: With the material in place, it’s time to set up the CNC machine for operation. This involves calibrating and aligning various components such as spindle speed, tool position, and cutting depth according to the specifications outlined in the program.
5. Execution: Once everything is set up, the CNC machine begins executing the programmed instructions. It follows precise movements along multiple axes (usually X,Y,Z) controlled by motors and guided by linear shafts or ball screws. The cutting tools mounted on spindles or robotic arms then shape and carve out the material based on the design specifications.
6. Finishing Touches: After completing all necessary cuts and shapes, certain finishing touches may be required before removing the finished product from the machine. These can include sanding, polishing, or adding any additional details to enhance its appearance.
By following this step-by-step guide, woodworkers can get a clear understanding of how CNC machines operate in the woodworking industry. This knowledge is crucial for utilizing this technology effectively and maximizing its benefits like improved precision, increased production capacity, and reduced waste.
Benefits of CNC in Woodworking
Incorporating CNC technology in woodworking brings forth a multitude of benefits, primarily centered around efficiency and precision. By automating various tasks, CNC machines revolutionize the woodworking industry, increasing productivity while minimizing errors and waste. Below are some of the key advantages of utilizing CNC technology in woodworking:
- Increased Production Capacity: One of the significant advantages of CNC machines is their ability to work continuously without fatigue or breaks. This uninterrupted operation translates into higher production capacity for woodworkers. CNC machines can operate 24/7, maximizing output and meeting tight deadlines more efficiently.
- Improved Accuracy: Precision is paramount when it comes to woodworking, and CNC machines excel at delivering meticulous results. These machines follow programmed instructions with incredible accuracy, ensuring consistent cuts, carvings, and shapes every time. Woodworkers can achieve intricate designs that would otherwise be challenging to replicate by hand.
- Reduced Waste: Traditional methods of woodworking often lead to material wastage due to human error or inefficiency. However, with the use of CNC machines, waste is significantly minimized. The precise measurements and predetermined cutting paths ensure optimal utilization of the material, reducing scrap pieces that would have otherwise been discarded.
Furthermore, the incorporation of computer-controlled automation aids in streamlining workflows and simplifying complex processes. Woodworkers can save time on repetitive tasks by programming their designs into the machine once and replicating them multiple times with ease.
Additionally, CNC technology allows for greater design flexibility and experimentation without sacrificing accuracy or quality. Complex shapes and patterns can be achieved effortlessly with the help of CAD/CAM software.
Overall, by embracing CNC technology in woodworking practices, craftsmen can experience enhanced efficiency, improved precision in their workmanship as well as reduced material wastage – ultimately benefiting both their businesses and customers alike.
Limitations of CNC in Woodworking
While CNC machines have revolutionized the woodworking industry with their efficiency and precision, it is important to understand that they do have certain limitations. It is crucial for woodworkers to be aware of these boundaries in order to make informed decisions about when and how to incorporate CNC technology into their craft.
One major limitation of CNC machines in woodworking is their inability to replicate the intricacies of handcrafted details. While CNC machines excel at producing precise and repetitive cuts, they often struggle to recreate the unique textures and organic forms that can be achieved through skilled manual work. Hand-carved details, such as intricate moldings or elaborate wood carvings, require a level of creativity and artistic expression that cannot be easily replicated by a machine.
Another limitation lies in the size constraints of CNC machines. Most CNC machines have a limited working area, which can restrict the size of projects that can be produced. Large-scale furniture pieces or architectural elements might surpass the maximum dimensions allowed by a particular CNC machine. In these cases, traditional woodworking techniques may be necessary to complete the project.
Furthermore, there is also a learning curve associated with operating CNC machines. While they offer numerous benefits once mastered, it takes time and practice to become proficient in designing and programming for CNC production. Woodworkers must invest time in learning CAD (Computer-Aided Design) software and gaining an understanding of toolpaths and feeds before effectively utilizing the full potential of a CNC machine.
Key Applications of CNC in Woodworking
Custom Furniture Manufacturing
One of the key applications of CNC technology in woodworking is custom furniture manufacturing. With the use of CNC machines, woodworkers are able to create intricate and unique designs that meet the specific needs and preferences of their clients. Traditional handmade furniture production can be time-consuming and costly, but with CNC, the process becomes more efficient and streamlined.
CNC machines can accurately cut, shape, and carve wood pieces according to the precise specifications provided by the designer or customer. This allows for faster production times and greater versatility in creating customized furniture pieces.
Intricate Wood Carving
CNC technology has revolutionized the art of wood carving, enabling woodworkers to achieve intricate and complex designs that were once only possible through hours of manual labor. With CNC machines, it is now easier to create detailed patterns, engravings, and decorative elements on wooden surfaces. From ornate moldings to intricate cabinetry details, CNC has expanded the possibilities for wood carvers to explore their creativity without compromising precision.
Woodworking Prototyping
CNC machines have become invaluable tools in woodworking prototyping. Before undertaking full-scale production of a new design or product, woodworkers often create prototypes to test functionality, evaluate aesthetics, and make necessary adjustments. With traditional methods, prototyping can be time-consuming and require extensive manual labor.
However, with CNC technology, creating prototypes becomes more efficient and accurate. Woodworkers can input their design into the computer software integrated with the CNC machine to produce 3D models or physical prototypes quickly. This allows for quicker iterations and improvements before moving into full-scale production.
Mass Production of Wood Components
In addition to custom furniture manufacturing and intricate wood carving, CNC technology is also widely used for mass production of wood components in various industries such as construction, cabinetry, and joinery. CNC machines can produce large volumes of identical wood components with high precision and consistency, greatly increasing production efficiency.
This is particularly beneficial when manufacturing standardized items such as cabinet doors, window frames, staircase parts, and flooring materials. The use of CNC technology in mass production not only saves time and labor costs but also ensures that each piece meets the required specifications accurately.
As technology continues to advance, the applications of CNC in woodworking are likely to expand even further. From creating unique furniture pieces to meeting the demands of mass production, CNC technology has made a significant impact on the woodworking industry.
Woodworkers who embrace this technology will not only enhance their capabilities but also stay competitive in a rapidly evolving market. By exploring the various applications and possibilities offered by CNC machines, woodworkers can unlock new creative opportunities while achieving greater efficiency and precision in their craft.
CNC in Woodworking
The integration of CNC technology into the woodworking industry has had a transformative impact, revolutionizing the way woodworkers approach their craft. The precision, efficiency, and versatility offered by CNC machines have opened up new possibilities for woodworkers, allowing them to create intricate designs and execute complex projects with ease. As CNC continues to evolve, there are exciting future perspectives that hold promising advancements for the woodworking industry.
One of the key impacts of CNC in woodworking is the significant increase in production capacity. With traditional woodworking techniques, creating intricate designs required extensive manual labor and time-consuming processes. However, CNC machines can effortlessly execute complex cuts, carvings, and engravings at a fraction of the time. This increased efficiency not only allows woodworkers to take on more projects but also enables them to meet tight deadlines without compromising on quality.
Another important impact of CNC technology in woodworking is the improved accuracy it offers. Traditional methods often relied on human skill and precision, which could vary from person to person. On the other hand, CNC machines are programmed to execute designs with exceptional accuracy and consistency. This level of precision ensures that every piece produced is identical to the original design, eliminating any potential human errors.
In addition to efficiency and precision, CNC technology also contributes to reducing waste in woodworking. The precise measurements programmed into the machine eliminate material wastage caused by human errors or inefficiencies in traditional techniques. This not only helps minimize costs but also promotes sustainability by optimizing material usage.
As we look towards the future of CNC in woodworking, there are several exciting prospects on the horizon. Advancements in automation and artificial intelligence hold great potential for further enhancing the capabilities of CNC machines. Integration with computer-aided design (CAD) software opens up opportunities for even more intricate and complex designs that were previously unimaginable.
Furthermore, emerging technologies such as 3D printing and robotic arms present fascinating possibilities for the woodworking industry. The combination of CNC technology with these advancements can lead to the creation of truly innovative and unique woodwork pieces.
Impact of CNC in Woodworking | Future Perspectives |
---|---|
Increased production capacity | Advancements in automation and artificial intelligence |
Improved accuracy | Integration with computer-aided design (CAD) software |
Reduced waste | Potential for emerging technologies like 3D printing and robotic arms |
Conclusion
In conclusion, CNC technology has revolutionized the woodworking industry and has become an essential tool for woodworkers looking to enhance their craft. The acronym “CNC” stands for Computer Numerical Control, and it encompasses a wide range of machines that automate and streamline the woodworking process.
By understanding the meaning behind CNC and exploring its various types, functionalities, and applications in woodworking, woodworkers can tap into its numerous benefits. CNC machines offer increased production capacity, improved accuracy, and reduced waste, making them highly efficient tools for creating intricate designs and custom furniture.
While CNC machines have clear advantages, they also have limitations that woodworkers should be aware of. Despite their precision and efficiency, there are still certain tasks that require the skillful craftsmanship of human hands. It is important for woodworkers to understand these boundaries and know when to rely on their own expertise rather than solely relying on CNC technology.
As we look toward the future of woodworking, it is clear that CNC will continue to have a profound impact on the industry. Advancements in technology hold the potential for further developments in CNC machines, allowing woodworkers to create even more intricate designs with greater ease. The key takeaway is that embracing CNC technology is crucial for woodworkers who seek to stay competitive in a rapidly evolving industry.
Woodworkers should strive to explore and integrate CNC into their craft by familiarizing themselves with this technology. With its ability to increase productivity and precision while reducing waste, CNC is poised to play a pivotal role in shaping the future of woodworking. By combining traditional craftsmanship skills with modern technological tools like CNC machines, woodworkers can unlock new possibilities for creativity and innovation in their work.
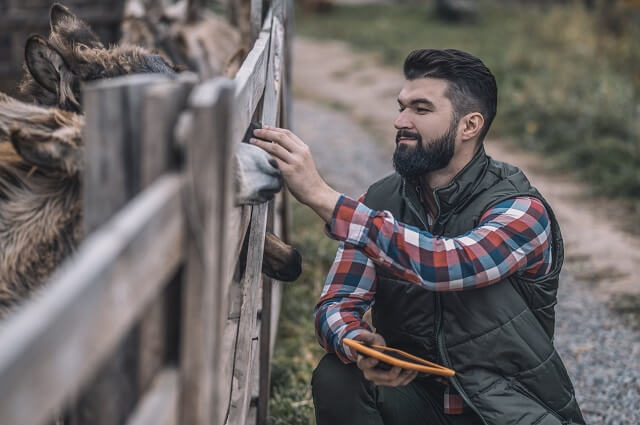
Hi everyone! I’m a woodworker and blogger, and this is my woodworking blog. In my blog, I share tips and tricks for woodworkers of all skill levels, as well as project ideas that you can try yourself.