What is CMC machinery for woodworking? CMC, or Computer Numerical Control, machinery is a type of automated equipment used in woodworking processes. This article aims to provide a comprehensive understanding of CMC machinery, covering its history, functionality, advantages, common types and applications, key considerations when choosing the right equipment, as well as maintenance and care tips.
The use of CMC machinery in the woodworking industry has revolutionized traditional methods and significantly improved efficiency and precision. From its early beginnings to the emerging trends and technologies in the future, this article will delve into the basics of CMC machinery for woodworking.
By exploring the history and evolution of CMC machinery in the woodworking industry, readers will gain insight into how this technology has developed over time to become an indispensable tool for woodworkers. Understanding the functionality and components of CMC machinery will also provide a solid foundation for appreciating its advantages and applications in various woodworking processes.
The History and Evolution of CMC Machinery in the Woodworking Industry
CMC machinery for woodworking has a long and fascinating history that has evolved over time to meet the demands of the industry. The use of machinery in woodworking dates back to ancient times, with early civilizations utilizing simple tools such as saws, chisels, and hand drills to craft wood. However, as the demand for intricately designed and mass-produced wooden products grew, there arose a need for more efficient and precise machinery.
The Industrial Revolution marked a significant turning point in the history of CMC machinery for woodworking. During this period, the development of steam-powered machines revolutionized the woodworking industry, allowing for large-scale production and increased efficiency. This era saw the emergence of various types of machinery such as lathes, planers, and routers, which paved the way for modern CMC machinery used today.
The evolution of CMC machinery in the woodworking industry continued with advancements in technology and automation. With the introduction of computer numerical control (CNC) technology, woodworking machinery became even more precise and versatile. CNC machines have become vital in modern woodworking operations, offering unparalleled accuracy and productivity. Today, CMC machinery continues to evolve with cutting-edge technologies such as 3D printing and advanced robotics making their way into woodworking processes.
- Woodworking machinery during ancient civilizations
- Impact of Industrial Revolution on woodworking machinery
- Advancements in technology leading to CNC machines
The Functionality and Components of CMC Machinery for Woodworking
One of the key components of CMC machinery for woodworking is the controller, which is essentially the brain of the equipment. The controller interprets the CAD/CAM design and converts it into specific movements and actions for the machine to execute. Additionally, motors and drives are essential components that provide the necessary power and motion for cutting, shaping, and carving wood according to the programmed specifications.
Another important aspect is the tooling system within CMC machinery. This includes various types of cutting tools such as end mills, router bits, drills, and saw blades. These tools are carefully selected based on factors like material type, desired finish quality, and specific cutting requirements. In conjunction with the tooling system, a well-designed holding mechanism or workpiece fixture ensures that the wood being processed remains secure and stable during machining operations.
Overall, understanding the functionality and components of CMC machinery for woodworking is fundamental in optimizing its performance and achieving high-quality outputs.
Functionality | Components |
---|---|
Automation of woodworking processes | Controller (CAD/CAM), Motors & Drives |
Precision cutting and shaping | Tooling System (End Mills, Router Bits), Workpiece Fixture |
Advantages of Using CMC Machinery in Woodworking Processes
CMC machinery for woodworking brings several advantages to the industry, making it an essential tool for modern woodworkers. One of the primary advantages is its ability to automate and streamline various woodworking processes, resulting in increased efficiency and productivity. With CMC machinery, tasks such as cutting, shaping, and milling can be performed with precision and speed, reducing the time and labor required for these tasks.
In addition to improving efficiency, CMC machinery also enhances the overall quality of woodworking products. The advanced technology and precision of CMC machinery ensure that each piece of wood is processed with accuracy, leading to high-quality finished products. This is particularly crucial for woodworking businesses that prioritize craftsmanship and attention to detail.
Furthermore, using CMC machinery in woodworking processes can also contribute to cost savings in the long run. While the initial investment in CMC machinery may seem substantial, the reduction in labor costs and waste materials, as well as the increased output, ultimately result in significant cost savings for woodworking businesses.
Lastly, CMC machinery enables woodworkers to explore more complex and intricate designs that may be challenging or impossible to achieve manually. This capability opens up new creative possibilities for woodworkers, allowing them to expand their product offerings and cater to a wider range of customer demands.
Advantages | Details |
---|---|
Increased Efficiency | Automation streamlines woodworking processes |
Enhanced Product Quality | Precision technology ensures high-quality finished products |
Cost Savings | Reduction in labor costs and waste materials leads to overall cost savings |
Creative Possibilities | Enables exploration of complex designs for expanded product offerings |
Common Types of CMC Machinery for Woodworking and Their Applications
When it comes to woodworking, CMC (Computer Numerical Control) machinery plays a crucial role in enhancing precision, efficiency, and consistency in various woodworking processes. CMC machinery for woodworking encompasses a wide range of equipment that is designed to automate and optimize cutting, shaping, carving, and other manufacturing processes. In this section, we will explore the common types of CMC machinery used in woodworking and their applications.
CNC Routers
CNC routers are one of the most commonly used types of CMC machinery in woodworking. These machines use computer-aided design (CAD) software to precisely cut, carve, and shape wood materials. CNC routers are versatile and can be used for various woodworking applications such as cabinetry, furniture making, sign making, and architectural millwork.
CNC Lathes
CNC lathes are specialized CMC machinery used for turning wood materials to create cylindrical or round parts such as table legs, balusters, and spindles. These machines provide high accuracy and repeatability in shaping wooden components, making them essential for producing intricate designs and details in woodworking projects.
CNC Panel Saws
CNC panel saws are designed for accurately cutting large sheets of wood panels or plywood into smaller pieces with precise dimensions. These machines are commonly used in cabinetmaking, furniture production, and carpentry workshops to streamline the cutting process and minimize material waste.
These are just a few examples of the many types of CMC machinery available for woodworking applications. Each type of machine offers unique capabilities to meet specific manufacturing needs within the woodworking industry. Understanding the different types of CMC machinery and their applications is essential when considering investment in this technology for your woodworking business or workshop.
Key Considerations When Choosing CMC Machinery for Woodworking
When choosing CMC machinery for woodworking, there are several key considerations to keep in mind to ensure that you make the right investment for your woodworking processes. From the size and capacity of the machinery to its efficiency and capability, here are some important factors to consider when choosing CMC machinery for woodworking.
Size and Capacity
One of the first things to consider when choosing CMC machinery for woodworking is the size and capacity of the equipment. This includes understanding the dimensions of the machinery and how it will fit into your workspace, as well as its capacity to handle the volume of wood materials you plan to work with. It’s important to choose machinery that not only fits your current needs but also has the potential to accommodate future growth in your woodworking operations.
Efficiency and Capability
Another crucial consideration is the efficiency and capability of the CMC machinery for woodworking. This encompasses factors such as speed, precision, and versatility in handling different types of woodworking tasks. The machinery should be able to deliver high-quality results while optimizing production processes for maximum output.
Technology and Automation
In today’s modern woodworking industry, technology and automation play a significant role in enhancing productivity and quality. When choosing CMC machinery for woodworking, it’s essential to assess the technological features and automation capabilities that can streamline your operations. From CNC-based controls to advanced software integration, investing in machinery with cutting-edge technology can propel your woodworking processes to new heights.
Considering these key factors when choosing CMC machinery for woodworking is essential for making a well-informed decision that aligns with your production goals and operational requirements. By evaluating each aspect thoroughly, you can select equipment that not only meets your current needs but also sets the foundation for future success in the woodworking industry.
Maintenance and Care Tips for CMC Machinery in Woodworking
When it comes to maintaining CMC machinery for woodworking, proper care and regular maintenance are essential to ensure optimal performance and longevity of the equipment. Here are some key tips to keep your CMC machinery in top condition:
1. Regular Cleaning: It is important to regularly clean the CMC machinery to remove any sawdust, debris, or residue that may accumulate during the woodworking process. Use a soft brush or vacuum to clean the machine thoroughly, paying special attention to moving parts and components.
2. Lubrication: Proper lubrication of the moving parts is crucial for the smooth operation of CMC machinery. Be sure to follow the manufacturer’s recommendations for lubrication intervals and use high-quality lubricants suitable for woodworking machinery.
3. Inspection and Maintenance Schedule: Create a regular inspection and maintenance schedule for your CMC machinery, including checking for loose bolts, worn-out belts, or any signs of wear and tear. This will help identify potential issues early on and prevent costly repairs down the line.
4. Operator Training: Proper training of operators is vital in ensuring the safe and efficient use of CMC machinery. Make sure that all operators are trained in equipment operation, safety protocols, and basic troubleshooting.
By following these maintenance and care tips, you can ensure that your CMC machinery for woodworking remains in excellent condition, delivering reliable performance for years to come.
The Future of CMC Machinery in Woodworking
In conclusion, the future of CMC machinery in woodworking holds exciting possibilities with emerging trends and technologies that are set to revolutionize the industry. As advancements in automation, robotics, and artificial intelligence continue to progress, the integration of these technologies into CMC machinery is expected to streamline and optimize woodworking processes even further. This can result in increased efficiency, precision, and productivity for woodworkers, ultimately leading to enhanced quality of output.
One of the key emerging trends to watch out for in the future of CMC machinery for woodworking is the utilization of smart technology and data analytics. This will enable CMC machinery to gather and analyze real-time data from woodworking processes, allowing for predictive maintenance, error detection, and performance optimization. Additionally, the incorporation of 3D printing technology into CMC machinery may offer new possibilities for creating intricate wood designs and components with unprecedented accuracy and speed.
As we look ahead, sustainability is also anticipated to play a significant role in shaping the future of CMC machinery in woodworking. With a growing emphasis on eco-friendly practices and materials within the industry, CMC machinery may see developments that focus on reducing waste, energy consumption, and environmental impact.
By embracing these trends and technologies, woodworkers can expect CMC machinery to continue empowering them with innovative solutions that enhance their craft while meeting evolving market demands. In essence, what is CMC machinery for woodworking today may evolve into an indispensable tool that drives creativity and efficiency in tomorrow’s woodworking industry.
Frequently Asked Questions
What Machine Is Used in Wood Workshop?
In a wood workshop, various machines are used for different purposes. Common machines include table saws, band saws, planers, jointers, and sanders. These machines help in cutting, shaping, and smoothing the wood for various projects.
What Is a Wood Combination Machine?
A wood combination machine is a woodworking tool that combines multiple functions into one unit. This can include a combination of operations like sawing, planing, drilling, and mortising. These machines are popular in small workshops where space is limited.
What Is the Meaning of Wood Work Machine?
The term “woodwork machine” refers to any type of machinery or power tool used in the process of working with wood. This can encompass a wide range of equipment including saws, routers, lathes, sanders, and drills. These machines are essential for efficiently shaping and finishing wood projects.
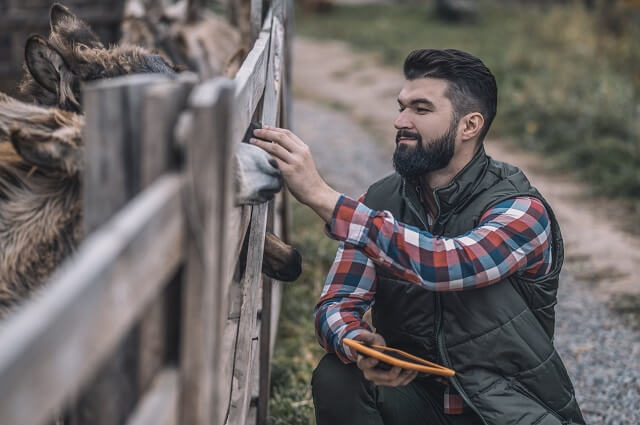
Hi everyone! I’m a woodworker and blogger, and this is my woodworking blog. In my blog, I share tips and tricks for woodworkers of all skill levels, as well as project ideas that you can try yourself.