Woodworking is a craft that requires precision, patience, and attention to detail. From carving intricate designs to assembling delicate pieces, every step in woodworking demands careful execution. One often overlooked aspect of this craft is the use of lubricants. In this article, we will explore the importance of using lube in woodworking projects and delve into the different types of lubricants available.
Lubrication plays a crucial role in woodworking, ensuring smooth movement and reducing friction between various parts and surfaces. Without proper lubrication, woodworking tools can become stiff, making it difficult to achieve precise cuts or manipulate materials effectively. Additionally, inadequate lubrication can lead to wear and tear on equipment, requiring more frequent maintenance and potentially affecting the quality of the final product.
A good lube for woodworking not only reduces friction but also protects against corrosion and extends the lifespan of tools and machinery. As woodworkers strive for accuracy and efficiency in their projects, selecting the right lubricant becomes paramount. Different types of lubricants offer unique benefits for woodworking applications, each with its own advantages and disadvantages. By understanding these options and their properties, woodworkers can make informed decisions when choosing a lube that meets their specific needs.
Overall, incorporating proper lubrication techniques into woodworking practices can greatly enhance precision and efficiency while ensuring the longevity of tools. In the following sections of this article, we will explore different types of lubes used in woodworking applications including water-based, oil-based, wax-based, silicone-based, and grease-based options. We will also discuss factors to consider when choosing a good lube for woodworking as well as provide recommendations for top products that meet woodworker expectations.
Moreover, we will explore DIY solutions that are cost-effective and efficient while discussing best practices for applying lubes and common mistakes to avoid. Lastly, our FAQ section aims to address concerns commonly faced by woodworkers regarding lubes.
The Role of Lubrication in Woodworking
Lubrication plays a crucial role in woodworking projects, and using a good lube is essential for several reasons. First and foremost, lubrication helps reduce friction between wood surfaces, allowing tools to glide smoothly during cutting, shaping, and sanding processes. This not only makes the work easier but also prevents unnecessary wear and tear on both the tools and the wood itself.
Moreover, using a good lube in woodworking helps prevent overheating and burning of the wood. When friction builds up between the tool and the wood surface, it can generate excessive heat that can scorch or damage the material. By applying a suitable lubricant, this heat is dispersed more effectively, minimizing any potential damage or discoloration to the wood.
Additionally, lubrication improves precision and accuracy in woodworking projects. By reducing friction, a good lube allows for smoother movements of tools such as saws or chisels, enabling woodworkers to have better control over their cuts or carvings. This enhanced control leads to cleaner lines, more precise details, and an overall higher quality finish in woodworking projects.
Different Types of Lubricants for Woodworking
Woodworking projects often require the use of lubricants to ensure smooth and efficient operation. There are several different types of lubricants available, each with its own advantages and disadvantages. In this section, we will explore and compare the various options to help woodworkers make an informed decision.
One commonly used type of lubricant for woodworking is water-based lubricant. This type of lubricant is popular because it is non-toxic and easy to clean up. It also does not leave a residue behind, which can be beneficial when working with certain types of wood finishes. However, water-based lubricants may not provide as much long-lasting protection as other types, and they can cause swelling or warping in some types of wood if not used carefully.
Another option for woodworkers is oil-based lubricants. These lubricants provide excellent protection against friction and wear, making them ideal for heavy-duty applications. They also offer good penetration into the wood, which can help to moisturize and protect it from drying out. However, oil-based lubricants can be messy to work with and may leave behind a residue that can attract dirt and dust.
Wax-based lubricants are another popular choice among woodworkers. These lubricants provide a smooth finish and help reduce friction during woodworking operations. They are especially effective when used on moving parts such as hinges or slides. Wax-based lubricants also have the advantage of being easy to apply and clean up. However, they may need to be reapplied more frequently than other types of lubes.
Lubricant Type | Advantages | Disadvantages |
---|---|---|
Water-Based | – Non-toxic
| – Less long-lasting protection
|
Oil-Based | – Excellent protection against friction and wear
| – Messy to work with
|
Wax-Based | – Provides a smooth finish
| – May need frequent reapplication |
Water-Based Lubricants
Water-based lubricants are a popular choice for woodworking applications due to their unique properties and advantages. These lubricants, as the name suggests, are primarily water-based, but they also contain additives that enhance their performance in woodworking projects.
One significant advantage of water-based lubricants is that they are environmentally-friendly and non-toxic. Unlike oil-based lubricants, which can be harmful to both human health and the environment, water-based lubes do not emit strong odors or release harmful chemicals. This makes them a safer option for woodworkers who want to prioritize their health and reduce their impact on the environment.
Another advantage of water-based lubricants is that they are easy to clean up. Since they are primarily composed of water, they can be easily wiped off surfaces with a damp cloth or rinsed away with water. This makes them ideal for projects where cleanliness and ease of removal are important factors.
However, water-based lubricants do have some drawbacks compared to other types of lubricants. One disadvantage is that they tend to evaporate more quickly than oil or wax-based lubes. This means that they may require more frequent applications during longer woodworking sessions or projects with extended periods between uses.
Additionally, water-based lubes may not provide as much long-term protection against moisture as oil-based alternatives. While they can still offer some level of moisture resistance, if you’re working in a humid environment or using the wood outdoors, you may need to opt for an oil-based lubricant instead.
Oil-Based Lubricants
Oil-based lubricants have long been a staple in woodworking projects due to their numerous benefits and versatility. These lubricants are typically made from mineral oil or synthetic oils, providing excellent lubrication and protection for various woodworking applications. In this section, we will explore how oil-based lubricants benefit woodworkers and enhance the overall quality of their projects.
One of the primary advantages of using oil-based lubricants in woodworking is their ability to reduce friction. As woodworkers maneuver their tools and equipment through various cuts and joints, friction can cause excess heat and wear on blades and bits. Oil-based lubricants create a protective barrier between the tool and the wood, reducing friction and extending the lifespan of cutting edges. This not only saves time and money on tool replacement but also ensures cleaner, smoother cuts.
Furthermore, oil-based lubricants provide an added layer of moisture resistance to protect against swelling or warping of wood. Wood is susceptible to absorbing moisture, which can lead to unwanted changes in dimensions or surface quality. Applying oil-based lubricant helps seal the wood fibers, preventing moisture ingress while maintaining the natural beauty of the material.
In addition to reducing friction and providing moisture resistance, oil-based lubricants also offer excellent corrosion protection. When working with metal components in woodworking projects, such as saw blades or drill bits, these lubricants help prevent rusting or oxidization by creating a protective film on the surface. This prolongs the life of the tools and keeps them sharp for longer periods.
To summarize, oil-based lubricants play a crucial role in benefiting woodworkers by reducing friction during cutting or shaping processes, imparting moisture resistance to protect against dimensional changes in wood, as well as providing corrosion protection for metal components involved in woodworking projects. With their versatility and effectiveness, it’s no wonder why many professional woodworkers rely on high-quality oil-based lubes to enhance their precision and efficiency.
Advantages of Oil-Based Lubricants in Woodworking |
---|
Reduces friction and extends the lifespan of cutting edges |
Provides moisture resistance to protect against wood swelling or warping |
Offers corrosion protection for metal components in woodworking tools |
Wax-Based Lubricants
When it comes to woodworking, achieving a smooth finish is paramount. This is where wax-based lubricants come into play. These lubricants offer numerous benefits and are widely used by woodworkers to enhance the quality of their projects.
One of the key advantages of wax-based lubricants is their ability to reduce friction during woodworking tasks. The wax creates a thin protective barrier between the wood and the tools, allowing them to glide smoothly over the surface without causing damage or leaving scratches. This not only makes the work process easier but also helps to preserve the integrity of the wood.
In addition to minimizing friction, wax-based lubricants also contribute to a smoother finish on wooden surfaces. When applied correctly, they can fill in small imperfections and pores in the wood, resulting in an even and polished appearance. This is particularly beneficial for woodworking projects that require a high level of precision or aesthetic appeal, such as furniture making or cabinetry.
Woodworkers have several options when it comes to choosing a wax-based lubricant for their projects. Some popular choices include:
- Beeswax: Known for its natural composition and pleasant scent, beeswax offers excellent lubricating properties.
- Carnauba Wax: Derived from palm leaves, carnauba wax is recognized for its hardness and durability.
- Paraffin Wax: A commonly found type of wax, paraffin provides reliable lubrication and is easily accessible.
To apply wax-based lubricants in woodworking, it is important to first clean the surface thoroughly to remove any dirt or debris that could affect the smoothness of the finish. Next, simply rub a thin layer of wax onto the wood using a cloth or brush, making sure to cover all areas evenly. Allow it to dry and then buff the wood with a clean cloth to achieve the desired smoothness and shine.
Overall, wax-based lubricants are an excellent choice for achieving a polished finish in woodworking. Their ability to reduce friction and fill in imperfections makes them indispensable for woodworkers who strive for precision and excellence in their projects. By understanding the advantages of wax-based lubricants and following proper application techniques, woodworkers can elevate the quality of their work and produce stunning pieces that stand the test of time.
Silicone-Based Lubricants
Silicone-based lubricants are a popular choice among woodworkers due to their unique properties and versatility. These lubricants consist of silicone oil as the main ingredient, making them ideal for various woodworking applications. In this section, we will explore the distinct features and benefits of silicone-based lubricants, as well as their specific uses in woodworking projects.
One of the key advantages of silicone-based lubricants is their excellent heat resistance. When working with power tools that generate high temperatures, such as saws or routers, these lubricants can withstand the heat without breaking down or evaporating quickly. This property ensures that the lubricant remains effective throughout the woodworking process, reducing friction and preventing damage to both the tools and the wood.
Furthermore, silicone-based lubricants have exceptional water resistance. They form a protective barrier on the surface of the wood, preventing moisture from seeping in and causing warping or swelling. This makes them an excellent choice for outdoor woodworking projects or when working with wooden items that may be exposed to high humidity environments.
In terms of applications, silicone-based lubricants are commonly used when gluing pieces of wood together. By applying a thin layer of silicone-based lubricant on surfaces that need to be glued, it helps prevent adhesive residue from seeping into unwanted areas and makes it easier to clean up any excess glue.
Additionally, silicone-based lubes can also be used on table saws or band saws to reduce friction between the wood and the blade, resulting in smoother cuts and improved overall performance.
It is important to note that while silicone-based lubes offer many benefits in woodworking projects, they may not be suitable for all situations. For instance, if you plan on using a finish or coating on your woodwork project after applying a silicone-based lubricant, it is recommended to switch to another type of lube as silicone can interfere with certain finishes.
Additionally, silicone-based lubricants may leave a slightly slippery residue on surfaces, so it is essential to wipe off any excess thoroughly to avoid potential safety hazards.
Overall, silicone-based lubricants are a valuable tool in a woodworker’s arsenal, offering excellent heat resistance, water resistance, and versatility in various woodworking applications. By understanding their unique properties and correctly utilizing them in your woodworking projects, you can enhance precision and efficiency while taking care of your tools and materials.
Grease-Based Lubricants
In the world of woodworking, grease-based lubricants are a popular choice due to their ability to reduce friction and ensure precision. These lubricants are made by mixing oil with a thickener, typically a soap or metallic soap, resulting in a semisolid consistency that adheres well to surfaces. This characteristic makes grease-based lubricants ideal for woodworking applications where long-lasting lubrication is needed.
One of the main advantages of using grease-based lubricants in woodworking is their ability to reduce friction. Friction can cause wear and tear on tools and equipment, leading to decreased performance and accuracy. Grease-based lubricants create a protective layer between moving parts, minimizing contact and reducing friction. This not only extends the lifespan of the tools but also helps maintain precise movements during woodworking projects.
Furthermore, grease-based lubricants offer excellent staying power. Unlike other types of lubricants that tend to drip or evaporate over time, greases cling to surfaces, providing long-lasting protection against rust and corrosion. This is particularly important for woodworkers who often work in humid environments that can accelerate metal deterioration. The high viscosity of grease allows it to remain in place even under heavy loads or extreme conditions, ensuring smooth operation and reliable performance.
Advantages | Disadvantages |
---|---|
– Reduces friction | – Can attract dust and debris |
– Provides long-lasting protection against rust and corrosion | – More difficult to clean off surfaces compared to other lubricants |
– Withstands heavy loads and extreme conditions | – May not be suitable for all woodworking applications |
Factors to Consider When Choosing a Good Lube for Woodworking
When it comes to choosing a good lube for woodworking, there are several important factors to consider. These factors include compatibility with different wood types and finishes, safety considerations, and the overall performance of the lubricant. Understanding these factors will ensure that you choose the right lube for your woodworking projects.
Compatibility: One of the first things to consider when choosing a lube for woodworking is its compatibility with different wood types and finishes. Some lubricants may react with certain woods or finishes, leading to discoloration or damage. It’s essential to check that the lube you choose is safe to use on the specific type of wood you’re working with.
Safety: Safety should also be a top priority when selecting a lubricant for woodworking. Some lubricants may contain harmful chemicals or fumes that can be hazardous to your health, especially if they come in contact with your skin or are inhaled during application. Look for lubricants that are labeled as non-toxic and safe for use in woodworking environments.
Performance: The performance of a lubricant is another crucial factor to consider. You want a lube that provides smooth and consistent results, reducing friction and ensuring precision in your woodworking projects. Consider how long the lubricant lasts before needing reapplication and whether it offers any additional benefits such as moisture resistance or rust prevention.
In summary, when choosing a good lube for woodworking, it is vital to consider compatibility with wood types and finishes, safety features, and overall performance. By taking these factors into account, you can select a lubricant that enhances precision and efficiency in your woodworking projects while ensuring safe usage.
Top Recommendations for Good Lubricants in Woodworking
Woodworkers rely on lubricants to enhance the efficiency and precision of their projects. With a wide variety of options available, it can be overwhelming to choose the right lubricant for woodworking applications. In this section, we will review some top recommendations for good lubricants that meet woodworker expectations.
One highly recommended lubricant for woodworking is Boeshield T-9. This product is an oil-based lubricant that offers excellent rust protection and penetration into tight spaces. It leaves behind a protective coating that helps prevent moisture and corrosion, making it ideal for use on saw blades, hand tools, and other wooden surfaces.
Another popular choice among woodworkers is DuPont Teflon Multi-Use Lubricant. This silicone-based lubricant provides long-lasting protection against friction, wear, and moisture. It has a high temperature resistance, making it suitable for use with power tools and machinery in woodworking projects.
For those looking for a water-based option, GlideCote Table & Tool Surface Sealant is highly recommended. This lubricant creates a smooth friction-free surface on table saws, routers, jointers, and other woodworking tools. It helps reduce drag and prevents rust or corrosion from forming on the equipment.
Lubricant | Type | Main Features |
---|---|---|
Boeshield T-9 | Oil-based | Rust protection, penetrates tight spaces |
DuPont Teflon Multi-Use Lubricant | Silicone-based | Friction reduction, high temperature resistance |
GlideCote Table & Tool Surface Sealant | Water-based | Smooth friction-free surface, prevents rust and corrosion |
These lubricants have been praised by woodworkers for their effectiveness and performance in woodworking applications. However, it is important to note that different projects may require different lubricants based on the specific needs of the tools and materials being used. It is always recommended to read product labels and follow manufacturer instructions for optimal results.
In the next section, we will explore DIY lubricants for woodworking, providing cost-effective and efficient alternatives that woodworkers can make themselves using readily available ingredients.
DIY Lubricants for Woodworking
Woodworkers who are looking for a more cost-effective and efficient solution to lubricate their woodworking tools and projects may find DIY lubricants to be a viable option. While there are many commercially available lubricants specifically designed for woodworking, some woodworkers prefer to create their own lubricants using common household ingredients. DIY lubricants can offer a more affordable alternative without compromising the quality of results.
Benefits of DIY Lubricants
One of the main benefits of using DIY lubricants in woodworking is cost-effectiveness. Commercially available lubricants can be expensive, especially for those who regularly engage in woodworking projects. By making your own lubricant, you have control over the ingredients and can choose more budget-friendly options without sacrificing effectiveness.
In addition to cost-effectiveness, DIY lubricants often use simple ingredients that are readily available at home or easily accessible at local stores. This convenience allows woodworkers to quickly create a solution when needed, eliminating the need for a trip to the store or waiting for a delivery.
Common Types of DIY Lubricants
There are several types of homemade lubricants that woodworkers can experiment with:
- Beeswax and Mineral Oil Mixture: Combining melted beeswax with mineral oil creates a paste-like substance that can be used as a general purpose lubricant for wooden surfaces and tools.
- Vegetable Oil: Simple vegetable oil such as coconut oil or olive oil can serve as a temporary lubricant for woodworking projects. It is important to note that vegetable oil may not provide long-lasting effects and may need reapplication after some time.
- Candle Wax: Melting candle wax and applying it onto wooden surfaces can provide temporary smoothness and reduce friction during certain operations, such as sawing or planing.
While these homemade solutions can be effective in certain situations, it is important to test them on scrap pieces of wood before applying them to finished projects. This ensures compatibility and prevents any unwanted effects on the wood.
DIY lubricants can be a cost-effective and efficient option for woodworkers. By utilizing common household ingredients, woodworkers have the flexibility to experiment and find a solution that meets their specific needs. It is recommended to research different recipes and techniques before attempting any homemade lubricants to ensure optimal performance while maintaining the safety and integrity of woodworking projects.
Best Practices and Application Tips for Using Lubricants in Woodworking Projects
Woodworking projects often require the use of lubricants to ensure smooth and precise operations. Whether you are cutting, drilling, or sanding, using a good lube can make a significant difference in the outcome of your project. In this section, we will explore some best practices and application tips for using lubricants in woodworking projects to maximize efficiency and results.
Choose the Right Type of Lubricant
When selecting a lubricant for your woodworking project, it’s important to consider the specific requirements of the task at hand. Different types of lubricants have varying properties that make them more suitable for certain applications.
For example, water-based lubricants are ideal for tasks where cleanup is a concern, while oil-based lubricants provide better protection against wear and tear. Understanding the different types of lubricants available and their characteristics will help you choose the right one for your project.
Apply the Lubricant Correctly
Proper application is crucial when using lubricants in woodworking. One common mistake is overapplying the lubricant, which can lead to messy work surfaces or interfere with adhesives used in later stages of the project.
It’s important to use a moderate amount of lube and apply it precisely to the intended areas. Depending on the task, you may need to apply the lubricant directly onto tools such as saw blades or drill bits, or you may need to apply it onto the surface being worked on.
Regularly Reapply as Needed
Lubrication can wear off over time, especially during prolonged woodworking sessions or when working with high-friction materials. Therefore, it’s important to regularly reapply the lubricant as needed throughout your project. This will help maintain optimal performance and prevent any potential damage caused by friction or heat build-up.
Common Mistakes to Avoid when Using Lubricants in Woodworking
Using the Wrong Type of Lubricant
One common mistake that woodworkers make when using lubricants is using the wrong type of lubricant for their specific woodworking application. It is important to understand that different lubricants have different properties and are designed for specific purposes. Using the wrong type of lubricant can result in inadequate lubrication, poor performance, or even damage to the wood and tools being used.
To avoid this mistake, it is essential to carefully consider the requirements of the woodworking project and choose a lubricant that is compatible with the materials and tools being used. For example, if you are working with hardwoods, an oil-based lubricant may be more suitable as it provides better penetration and protection against friction.
On the other hand, if you are working with sensitive woods or finishes, a water-based lubricant may be a better choice as it won’t affect the appearance or integrity of the wood.
Overusing or Underusing Lubricants
Another common mistake in woodworking is either overusing or underusing lubricants during application. Both scenarios can have negative effects on the overall performance and outcome of your woodworking projects.
Overusing lubricants not only wastes product but can also lead to messy workspaces and potential difficulties in getting a smooth finish. Excessive amounts of lube can attract dirt and debris, creating an abrasive surface that can damage tools or leave unsightly marks on your workpiece.
On the other hand, underusing lubricants may result in insufficient protection against heat and friction, which can lead to increased wear on tools and wood surfaces. It’s important to apply enough lubricant to create a thin film between moving parts while avoiding excess.
Failing to Clean Tools Properly before Application
One often overlooked mistake is failing to properly clean tools before applying any type of lube. Lubrication products should be applied to clean surfaces to ensure proper adhesion and effectiveness. Before applying lubricant, make sure to thoroughly remove any dirt, sawdust, or debris from your tools, as these can interfere with the lube’s performance.
To prevent this mistake, develop a routine of cleaning and maintaining your tools regularly. Use compressed air or a soft brush to remove any loose particles, and wipe down the tools with a cloth dampened with a mild solvent if necessary. By keeping your tools clean, you can optimize their performance and ensure that the lubricant is working as intended.
By avoiding these common mistakes when using lubricants in woodworking projects, you can enhance safety and effectiveness while achieving optimal results. Taking the time to choose the right lubricant for your specific needs, properly applying it without overusing or underusing, and ensuring that tools are clean before application will lead to smoother operations and better outcomes in woodworking projects.
Frequently Asked Questions about Good Lubricants for Woodworking
What are the key characteristics to look for in a good lubricant for woodworking?
When it comes to choosing a good lubricant for woodworking, there are several key characteristics that woodworkers should consider. Firstly, it is important to find a lubricant that is compatible with the specific type of wood you are working with. Different woods have different properties and may react differently to certain types of lubricants. Therefore, it is crucial to select a lubricant that will not damage or negatively affect your woodworking project.
Secondly, safety is of utmost importance when selecting a lubricant. Look for products that are non-toxic and safe to use around food or in enclosed spaces. It is also advisable to choose lubes that do not emit strong odors or harmful fumes. Additionally, consider the environmental impact of the lubricant and opt for eco-friendly options whenever possible.
Lastly, performance is a key factor in selecting a good lubricant. Look for products that provide long-lasting performance and excellent protection against wear and tear. Lubricants with high heat resistance and low friction properties are ideal for woodworking projects as they can help enhance precision, reduce friction, and extend the lifespan of tools and equipment.
Can I use regular household lubricants for woodworking?
While some household lubricants may work adequately for certain woodworking tasks, it is generally recommended to use specialized lubes specifically designed for woodworking applications. Regular household lubes such as cooking oils or WD-40 may not offer the same level of protection and performance as dedicated woodworking lubes.
Woodworking lubes are formulated to be non-staining, non-drying, and provide optimal protection against moisture, heat, and friction – factors that can significantly impact the quality of your projects. These specialized lubes often contain additives that improve their suitability for woodworking tasks like reducing saw blade sticking or preventing rust on tools.
Therefore, investing in quality woodworking lubricants is a wise choice to ensure the best results and protect your woodworking tools and machinery from wear and tear.
How should I apply lubricants in woodworking?
The application of lubricants in woodworking will depend on the specific task at hand. Here are some general guidelines:
- For cutting tools like saw blades or drill bits, apply a small amount of lubricant directly to the cutting edge. This will help reduce friction and heat buildup, resulting in smoother cuts and prolonged tool life.
- To lubricate moving parts or joints, use a small brush or cloth to apply the lubricant evenly along the surfaces that come into contact with each other. Make sure to wipe off any excess lube afterwards to prevent accumulation of dust or debris.
- When using power tools with moving parts like table saws or planers, refer to the manufacturer’s guidelines for recommended lubrication points and intervals. Apply the appropriate lubricant as directed to ensure optimal performance and longevity of your equipment.
Remember to always read the instructions provided by the manufacturer of your chosen lubricant for specific guidance on application methods and quantities.
Conclusion
In conclusion, choosing the right lubricant for woodworking projects can greatly enhance precision and efficiency. With the wide variety of lubricants available, it is important to consider factors such as compatibility, safety, and performance when making a selection.
Water-based lubricants offer advantages such as easy cleanup and non-toxicity, but they may not be suitable for all woodworking applications. Oil-based lubricants are popular among woodworkers due to their ability to penetrate deep into the wood, providing long-lasting lubrication. Wax-based lubricants are known for their ability to provide a smooth finish on woodworking projects.
Silicone-based lubricants offer unique properties such as water resistance and high temperature resistance, making them suitable for specialized woodworking tasks. Grease-based lubricants help reduce friction and ensure precision in woodworking by offering a thick layer of protection.
When choosing a good lube for woodworking, it is important to consider the specific needs of your project and the materials being used. It is also crucial to follow the manufacturer’s instructions and recommendations for safe application.
In addition to commercial lubricant options, some woodworkers may opt for DIY solutions that are cost-effective and efficient. However, it is important to carefully research homemade lubricants and ensure they are safe for use on woodworking projects.
By following best practices and application tips for using lubricants in woodworking projects, woodworkers can maximize efficiency and achieve superior results. It is important to evenly apply the lubes in an appropriate amount to avoid excess buildup or waste.
Overall, finding the perfect lube for woodworking projects can make a significant difference in the outcome of your work. Whether you choose a commercially available product or decide to make your own, careful consideration of factors such as compatibility, safety, and performance will help enhance precision and efficiency in your woodworking endeavors.
Frequently Asked Questions
What is the best lubricant for wood on wood?
When it comes to lubricating wood-on-wood surfaces, one of the best options is beeswax. Beeswax is a natural and safe lubricant for wood that has been used for centuries.
It helps reduce friction and allows wooden components to glide smoothly against each other without causing damage. To apply beeswax to wood-on-wood surfaces, you can rub a small amount directly onto the area or melt it and brush it on with a soft cloth.
What lubricant is safe for wood?
Among the lubricants considered safe for use on wood, one popular choice is silicone spray. Silicone sprays are effective in reducing friction between wood surfaces while being gentle enough not to harm the material.
They provide a smooth surface that allows wooden parts to move more easily without causing any damage or staining. It’s important to choose a silicone spray specifically formulated for fine finishes like furniture wax or polish, as they are designed to be safe for use on various types of woods.
What is the best lubricant for wood screws?
When it comes to lubricating wood screws, paraffin wax often proves to be highly effective. Paraffin wax is commonly used because it provides a thin layer of lubrication that helps prevent screws from getting stuck or damaged when driven into wood. Applying paraffin wax involves rubbing it directly onto the threads of the screw before driving them in.
The wax acts as a temporary coating that reduces friction between the screw and the wood, making installation smoother and easier. Additionally, since paraffin wax is relatively inexpensive and easy to find at hardware stores, it has become a go-to choice for many DIY enthusiasts when dealing with woodworking projects involving screws.
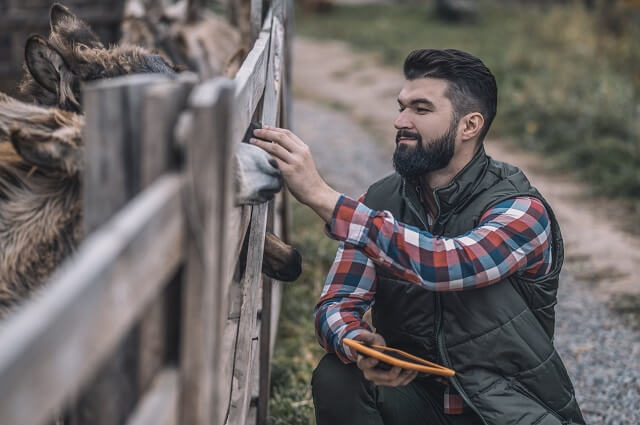
Hi everyone! I’m a woodworker and blogger, and this is my woodworking blog. In my blog, I share tips and tricks for woodworkers of all skill levels, as well as project ideas that you can try yourself.