Woodworkers should know the basics of plywood, its popularity among woodworkers and a brief history of its evolution. Plywood is a versatile and widely-used material in woodworking projects due to its strength, stability, and affordability. Understanding the different types of plywood, such as exterior, interior, marine, and structural plywood, can help woodworkers choose the right materials for their projects.
This article will also cover the pros and cons of using plywood in woodworking, as well as tips for choosing the right plywood for specific applications. By gaining knowledge about plywood, woodworkers can harness its power in various projects and explore endless possibilities.
Types of Plywood
Exterior plywood: Ideal for outdoor projects
Exterior plywood is specifically designed to withstand the elements and is commonly used in outdoor projects such as decks, fences, and exterior furniture. It is manufactured with a weather-resistant adhesive that allows it to withstand moisture, humidity, and temperature variations without warping or delaminating. Exterior plywood is usually made with a higher grade of wood veneer on the outer layers to enhance its durability and resistance to decay.
To ensure the best performance in outdoor applications, it is important to choose exterior plywood that is properly sealed and finished. This will help protect it from water damage and extend its lifespan. Applying a waterproof sealant or paint can be beneficial in preventing moisture absorption and ensuring the longevity of your outdoor projects.
Interior plywood: Versatile and suitable for various applications
Interior plywood is highly versatile, making it suitable for a wide range of woodworking projects. It comes in different grades and can be used for anything from cabinets, furniture, flooring, wall paneling, doors, and much more. Interior plywood typically has a smooth finish on both sides and may have fewer blemishes compared to exterior plywood.
One advantage of using interior plywood is its affordability compared to solid wood options. It also offers increased dimensional stability when compared to solid wood, meaning it is less prone to warping or shrinking due to changes in humidity or temperature.
Marine plywood: Water-resistant and highly durable
Marine plywood is specifically manufactured for use in marine environments where constant exposure to water or high humidity levels are expected. It features a special waterproof glue that makes it highly resistant to rotting or delaminating even when submerged underwater for extended periods.
This type of plywood typically has superior-quality veneer faces that are free from defects such as knots or voids. Marine-grade lumber is often required for boat building projects due to its exceptional strength properties as well as its ability to resist decay caused by water exposure.
Structural plywood: Designed for load-bearing purposes
Structural plywood is engineered to carry heavy loads and is often used in construction and structural applications. It is made with thicker layers of veneer and high-quality adhesive that gives it exceptional strength, stiffness, and stability.
One key characteristic of structural plywood is its ability to distribute weight evenly across its surface, making it suitable for flooring, roofing, sheathing, and other load-bearing installations. It is important to note that structural plywood should be used in accordance with local building codes and guidelines to ensure safety and compliance.
Understanding the different grades and veneer patterns
Plywood comes in various grades that denote the quality of the wood veneers used on the faces and core layers. The grading system generally ranges from A to D, with A being the highest quality and D representing a lower quality or structural grade.
The appearance of plywood can vary depending on the arrangement of wood veneers on its outer layers. Different patterns such as rotary-cut, plain-sliced (also known as flat-cut), quarter-sawn, rift-sawn, or combination cuts can result in distinct aesthetics.
Woodworkers may choose a specific veneer pattern based on their desired visual effect for the project at hand. For example, quarter-sawn veneer patterns are known for their straight grain appearance while rotary-cut patterns exhibit a more pronounced natural figure.
When selecting plywood for your project, it is essential to consider both the grade and veneer pattern that best suit your specific needs in terms of strength, aesthetics, and budget.
Type of Plywood | Features | Common Applications |
---|---|---|
Exterior Plywood | – Weather-resistant adhesive\n – Higher-grade veneer on outer layers\n – Resistant to moisture and decay | – Outdoor furniture\n – Decks and fences\n – Exterior structures |
Interior Plywood | – Smooth finish on both sides\n – Versatile and affordable\n – Increased dimensional stability | – Cabinets and furniture\n – Wall paneling\n – Flooring and doors |
Marine Plywood | – Special waterproof glue\n – Resistant to rotting and delamination\n – Superior-quality veneer faces | – Boat building projects\n – Water-resistant applications |
Structural Plywood | – Thicker layers for added strength\n – Even weight distribution\n – High-stiffness and stability | – Construction and structural applications\n – Flooring, roofing, sheathing |
Pros and Cons of Using Plywood in Woodworking Projects
Plywood is a widely used material in woodworking projects due to its various advantages. However, it also has its drawbacks that woodworkers should be aware of before incorporating it into their projects.
Advantages of plywood
One of the main advantages of plywood is its strength. Plywood is made by layering thin sheets of wood veneer together with adhesive, which creates a strong and durable material. This makes it ideal for structural applications where strength is crucial, such as in building shelves, cabinets, and furniture.
In addition to its strength, plywood also offers stability. Unlike solid wood, plywood is less prone to warping or shrinking when exposed to changes in temperature or humidity. This stability makes it a reliable choice for woodworking projects that require dimensional accuracy over time.
Another key advantage of plywood is its affordability. Compared to solid wood, plywood tends to be more cost-effective. It allows woodworkers on a budget to still create quality pieces without breaking the bank. Additionally, because plywood is made from layers of veneer rather than whole logs, it can be produced from smaller trees, making it a more sustainable option.
Drawbacks of plywood
Despite its many advantages, there are some drawbacks to using plywood in woodworking projects. One common issue with plywood is the possibility of delamination. Delamination occurs when the layers separate due to moisture exposure or improper handling. This can weaken the structure and compromise the integrity of the project if not addressed promptly.
Another limitation of using plywood relates to aesthetic options. Many woodworkers appreciate the natural beauty and grain patterns found in solid wood. While some higher-end varieties of plywood may offer attractive veneers, they generally provide fewer options compared to working with solid wood species.
Additionally, while many consider the affordability of plywood an advantage, others may argue that cheaper grades of plywood can lack the same level of quality and durability as solid wood. It is essential to understand the different grades and select plywood that meets the specific needs of the project.
By weighing these pros and cons, woodworkers can make informed decisions when considering plywood for their woodworking projects.
Choosing the Right Plywood for Your Project
When it comes to choosing the right plywood for your woodworking project, there are several factors that need to be considered. From determining the desired strength and durability to considering the appearance and finish, making an informed decision will ensure the success of your project. Additionally, understanding the impact of veneer patterns on aesthetics and decoding the grading system is crucial in selecting the best plywood for your needs.
One of the first considerations when choosing plywood is determining the desired strength and durability required for your project. Different types of plywood have varying levels of strength and are designed to withstand different loads. If you’re working on a project that requires load-bearing capabilities, structural plywood would be appropriate. On the other hand, if your project will be exposed to moisture or outdoor elements, marine plywood with its water-resistant properties would be a better choice.
The appearance and finish of your final product also play a significant role in selecting plywood. Interior plywood with a smooth surface is suitable for projects that will require painting or staining since it provides a clean canvas for these finishes.
However, if you prefer a natural wood finish or want to showcase interesting grain patterns, choosing plywood with an attractive veneer pattern is essential. Veneer patterns can range from simple grains like birch or maple to more exotic options like oak or mahogany, providing endless possibilities for customization.
Understanding the grading system is another important factor in choosing plywood. Plywood grades indicate the quality of the wood veneers used in its construction. Higher grades such as A or B mean fewer visible defects and higher quality veneers. These grades are ideal for projects where appearance matters, such as furniture-making or cabinetry. Lower grades like C or D may have more visible defects but can still serve well in applications where strength is more important than aesthetics.
By carefully considering factors such as desired strength and durability, appearance and finish preferences, as well as understanding the grading system, you can select the right plywood for your woodworking project. Taking the time to choose the appropriate plywood will ensure that your project not only looks great but also performs well and stands the test of time.
Proper Handling and Storage of Plywood
Plywood is a versatile and popular material choice for woodworkers due to its strength, stability, and affordability. However, in order to maintain the quality and integrity of plywood sheets, it is crucial to handle and store them properly. Improper handling and storage can lead to warping, damage, or even delamination of the sheets. Here are some important tips to ensure the proper handling and storage of plywood:
- Storing plywood: Proper storage is key to preventing warping or damage to the sheets. Plywood should be stored in a dry, well-ventilated area with temperature and humidity control if possible. It is important to keep the sheets flat by storing them horizontally on a level surface. If vertical storage is necessary due to limited space, ensure that the sheets are adequately supported with no overhanging edges.
- Handling precautions: When moving or transporting plywood sheets, be careful not to drop or pile heavy objects on top of them as it can cause damage or breakage. Avoid dragging the sheets on rough surfaces as it can scratch or dent the surface. Use caution when using tools such as saws or drills near the edges of the plywood to avoid accidental damage.
- Preventing moisture absorption: Plywood is susceptible to moisture absorption which can lead to warping or mold growth. To prevent this, avoid storing plywood in humid or damp environments. If the sheets do become wet, allow them to dry completely before stacking or installing them. It may also be helpful to seal all exposed edges with a waterproof sealant.
Tips for Proper Handling and Storage of Plywood |
---|
Store plywood in a dry, well-ventilated area |
Keep sheets flat and level during storage |
Avoid dropping or piling heavy objects on top of plywood |
Avoid dragging plywood on rough surfaces |
Seal all exposed edges to prevent moisture absorption |
Following these guidelines for proper handling and storage will help to maintain the quality of plywood sheets, ensuring they are ready to be used in woodworking projects without warping, damage, or delamination. By taking the time to handle and store plywood correctly, woodworkers can maximize its durability and longevity in their projects.
Techniques for Cutting and Joining Plywood
Choosing the Appropriate Tools for Cutting Plywood
When it comes to cutting plywood, using the right tools is crucial to achieving clean and accurate cuts. One of the most common tools used for cutting plywood is a circular saw.
When selecting a circular saw blade, it is important to choose one with a high tooth count, typically around 60 to 80 teeth, as this will help to minimize tear-out and create a smoother edge. It is also recommended to use a straight edge or a guide when using a circular saw to ensure straight cuts.
Another tool that can be used for cutting plywood is a table saw. Table saws provide stability and accuracy, making them ideal for larger woodworking projects. To achieve precise cuts with a table saw, it is essential to use a rip fence or miter gauge to guide the plywood through the blade. This will help to maintain uniformity in the cuts.
For more intricate cuts or curves, a jigsaw can be employed. Jigsaws are versatile and allow woodworkers to navigate tight corners and irregular shapes easily. When using a jigsaw, it is advisable to use a finer-toothed blade for cleaner results.
Best Practices for Achieving Clean and Accurate Cuts
To achieve clean and accurate cuts in plywood, there are several best practices that woodworkers should follow. First, it is crucial to measure and mark the dimensions accurately before cutting. Using a square or measuring tools can help ensure precision.
Before making any cuts on plywood, it is also recommended to score the cut line lightly with a utility knife. This will help prevent tear-out by creating an indentation that guides the blade while cutting.
Additionally, when using power tools such as circular saws or table saws, it is essential to move the sheet slowly through the blade, maintaining controlled movement throughout the process. Rushing through cuts can result in rough or uneven edges.
Lastly, preventing tear-out can be achieved by supporting the plywood properly during cutting. Using sawhorses or a stable workbench will minimize vibration and provide a secure surface for cutting, resulting in cleaner cuts.
Different Joining Methods for Plywood: Nails, Screws, and Adhesives
Joining plywood is an essential aspect of woodworking projects. There are several methods that woodworkers can utilize to join plywood pieces together effectively.
One common method is using nails or screws to secure the plywood joints. When working with thinner sheets of plywood, it is best to use nails as they are less likely to split the wood. For thicker plywood, screws with pre-drilled holes are recommended. Pre-drilling prevents splitting and ensures a tight joint.
Another popular joining method is using adhesives such as wood glue or construction adhesive. Adhesives provide strength and flexibility in joining plywood pieces without the need for visible fasteners. When using adhesives, it is crucial to apply even pressure to the joint area while allowing sufficient drying time for optimal bonding.
For stronger joints, combining mechanical fasteners with adhesives can provide added stability. This method involves securing the plywood pieces with nails or screws first, followed by applying adhesive along the joints for enhanced durability.
To reinforce the joints further and prevent splitting in high-stress areas, woodworkers may opt for using wooden dowels or biscuits. These small wooden inserts act as additional support and help strengthen the joint over time.
By utilizing these various cutting and joining techniques for plywood, woodworkers can ensure accurate cuts and sturdy connections in their woodworking projects.
Finishing Plywood
Sanding Techniques for a Smooth Surface
When it comes to finishing plywood, sanding is an essential step to achieve a smooth and polished surface. Before sanding, ensure that the plywood is clean and free from any dirt or debris. Start with a coarser grit sandpaper, around 80 or 100-grit, to remove any rough patches or imperfections on the surface. Use long, even strokes in the direction of the grain to prevent scratches.
After sanding with the coarse grit, gradually move to finer grits such as 120-grit and 220-grit. This will help to further smoothen the surface and eliminate any visible scratches from the previous sanding. Always remember to sand with the grain of the wood and avoid applying too much pressure as this can cause unevenness.
Staining, Painting, and Varnishing Options for Plywood
One of the advantages of using plywood in woodworking projects is its versatility when it comes to finishes. Plywood can be stained, painted, or varnished according to your desired aesthetic.
If you prefer a natural wood look while still protecting the surface from damage and wear, staining is a great option. Before staining, make sure to apply a pre-stain conditioner to prevent blotchiness. Apply your chosen stain evenly with a brush or rag and allow it to fully dry before applying a protective topcoat.
Painting plywood offers endless possibilities for adding color and character to your projects. Start by priming the surface with a good quality primer specifically designed for wood surfaces. After that, you can apply latex or oil-based paint using brushes or rollers for an even application.
For those who want a glossy sheen and enhanced durability, varnishing is the way to go. Opt for either water-based or oil-based varnish depending on your preferences. Apply thin coats of varnish using a brush, allowing each coat to dry completely before applying the next. Sand lightly with fine-grit sandpaper between coats for a smoother finish.
Sealants and Protective Coatings to Enhance Durability
To further enhance the durability of plywood and protect it from moisture damage, consider using sealants and protective coatings. These options can help prolong the lifespan of your woodworking projects.
One popular choice is polyurethane, which provides a hard and durable finish that resists scratches and stains. Apply multiple thin coats using a brush or roller, ensuring proper drying time between each coat. Polyurethane can come in different finishes such as matte, satin, or gloss, allowing you to achieve the desired look for your project.
Another effective option is epoxy resin, which creates a strong protective layer on the plywood surface. Epoxy is highly resistant to water, chemicals, and UV rays. It can also provide a glossy finish that enhances the natural beauty of the wood grain. Follow the manufacturer’s instructions carefully when working with epoxy resin and be sure to properly prepare the surface before application.
Remember to always work in a well-ventilated area when applying sealants or protective coatings and follow safety guidelines provided by the manufacturers.
Common Mistakes to Avoid When Using Plywood
When it comes to using plywood in woodworking projects, there are a few common mistakes that woodworkers should be aware of and avoid. These mistakes can affect the overall quality and durability of the finished piece. By understanding these potential pitfalls, woodworkers can ensure they make the most out of their plywood and create high-quality projects.
One common mistake is overlooking the importance of quality and grading when selecting plywood. Plywood comes in a variety of grades, ranging from A to D, with A being the highest quality and D being the lowest. It is important to select plywood that is appropriate for the intended use of the project. Ignoring this can result in weakened structures or poor aesthetics.
Improper storage and handling of plywood can also lead to issues such as warped sheets. Plywood is susceptible to warping if exposed to changes in temperature and humidity. It is crucial to store plywood properly in a cool, dry place with even support along its entire length. Additionally, proper handling techniques should be employed to prevent damage during transport and installation.
Another mistake that woodworkers should avoid is neglecting proper sealing and finishing techniques. Plywood has a tendency to absorb moisture if not properly sealed, leading to swelling or delamination over time. Applying sealants or protective coatings helps protect against moisture damage, providing longevity for your project.
Lastly, failing to reinforce joints and corners effectively can be a significant mistake when working with plywood. Plywood tends to be more vulnerable at the edges where it may split or splinter if not reinforced properly. Using suitable reinforcement methods such as nails, screws, or adhesives will provide strength and stability for your project.
By being mindful of these common mistakes, woodworkers can maximize the potential of plywood in their projects. Understanding how to choose the right grade, handle and store plywood correctly, apply proper seals and finishes, as well as reinforce joints effectively will result in high-quality, durable pieces that will stand the test of time.
Frequently Asked Questions about Plywood
Woodworkers often have questions about plywood and its suitability for different projects. Here are answers to some of the most frequently asked questions about plywood:
Can plywood be used for outdoor furniture?
Yes, plywood can be used for outdoor furniture, provided that it is the right type of plywood. Exterior plywood is specifically designed for outdoor use as it is made with glue that can withstand exposure to moisture and weather elements. It is also important to properly seal and finish the plywood to ensure its longevity in outdoor conditions.
Is plywood suitable for kitchen cabinets?
Plywood is a popular choice for kitchen cabinets due to its strength and stability. Interior plywood, which is commonly used for cabinetry, provides a solid base and can withstand the weight of heavy countertops and appliances. It also has the advantage of being more affordable compared to solid wood options while still offering durability.
How to repair delaminated plywood?
Delamination occurs when the layers or plies of plywood start to separate from each other, leading to weakened structural integrity. To repair delaminated plywood, start by removing any loose or damaged sections of the ply using a chisel or scraper. Apply a good-quality wood glue onto both surfaces and press them together firmly using clamps or weights. Allow sufficient time for the glue to dry before sanding and applying any necessary finishes.
What is the difference between plywood and MDF?
Plywood and Medium-Density Fiberboard (MDF) are two commonly used materials in woodworking projects, but they have distinct differences. Plywood consists of thin layers of wood veneers bonded together with adhesive, offering strength and stability in all directions.
MDF, on the other hand, is composed of fine wood fibers mixed with glue and pressed into solid panels. While plywood is known for its durability and ability to hold screws securely, MDF has a smoother surface ideal for painting and intricate designs but is not as strong as plywood.
By addressing these frequently asked questions, woodworkers can make informed decisions when using plywood in their projects. Remember that the suitability of plywood for specific applications may vary depending on factors such as the type, grade, and finish. With proper knowledge and understanding, woodworkers can maximize the benefits and potential of plywood in their woodworking endeavors.
Conclusion
In conclusion, plywood is a highly versatile and popular material among woodworkers for good reason. It offers a wide range of benefits, including strength, stability, affordability, and durability. Throughout history, plywood has evolved to meet the needs of different applications and projects.
When choosing plywood for your woodworking project, it is important to consider factors such as desired strength, appearance, and veneer patterns. Understanding the grading system can also guide you in selecting the best plywood for your specific requirements.
Proper handling and storage of plywood are crucial in preventing warping and damage to the sheets. Additionally, techniques for cutting and joining plywood should be mastered to achieve clean and accurate cuts as well as strong joints.
Finishing techniques such as sanding, staining, painting, and varnishing can enhance the appearance and durability of plywood. It is important not to overlook these steps as they contribute significantly to the overall quality of your project.
Frequently Asked Questions
What is the basic knowledge of plywood?
Plywood is a type of engineered wood that consists of layers or plies of wood veneer bonded together with adhesive. These layers are stacked in alternating directions, which gives plywood its strength and stability.
The number of layers can vary, but plywood typically has an odd number of layers to prevent warping. It is widely used for various applications such as construction, furniture, cabinets, and packaging due to its durability and versatility.
How can you tell good quality plywood?
There are several ways to determine if plywood is good quality or not. One important factor is the thickness and number of plies. Good quality plywood tends to have more plies, which increases its strength and stability.
The adhesive used to bond the veneer should be evenly spread without any visible gaps or voids. Additionally, high-grade plywood often has a smooth surface without any rough patches or unevenness. It should also be free from knots or defects that could weaken the overall structure.
What are the 5 grades of plywood?
Plywood is graded based on its appearance and intended use. The five grades commonly used are A, B, C, D, and X. Grade A represents the highest quality with a nearly perfect appearance and few defects visible on both sides of the plywood sheet. Grade B may have some minor defects but still maintains good overall appearance; it is often used for furniture or cabinetry where one side will be visible.
Grade C is considered utility grade and may have more noticeable defects but still retains structural integrity, making it suitable for sheathing or subflooring purposes. Grade D has visible defects that may affect its strength and can be used for temporary structures or non-structural applications where appearance is not important. Lastly, grade X indicates that one side of the plywood sheet meets the requirements for a specific type of surface finish, such as being paintable or suitable for laminating.
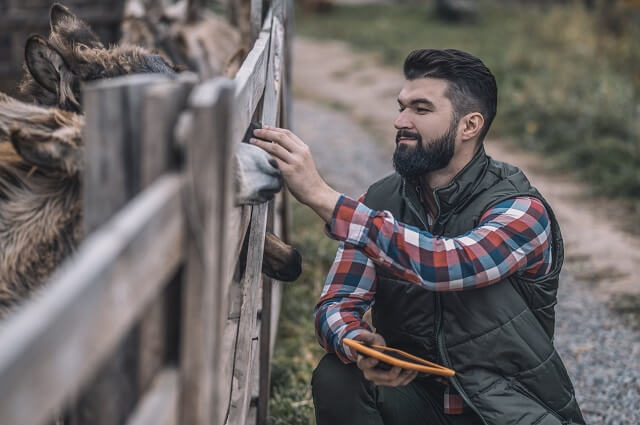
Hi everyone! I’m a woodworker and blogger, and this is my woodworking blog. In my blog, I share tips and tricks for woodworkers of all skill levels, as well as project ideas that you can try yourself.