Woodworking has long been revered as a timeless craft, steeped in tradition and expertise. However, in recent years, there has been a noticeable surge in the use of epoxy within the woodworking community. Epoxy, known for its strong adhesive properties and versatility, has found its way into various applications, from filling cracks and knots to creating unique resin art pieces. Despite its growing popularity, there are valid reasons why one might question the use of epoxy in woodworking.
Woodworking has always placed great emphasis on traditional techniques that have stood the test of time for centuries. These methods have been refined over generations and require a high level of craftsmanship and skill. By contrast, epoxy seems to offer a quick fix or shortcut that deviates from the authenticity and dedication ingrained in traditional woodworking practices.
Moreover, the charm of woodworking lies in its ability to showcase natural wood’s innate beauty – its warmth, grain patterns, and distinct character. Wood has an intrinsic connection to nature that resonates with many enthusiasts. However, epoxy coatings can often mask this natural appeal with their glossy sheen or unnatural colors. This deviation from pure wood aesthetics prompts us to question whether epoxy is truly compatible with the artistic vision of woodworking.
The Importance of Traditional Woodworking Techniques
Woodworking is a craft that has been handed down through generations, relying on time-honored techniques and skills that have proven their worth over centuries. Traditional woodworking techniques not only create beautiful, functional pieces but also provide a connection to the rich history and heritage of this craft. While epoxy has gained popularity in recent years, it is important to recognize the value of these traditional methods and their impact on woodworking.
One of the key benefits of traditional woodworking techniques is the authenticity and natural beauty they bring to furniture and other woodworking projects. When working with natural wood, craftsmen can showcase the unique characteristics and charm that come from each individual piece.
The grain patterns, knots, and colors of different woods give each project its own personality and story. In contrast, epoxy may detract from this aesthetic by creating a uniform, artificial appearance that lacks the warmth and character found in natural wood.
In addition to the aesthetic appeal, sustainability and environmental considerations are crucial factors in choosing traditional woodworking techniques over epoxy. Wood is a renewable resource when sourced responsibly, making it an environmentally friendly material choice. On the other hand, epoxy production requires chemicals that can have harmful effects on the environment during manufacturing as well as disposal. By embracing traditional woodworking methods and using sustainable wood sources, craftsmen can contribute to a more eco-friendly approach in their projects.
Traditional joinery techniques also offer structural integrity and longevity that may surpass those achieved through epoxy-based bonding methods. Techniques such as dovetails, mortise and tenon joints, and finger joints have stood the test of time for their strength and durability. These types of joinery create connections between wood pieces that become even stronger over time as wood naturally expands and contracts with changing humidity levels.
Epoxy adhesives may introduce potential weaknesses into woodwork due to issues like yellowing or cracking over time. Therefore, relying on traditional joinery ensures long-lasting structural integrity in woodworking projects.
Authenticity and Natural Beauty
The Unique Charm of Natural Wood
Natural wood has a unique charm and warmth that is unparalleled. It brings a sense of authenticity and connection to nature, creating furniture and woodworking projects that are not only functional but also visually appealing. The patterns of the grain, the variation in color, and the natural imperfections all contribute to the beauty of wood.
Woodworking enthusiasts often appreciate the process of selecting wood for their projects, carefully considering factors such as species, grain orientation, and figuring. Additionally, working with wood allows artisans to bring out its natural beauty through techniques like hand carving, shaping, and finishing. These processes allow for a deep appreciation of woodworking as an art form.
Epoxy: A Detractor from Natural Beauty
While epoxy has gained popularity in woodworking for its versatility and strength properties, it may detract from the authentic and natural aesthetic that many craftsmen strive for. Epoxy coatings can create a glossy or glass-like finish that covers up the unique characteristics of wood. The transparency of epoxy may not always reveal the true depth and complexity of the grain pattern or allow it to interact with light in the same way as untreated wood.
Moreover, epoxy can fill gaps or cracks in wood, making it appear flawless on the surface but potentially masking interesting features like knots or burls. This uniformity achieved through epoxy application can sometimes lead to a loss of character and individuality in woodworking projects.
Preserving Authenticity in Woodworking
For those who value authenticity and natural beauty in their woodworking projects, traditional finishing methods such as oil-based finishes or shellac may be preferred over epoxy. These finishes enhance rather than mask the natural features of wood while providing protection against wear and tear.
Furthermore, embracing the uniqueness of each piece of wood by showcasing its imperfections can add character and warmth to furniture and other woodworking creations. By using traditional woodworking techniques and finishes, craftsmen can highlight the beauty of natural wood and create pieces that stand apart from the mass-produced, uniform designs seen in many modern settings.
Sustainability and Environmental Considerations
As the world becomes more aware of the environmental impact of various industries, it is crucial to examine the sustainability and environmental considerations of using epoxy in woodworking. Epoxy is a synthetic material that is commonly used as an adhesive or coating in woodworking projects. However, its production, usage, and disposal can have detrimental effects on the environment.
Firstly, the production of epoxy involves the use of petrochemicals and other potentially harmful substances. These chemicals are non-renewable resources that contribute to greenhouse gas emissions and depletion of natural resources. Additionally, the manufacturing process often involves energy-intensive procedures that further contribute to carbon emissions.
Moreover, using epoxy in woodworking not only has environmental implications during production but also during usage. Epoxy releases volatile organic compounds (VOCs) into the air during application and curing processes. These VOCs can have adverse effects on indoor air quality and human health. Furthermore, when epoxy-coated wood items reach their end-of-life stage or require refinishing, disposing of them becomes a challenge as they cannot be easily recycled or decomposed.
To address these sustainability concerns, alternative eco-friendly materials and techniques are gaining popularity in woodworking. One such material is natural oils or finishes made from renewable sources such as linseed oil or tung oil. These finishes not only provide protection but also enhance the beauty of wood while being environmentally friendly.
Furthermore, traditional joinery techniques can be employed instead of relying on epoxy-based bonding methods. Traditional joints like dovetails, mortise and tenon, and finger joints offer exceptional strength and durability without resorting to synthetic adhesives or coatings.
Structural Integrity and Longevity
One of the primary concerns with using epoxy in woodworking is its long-term durability. While epoxy can provide a strong bond initially, there are potential issues that may arise over time. One such issue is yellowing. Epoxy has a tendency to yellow and become discolored when exposed to UV light. This can significantly impact the aesthetic appeal of the woodwork, especially if it was intended to showcase the natural beauty of the wood.
Another concern is cracking. Epoxy has a relatively low elasticity compared to wood, which means that it may not be able to withstand changes in temperature or humidity as well as traditional joinery methods. This can lead to cracks developing in the epoxy over time, compromising the structural integrity of the piece.
Delamination is also a potential weakness associated with epoxy use in woodworking. If not properly applied or if there are inconsistencies in the surface preparation, epoxy may fail to adhere securely to the wood substrate. This can result in layers of epoxy separating from each other or from the wood itself, leading to significant damage and reducing the overall lifespan of the piece.
To address these concerns, it is crucial for woodworkers considering using epoxy to carefully evaluate their specific project requirements and select appropriate epoxy products that offer superior UV resistance and flexibility. Additionally, thorough surface preparation and application techniques should be followed diligently to ensure proper adhesion between the wood and epoxy.
In summary, while epoxy can provide initial strength and stability in woodworking projects, it is important for craftspeople to weigh its potential weaknesses against alternative traditional joinery methods. By considering aspects such as yellowing, cracking, and delamination, informed decisions can be made about whether or not to incorporate epoxy into their woodworking practices.
Structural Integrity and Longevity: Addressing the concerns regarding the long-term durability and potential weaknesses that epoxy may introduce into woodwork, such as yellowing, cracking, or delamination.
One of the primary concerns with using epoxy in woodworking is its long-term durability. While epoxy can provide a strong bond initially, there are potential issues that may arise over time. One such issue is yellowing. Epoxy has a tendency to yellow and become discolored when exposed to UV light. This can significantly impact the aesthetic appeal of the woodwork, especially if it was intended to showcase the natural beauty of the wood.
Another concern is cracking. Epoxy has a relatively low elasticity compared to wood, which means that it may not be able to withstand changes in temperature or humidity as well as traditional joinery methods. This can lead to cracks developing in the epoxy over time, compromising the structural integrity of the piece.
Delamination is also a potential weakness associated with epoxy use in woodworking. If not properly applied or if there are inconsistencies in the surface preparation, epoxy may fail to adhere securely to the wood substrate. This can result in layers of epoxy separating from each other or from the wood itself, leading to significant damage and reducing the overall lifespan of the piece.
Versatility of Traditional Joinery
Traditional woodworking techniques have stood the test of time for centuries, and one of their notable strengths lies in the versatility and strength of traditional joinery. Joinery refers to the method used to connect two or more pieces of wood together, and it plays a crucial role in determining the structural integrity and longevity of a woodworking project.
In contrast to epoxy-based bonding methods, traditional joinery techniques like dovetails, mortise and tenon, and finger joints offer several advantages that make them highly valued by woodworking purists.
Dovetail joints are renowned for their strength and durability. They consist of interlocking fan-shaped tails on one piece of wood that fit into corresponding notches on another piece, creating an incredibly strong bond. This type of joint is often used in drawer construction because it can withstand repeated use without loosening or falling apart.
The mortise and tenon joint is another staple in traditional woodworking that provides exceptional strength. It involves a square or rectangular hole (the mortise) cut into one piece of wood, into which a projecting tongue (the tenon) from another piece is inserted. The combination of this tight-fit connection plus glue results in a joint that can resist considerable stress.
Finger joints, also known as box joints, create connections by interlocking alternating rectangular cuts on the ends of two pieces of wood. This type of joint provides an extremely large gluing surface area, distributing weight evenly across the joint and increasing its overall strength.
Joint | Description | Advantages |
---|---|---|
Dovetail Joint | A strong joint with interlocking fan-shaped tails. | Excellent durability; withstands repeated use without loosening. |
Mortise and Tenon Joint | A joint created by inserting a projecting tongue into a square or rectangular hole. | Exceptional strength; resists considerable stress. |
Finger Joint (Box Joint) | Interlocking alternating rectangular cuts create the joint. | Large gluing surface area enhances strength and weight distribution. |
These traditional joinery techniques not only provide structural integrity, but they also contribute to the aesthetic appeal of woodworking projects. The visible joinery serves as an indicator of the craftsmanship and skills involved in creating each piece. Additionally, these joints allow for disassembly and repair if necessary, providing versatility that epoxy-based bonding methods may lack.
While epoxy can be a useful tool in certain applications or as an accent material, it is important to recognize and appreciate the versatile and strong nature of traditional joinery in woodworking. These time-honored techniques not only ensure the longevity of furniture and other woodworking projects but also contribute to their artistic value and charm.
Appreciation of Handcrafted Artistry
Woodworking is a craft that has long been celebrated for its attention to detail, skillful techniques, and the unique artistry behind each handcrafted piece. From intricate carvings to meticulously crafted joints, woodworking showcases the beauty of natural wood and the dedication of its makers. It is in this appreciation of handcrafted artistry that some traditionalists question the use of epoxy in woodworking.
One of the key reasons why many craftsmen are hesitant to incorporate epoxy into their projects is because it can potentially detract from the uniqueness and individuality of each handcrafted piece. Woodworkers take pride in creating one-of-a-kind items that celebrate the natural characteristics and imperfections of wood.
The application of epoxy resin can create a glossy, uniform surface that may diminish the charm and character inherent in wood’s natural grain patterns or distinctive markings. This can result in a more generic appearance that lacks the depth and richness typically associated with traditional woodworking.
Furthermore, epoxy has become increasingly popular for creating river tables or filling voids within a wooden surface. While these creations can be visually striking, they often rely on uniform colors or various additives mixed with epoxy to achieve desired effects. As a result, they tend to have a more manufactured appearance compared to pieces where emphasis is placed solely on highlighting the natural beauty of wood through careful craftsmanship.
Many woodworkers believe that embracing imperfections and working with what nature provides adds authenticity to their pieces. Each knot, crack, or irregularity tells a story about the life cycle of a tree, bringing depth and character to finished furniture or other woodwork projects. By contrast, using epoxy to fill or cover imperfections masks these natural traits, leading to a more manufactured look.
Natural Aging and Patina
Wood is a living material that ages and develops character over time, creating a beautiful patina that enhances its authenticity and connection to nature. This natural aging process is highly valued in woodworking, as it showcases the unique story of each piece of wood and adds depth to the finished project. In contrast, epoxy-coated surfaces tend to have a more static appearance, which can detract from the organic charm that wood brings to furniture and other woodworking projects.
The Beauty of Wood Patina
One of the most alluring aspects of using natural wood in woodworking is its ability to develop a rich patina over time. As wood ages, it undergoes subtle changes in color and texture, which contribute to its unique character. It acquires a deeper tone, highlighting the grain patterns and adding depth to the overall aesthetic. This natural aging process cannot be replicated by any other material or finish.
Connection to Nature
Wood is a product of nature itself, having grown slowly over many years before being harvested for use in woodworking projects. It carries with it a sense of history and a connection to the outdoors that cannot be replicated by synthetic materials. When woodworking enthusiasts choose to forgo epoxy coatings, they are preserving this authentic connection to nature in their creations, allowing the beauty of nature’s creation to shine through.
Contrasting Epoxy-Coated Surfaces
In contrast to the natural aging process of wood, epoxy-coated surfaces tend to have a more predictable and static appearance. While epoxy can provide protection and durability to woodwork, it often leaves behind a glossy or plastic-like finish that lacks the warmth and individuality found in aging wood. The uniformity of epoxy finishes can sometimes overshadow the unique characteristics that make each piece of wood special.
Overall, the natural aging process and patina that occur in wooden surfaces are highly valued by traditionalists in woodworking. They appreciate the authentic connection to nature, the individuality of each piece, and the depth of character that wood brings to their creations. While epoxy may have its place in certain applications or as an accent material, the desire to preserve and celebrate these natural qualities is why many traditionalists choose to avoid its use in woodworking projects.
Conclusion
In conclusion, it is evident that traditionalists in woodworking may have valid reasons to avoid the use of epoxy in their craft. The importance of preserving and honoring time-honored woodworking techniques cannot be undermined. These methods have been passed down for centuries, and they contribute to the authenticity and natural beauty that wood brings to furniture and other projects.
Moreover, sustainability and environmental considerations cannot be taken lightly. Epoxy production, usage, and disposal all have potential negative impacts on the environment. Exploring alternative, eco-friendly materials and techniques may therefore be a more responsible choice for woodworkers who prioritize sustainability.
Beyond these practical concerns, traditional woodworking joints offer unmatched versatility and strength compared to epoxy-based bonding methods. Dovetails, mortise and tenon, and finger joints are examples of craftsmanship that has stood the test of time. They not only add structural integrity but also showcase the skill and artistry involved in woodworking.
However, it would be remiss not to acknowledge that epoxy does have its place in certain applications or as an accent material. In specific instances where strength or water resistance is necessary, epoxy can provide unique benefits. Additionally, using epoxy as an accent material may allow woodworkers to experiment with new artistic possibilities while still honoring traditional techniques.
Ultimately, the decision to use or avoid epoxy in woodworking should be based on personal preferences and project requirements. While some may opt for the charm and warmth of natural wood, others may find value in exploring the possibilities offered by this modern material. As with any craft rooted in tradition, striking a balance between heritage and innovation is key for woodworkers seeking to create timeless pieces of artistry.
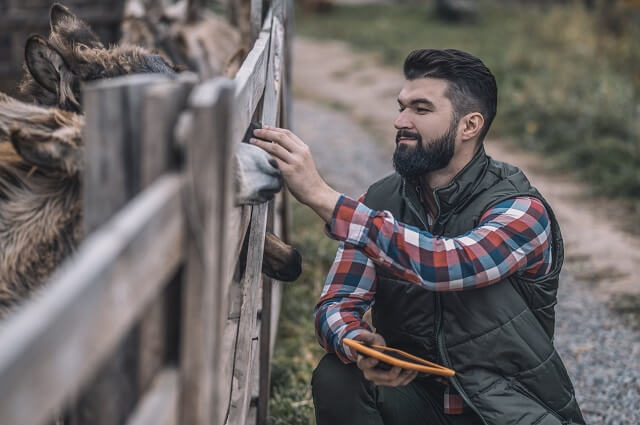
Hi everyone! I’m a woodworker and blogger, and this is my woodworking blog. In my blog, I share tips and tricks for woodworkers of all skill levels, as well as project ideas that you can try yourself.