Introduction
Woodworking is a timeless art that has been practiced by craftsmen and hobbyists alike for centuries. It can range from simple tasks of carving wooden pieces to intricate designs that require multiple steps and tools. Regardless of the project, woodworking is an enjoyable activity with a potential to create something both beautiful and practical. But there are also certain tricks, tips, and secrets that experienced carpenters have learned over the years that can make all the difference between success and failure in craftsmanship.
Knowing the best tips, tricks and secrets when it comes to woodworking can help any individual take their projects to the next level. First off, it helps one understand complex concepts more quickly. With all the variables when it comes to size, shape, joints and materials used, having all of this information organized is paramount, this will help avoid unnecessary mistakes and give you peace of mind as you work on each individual piece. Additionally, Woodworking Tips Tricks and Secrets will enable you to maximize tool efficiency; working smarter not harder! This means having better handle on things like proper routing techniques or cutting methodologies which save time spent on projects. With routines down pat in such valuable detail one can produce easier but also much higher quality finished products in far less time than before. Finally keeping yourself informed on technology advancements that pertain to what you do will always help stay current with industry standards as well as keeping your head in leaderboard rankings if being competitive is something desired!
Preparing Your Woodworking Project
Preparing Your Woodworking Project: Gather Essential Tools ” It is important to gather the essential tools needed for your project from the start. Many woodworking projects will require the use of saws, drills, sanders and other common tools. Make sure to get the right size for each job, as it will make it easier to do a quality job in a timely manner.
Choosing the Right Wood for the Job” When beginning any woodworking project is important to select an appropriate type of wood that can hold up to wear and tear. Different woods have different characteristics such as hardness, durability, moisture resistance and ability to change with time. Knowing what qualities you need will help you choose the right wood for your project.
How To Maintain Structural Integrity From The Start ” To ensure that your woodworking project has a solid foundation with no weak points it is important to take precautions such as using the right screws and bolts when assembling parts, using glue where necessary and checking that planks are properly lined up before inserting nails or screws into them. Additionally make sure all pieces fit snugly before proceeding with construction as this can help prevent warped boards in later stages of assembly.
Finishing Touches
Finishing touches are often the most time consuming yet rewarding steps of any woodworking project. When it come to finishes, various options exist from natural oils, paints and laminates to more specialist varnishes, waxes and glazes. As different woods require different treatments, it’s worth researching what works best for each species before commencing a project. For example some softer woods respond well to waxing but wouldn’t stand up to furniture polish.
Sanding and polishing are also key in providing an aesthetically pleasing finish as any remaining splinters or bumps can quickly ruin the final look. Sandpaper comes in many forms with the coarseness designating which stage of sanding you should use on a particular area – starting off with a rougher grade before graduating down to smoother ones. Research or ask advice on how fine each stage should be, as over-polishing can result in an undesirable shine.
Finally many woodworkers choose to stain their work as it adds colour and makes the grain pattern stand out more visibly – although staining can add another layer of complexity! Different techniques such as wiping or brushing on with long strokes ensure consistency of shade when compared to dipping sections into a container of stain. Furthermore there are other products available that recreate unique effects such as patterns of streaks or darker corners – adding flair and originality that can set a piece apart from the rest!
Safety Tips
Safety is of paramount importance when it comes to woodworking. It is important to always wear the appropriate gear, such as safety glasses and/or a face shield and hearing protection, when working with tools and machines. Additionally, you should always be cautious when handling power tools, as there are many potential hazards that can arise from improper use. Make sure to read all of the safety instructions provided by the manufacturers before starting any project. Furthermore, remember to never leave a tool running or unattended while in use, shut off any tools after finishing a job so you do not forget them turned on again later, and always unplug tools between uses. Have an open mind for ongoing learning to ensure best practice methods are applied in your shop. Taking these simple precautions should help make certain that each day in the workshop is a safe one.
Troubleshooting
Troubleshooting imperfections quickly is key for any woodworking project. The most common way to do this is to carefully inspect the parts and pieces as soon as they are cut or milled, noting down any flaws that may prevent the assembly from being successful. Where possible it can be useful to work with scrap pieces of wood and experiment with different solutions until you find one that works best.
Identifying weak joints is a crucial step in making sure the final product will be of high quality. Weak joints can appear due to improper measurements, incorrect angles, split or damaged timber, or poor glue applications. Never be tempted to rush your joints”carefully measure twice and cut once to ensure accuracy when putting them together.
When troubleshooting common problems such as sticking drawers or doors, don’t become frustrated and try applying different finishes in order to improve friction. Waxes can also be used in order to make surfaces easier to maneuver into position, whilst lubricants such as powder graphite offer excellent solutions for stiff hinges and movement issues caused by humidity levels or extreme temperatures changes.
Wood Carving and Sculpting
When it comes to wood carving and sculpting, there are many techniques that can help you achieve stylish and unique results. The key is to master the basic techniques first, before moving onto more complex shapes. Carving is both an art and a craft that requires practice and patience. For the beginner woodcarver, here is a step-by-step guide on how to carve intricate shapes with professional results:
1. Start by selecting the right tools: Before starting a project, select appropriate carving tools such as chisels, V-tools, gouges, and knives depending on what kind of project you’re working on. Consider the types of wood you’ll be using because different types of woods require different techniques and levels of guidance for the tools. Make sure the edges are smooth in order to avoid splintering when cutting into the wood.
2. Draw reference lines or patterns: Before you start carving, it is important to know where your cuts need to go. This is best accomplished by drawing out plans or patterns which will act as a guide for you as you work your way through the sculpture. It is possible to create imaginative designs from scratch but it saves time if you have something prepared beforehand as your guideline during construction.
3 Score along lines: When finished with drawing out your plans/patterns then use them to think about what type of cuts should be made in order to achieve desired result. Use a wooden mallet and chisel or V-tool to score along these predetermined lines in order to make visible divisions between shapes that need to be cut away later on down carving path (which will depend on type of shape being carved).
4 Cut away shape: Now based off those scores from before work away at removing portions that do not belong in design rather than cutting into wider sections; this will make it easier for end result come out looking much smoother overall when finished! Also take care not too rush – slow consistent strokes mean better precision accuracy!
5 Sand & finish as desired: Finally after all desired cutting/shaping/smoothing has been completed sand down any rough edges & clean up surface before applying sealant/paint etc..(depending on end goal look) Take potential material shrinkage into account while finishing project so design won’t appear distorted over time due lack support! With all these simple steps followed correctly no doubt one’s sculpture will turn out looking truly spectacular!
Advanced Woodworking Techniques
Introduction to Woodturning: If you want to take your woodworking skillset to the next level, consider learning how to use a lathe. Woodturning is an art form of turning cylindrical pieces of wood into decorative items such as bowls, plates, and spindles. This technique requires extreme precision and skill to create beautifully symmetrical shapes and curves.
Exploring Inlay Designs and Intarsia: With this advanced woodworking technique, you can learn how to add beautiful inlaid designs or intarsia patterns into your furniture or other projects. This intricate process adds a touch of character and class to your hand-crafted masterpieces.
Woodburning Basics: Woodburning is a popular method of applying color patterns directly onto the surface of the wood without having to paint it afterward. There are several different types of tools used for this skill including etching pens and stencils, which allow you to craft more detailed designs with little effort.
Tips to Minimize Waste
Creative Uses for Wood Scraps: Woodworking typically produces quite a large amount of scraps that are often just thrown away or set aside for disposal. However, with a bit of creativity and resourcefulness, these wood pieces can be put to good use. Repurposing wood scraps or off-cuts into smaller projects like birdhouses, decorative boxes, planters, and other merchandise is one way to make sure they don’t go to waste. Also consider cutting the small wood pieces into confetti-like shapes and using them as packing material; this is especially useful around the holidays when shipping gifts!
Splices Vs. Scarf Joints: Understanding the strengths of both splices and scarf joints is key when deciding how best to join two pieces of lumber together. Splices require little skill while still providing solid results; however, if aesthetics are important in a project, then a scarf joint might be a better option due its blend with the wood grain across its length once finished properly. Additionally, scarf joints work great for longer spans needing added strength but must be crafted correctly to avoid splitting or cracking.
Crafting Professional Looking Miters: To craft professional looking mitered corners can take some practice on your part as it requires precise angles and sharp cuts that fit together snugly. Before making each cut it’s important measure out your materials accurately and mark them accordingly with quick references points like snap lines or scribe marks. Use an appropriate saw for the task – handsaws work great for tight corners – and ensure you always cut away from yourself for safety purposes. Smoothing out any jagged edges with sandpaper helps finish up the project perfectly!
Secrets to Professional Results
Applying Glue Like an Expert:
Using the right glue and applying it carefully is essential to ensure successful stick results. The choice of glue usually depends on the type of wood being used, as different woods require different types of adhesive. After selecting an appropriate glue, identify which parts need to be glued together by marking them with a pencil, which also helps keep track of which sides have been spread with glue. To ensure good contact between the surfaces and efficient adhesion, use a cloth, roller or brush to evenly spread all sides involved prior to pressing them together for assembly. In the case of very porous wood pieces, pre-wetting those surfaces will help reduce absorption levels, ensuring successful binding.
Unveiling the Secret to Professional Quality Joint Fitting:
The secret to a perfect fit is all in accurate cutting and joining techniques. Cut each piece accurately according to plan before fitting. Make sure grooves are cut evenly and square-shouldered mortises are properly centered around their corners with exact wall thicknesses for maximum strength in assembly. Test fit each joint on its two corresponding mating surfaces reassuring tight tolerances before applying adhesive for actual assembly. Additionally, practice designing wooden structures like trees and rafts so you can assess a variety of joint combinations that best suit your project needs.
Tuning Up Your Machines for Maximum Performance:
Machine maintenance is key in order to keep machines running smoothly while avoiding any potential safety risks when working in the workshop- always double check if machines are correctly adjusted prior to use! For saws, cautiously adjust fences using careful measurements based on angles realized in workpieces’ shapes or designs; use sharp blades only (replacing/optimizing teeth sharpness every other week); set depth accurately by covering teeth most appropriately when performing specific cuts; apply correct speed settings depending on usability; besides don’t forget about cleaning after each use! Moreover double check router’s cutting height is properly aligned before commencing from structure building projects; select enough speed; clear off router bit well after cuttings for improved results when switching bits; and when taking off dust happily recollect it with provisions like vacuum cleaners or even dust masks whenever necessary!
Conclusion
The tips, tricks and secrets learned from woodworking can be invaluable for craftspeople of all skill levels. From beginner to advanced, knowledge is power in the world of woodworking. First, it is important to keep safety at the forefront when using tools or working with materials. Always wear protective equipment, such as gloves and goggles, and read the manufacturer’s manual before using any tools. Second, choose good quality materials and plan the project thoroughly with accurate measurements and drawings. Third, practice makes perfect so taking on small projects to gain experience before attempting larger ones is a great idea. Finally, recognize that common mistakes are part of learning so don’t give up after running into problems during a project. With these tips in mind, anyone can become an expert woodworker!
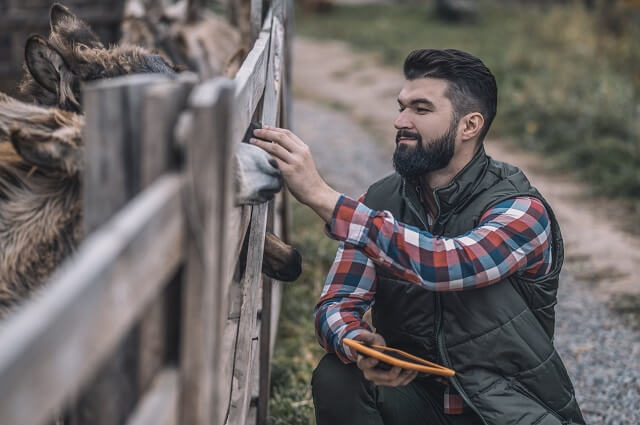
Hi everyone! I’m a woodworker and blogger, and this is my woodworking blog. In my blog, I share tips and tricks for woodworkers of all skill levels, as well as project ideas that you can try yourself.