Woodworking is a rewarding and fulfilling craft, but it also presents a variety of potential safety hazards that must be carefully addressed. From the operation of machinery to the handling of materials, a woodworking environment requires strict adherence to safety protocols to prevent accidents and injuries. Understanding the importance of safety in this setting is crucial for both experienced woodworkers and those new to the trade.
In this article, we will explore the common safety hazards found in woodworking environments and discuss the proper use of personal protective equipment (PPE). We will also highlight the significance of maintaining and inspecting woodworking machinery for safety, as well as best practices for handling and disposing of materials and waste. Additionally, we will delve into emergency preparedness and response, the role of proper ventilation and air quality, and implementing a safety training program for woodworking employees.
Whether you are an individual woodworker or manage employees in a woodworking facility, prioritizing safety is essential. By understanding and addressing potential risks, we can create a safer environment for everyone involved in the woodworking process. Let’s delve into these critical topics to ensure that safety remains at the forefront of our woodworking practices.
Common Safety Hazards in a Woodworking Environment
Woodworking environments present a variety of potential safety hazards that employees need to be aware of and prepared for. Understanding these hazards is crucial in order to prevent accidents and ensure a safe working environment. Some common safety hazards in a woodworking environment include:
1. Exposure to harmful dust and fumes: Woodworking processes such as sawing, sanding, and drilling can generate fine dust particles and fumes that can pose respiratory health risks if inhaled over time.
2. Machine-related injuries: Working with woodworking machinery, such as table saws, band saws, and routers, presents the risk of lacerations, amputations, and other serious injuries if not operated properly.
3. Fire hazards: Wood dust is highly flammable and can pose a fire hazard if proper housekeeping practices are not maintained or if there are equipment malfunctions.
In order to address these safety hazards effectively, it is important for woodworking employees to be well-trained on safety protocols and for employers to implement comprehensive safety measures in the workplace.
To mitigate the risks associated with these common safety hazards, woodworking employees should follow strict safety guidelines and utilize personal protective equipment (PPE) at all times while performing their duties. This includes wearing respirators or masks to protect against inhaling hazardous dust or fumes, as well as using goggles, gloves, and hearing protection when operating woodworking machinery.
By being proactive and vigilant about identifying and addressing these common safety hazards, employers can create a safer working environment for their woodworking employees.
Proper Use of Personal Protective Equipment (PPE) in Woodworking
Understanding the Importance of PPE
Woodworking involves various tools and machinery that can pose serious risks to workers if proper precautions are not taken. PPE serves as the first line of defense against potential hazards, such as flying wood chips, dust, noise, and more. Understanding the importance of wearing appropriate PPE is essential for all individuals working in or around a woodworking environment.
Types of PPE for Woodworking
Several types of personal protective equipment are essential for workers in a woodworking environment. These may include safety glasses or goggles to protect the eyes from flying debris and sawdust, hearing protection to minimize the risk of hearing loss due to loud machinery, respiratory protection to prevent inhalation of harmful dust particles, and gloves to shield the hands from cuts and splinters.
Proper Care and Maintenance
It is important for employees to understand how to properly care for and maintain their PPE. Regular inspection and replacement of damaged or worn-out equipment are crucial to ensure its effectiveness. Additionally, providing training on how to correctly fit and use each piece of protective gear is critical for maximizing its protective benefits.
Overall, prioritizing the proper use of personal protective equipment in a woodworking environmental presents a variety of potential safety benefits for workers. By understanding the importance of PPE, utilizing the appropriate gear, and maintaining it properly, employees can reduce their risk of injury and illness while working with wood materials.
Importance of Maintaining and Inspecting Woodworking Machinery for Safety
Woodworking machinery plays a crucial role in the production process, but it also presents potential safety hazards that must be closely monitored. The maintenance and inspection of woodworking machinery are essential aspects of ensuring a safe working environment for employees. Failure to properly maintain and inspect machinery can result in accidents, injuries, and even fatalities.
One of the most common causes of woodworking machinery accidents is the lack of regular maintenance and inspection. Over time, wear and tear can affect the performance of machinery, increasing the risk of malfunction. In addition, improper maintenance can lead to unexpected breakdowns, putting workers at risk of injury as they attempt to troubleshoot or repair the equipment.
To prevent these risks, employers should implement a rigorous maintenance schedule for all woodworking machinery. Regular inspections should be conducted to identify any signs of wear, damage, or malfunction. Any issues should be promptly addressed by qualified technicians to ensure that the machinery operates safely and efficiently. By prioritizing maintenance and inspection, employers demonstrate their commitment to the well-being of their employees in a woodworking environmental presents a variety of potential safety hazards.
It’s important to note that proper training on machinery operation and maintenance is equally critical in preventing accidents related to woodworking equipment. Employees should be educated on best practices for using machinery safely as well as how to recognize signs that indicate the need for maintenance or repair. This proactive approach not only reduces the likelihood of accidents but also promotes a culture of safety within the workplace.
Woodworking Machinery Maintenance | Importance |
---|---|
Regular inspections | Identify signs of wear and malfunction |
Employer responsibility | Demonstrate commitment to employee safety |
Proper training | Prevent accidents related to equipment use |
Best Practices for Handling and Disposing of Woodworking Materials and Waste
Woodworking materials and waste must be handled and disposed of with great care in order to maintain a safe and healthy environment. Implementing best practices for the handling and disposal of these materials helps to minimize potential safety hazards and environmental impacts. Here are some key best practices to follow:
- Proper storage: Store woodworking materials in designated areas that are away from walkways and emergency exits. This helps reduce the risk of tripping or falling over materials, as well as ensures easy access in case of an emergency.
- Waste management: Set up a system for segregating wood scraps, sawdust, and other waste materials. Recycling or repurposing wood waste whenever possible can help minimize environmental impact.
- Safe disposal: Dispose of woodworking waste in accordance with local regulations. This may involve arranging for regular collection by a licensed waste management company.
- Hazardous material handling: For any hazardous woodworking materials, such as finishes or adhesives, it is important to follow proper handling procedures outlined by the material safety data sheet (MSDS).
By following these best practices, woodworking businesses can ensure a safer work environment for their employees while also minimizing their impact on the environment.
It is also important to provide training to employees on the proper handling and disposal of woodworking materials and waste. This training should cover topics such as:
- Identifying different types of woodworking materials and their associated hazards
- Using appropriate containers for storing wood waste
- Following procedures for safe disposal of hazardous woodworking materials
By implementing these best practices and providing thorough training, businesses can effectively manage woodworking materials and waste in a safe and environmentally responsible manner.
Emergency Preparedness and Response in a Woodworking Environment
Woodworking environments present a variety of potential safety hazards, and being prepared for emergencies is crucial. It is important to have an emergency preparedness plan in place to ensure the safety of employees and minimize the impact of any unforeseen events.
One of the key aspects of emergency preparedness in a woodworking environment is having clear evacuation procedures in case of fire or other emergencies. This includes regular drills to ensure that all employees are familiar with the evacuation routes and procedures.
In addition to having evacuation procedures in place, woodworking facilities should also have plans for responding to accidents or injuries. This can include providing first aid training to employees, ensuring that first aid kits are readily available, and designating individuals who are responsible for coordinating emergency response efforts. By being proactive and well-prepared, woodworking facilities can minimize the impact of accidents and respond effectively in the event of an emergency.
Furthermore, it is crucial to have measures in place for handling hazardous materials commonly used in woodworking processes. This includes having protocols for containing spills or leaks, as well as providing appropriate training on how to handle these materials safely. By implementing these measures and ensuring that employees are well-trained, woodworking facilities can reduce the risk of accidents and ensure a safe working environment.
Aspect | Importance |
---|---|
Evacuation Procedures | Crucial for ensuring employee safety during emergencies |
First Aid Training | Essential for responding to accidents or injuries effectively |
Handling Hazardous Materials | Key for minimizing the risk of accidents related to hazardous substances |
The Role of Proper Ventilation and Air Quality in Woodworking Safety
Woodworking environments can pose a variety of potential safety hazards, including those related to air quality and ventilation. The presence of wood dust and other airborne particles in woodworking shops can have serious health implications for employees if not properly mitigated. Therefore, the role of proper ventilation and air quality in ensuring the safety of workers in a woodworking environment is crucial.
Health Hazards of Poor Air Quality
Inadequate ventilation in a woodworking space can lead to the accumulation of wood dust, which may cause respiratory issues such as asthma and bronchitis, as well as more serious conditions such as nasal cancer or chronic obstructive pulmonary disease (COPD). Additionally, poor air quality can also lead to eye irritation, headaches, and allergies among woodworking employees. It is essential for employers to recognize these potential health hazards and take proactive measures to protect their workers.
Importance of Proper Ventilation
Proper ventilation systems are essential for removing airborne contaminants from a woodworking environment. These systems help to control the level of wood dust in the air, thereby reducing the risk of respiratory issues for employees. Employers should invest in high-quality ventilation systems that are capable of efficiently capturing and removing wood dust from the workplace. Adequate airflow and circulation within the workspace are also crucial for maintaining good air quality.
Monitoring Air Quality
Regular monitoring of air quality is essential to ensure that woodworking environments meet safety standards. This may involve conducting air quality tests at regular intervals to assess the level of wood dust and other contaminants present in the air. If elevated levels are detected, employers must take immediate steps to improve ventilation and mitigate any health risks associated with poor air quality.
By prioritizing proper ventilation and air quality in woodworking environments, employers can effectively safeguard the health and well-being of their employees from potential respiratory hazards associated with wood dust and other airborne particles. Implementing robust ventilation systems, monitoring air quality regularly, and providing necessary protective equipment are important steps towards creating a safe working environment for all woodworking employees.
Implementing a Safety Training Program for Woodworking Employees
Woodworking businesses must prioritize the safety of their employees by implementing a comprehensive safety training program. This program should cover a wide range of topics related to safety in a woodworking environment, including proper tool usage, handling of materials, emergency procedures, and more. By providing thorough training, employers can ensure that their employees are equipped with the knowledge and skills necessary to work safely and prevent accidents.
One key aspect of a safety training program for woodworking employees is the emphasis on the proper handling of tools and machinery. Employees should be educated on how to use various woodworking tools safely and effectively, as well as how to recognize potential hazards associated with each tool. Training should also include guidelines for maintaining and inspecting machinery to reduce the risk of accidents due to equipment malfunctions.
In addition to tool usage, woodworking employees should receive training on material handling and disposal best practices. This includes instruction on how to properly lift heavy materials to prevent back injuries, as well as how to handle and dispose of hazardous waste materials in accordance with safety regulations. By educating employees on these important practices, employers can minimize the risk of workplace injuries and create a safer working environment overall.
Conclusion
In conclusion, it is crucial for all woodworking environments to prioritize safety in order to prevent accidents and protect the well-being of employees. The potential safety hazards in a woodworking environment are numerous, from flying wood particles to dangerous machinery, making it essential for employers and workers alike to be vigilant and proactive in implementing safety measures.
By recognizing the common safety hazards and understanding the proper use of personal protective equipment (PPE), woodworking professionals can significantly reduce the risk of injury or illness.
Furthermore, maintaining and inspecting woodworking machinery is paramount to ensuring a safe working environment. Regular inspections can help identify and address any potential hazards before they escalate into more significant issues.
In addition, proper handling and disposal of woodworking materials and waste are also crucial in preventing environmental contamination and reducing health risks for workers. Emergency preparedness, including having a response plan in place for various scenarios, as well as ensuring proper ventilation and air quality are other essential aspects of maintaining safety in a woodworking environment.
Lastly, implementing a comprehensive safety training program for all employees is imperative. This includes providing regular training sessions on identifying hazards, utilizing PPE effectively, safe operation of machinery, and emergency response procedures.
By fostering a culture of safety awareness and emphasizing its significance in every aspect of the woodworking process, businesses can create a work environment that prioritizes the well-being of their employees while promoting productivity and efficiency. It is only through this collective effort that the potential safety hazards present in a woodworking environmental can be effectively managed.
Frequently Asked Questions
What Are Some of the Dangers Present in a Woodworking Environment?
In a woodworking environment, some of the dangers present include the risk of cuts and puncture wounds from sharp tools and machinery, such as saws and chisels. Additionally, there is a potential for eye injuries from flying wood chips or debris, as well as the risk of inhaling harmful dust particles generated during the woodworking process.
Splinters and repetitive strain injuries are also common hazards in this type of environment.
What Are the Safety Rules in the Woodworking Shop?
Safety rules in the woodworking shop include wearing appropriate personal protective equipment (PPE) such as safety goggles, gloves, and hearing protection. Following proper operating procedures for machinery and tools is crucial to prevent accidents.
Maintaining a clean and organized workspace helps minimize tripping hazards and potential accidents. It’s also important to receive proper training on all equipment and tools before use.
What Are the Potential Hazards Associated With Producing Woodworking Joints?
The potential hazards associated with producing woodworking joints include the risk of finger or hand injuries from using hand-held power tools like routers or jigsaws. There is also a danger of kickback when using saws or other cutting tools to create joints, which can lead to serious injury if not handled properly.
Additionally, exposure to toxic fumes from certain types of wood glue or finishes used in joinery poses a health hazard if not used in a well-ventilated area. Proper technique, safety measures, and PPE are all essential when working with woodworking joints to prevent accidents and injuries.
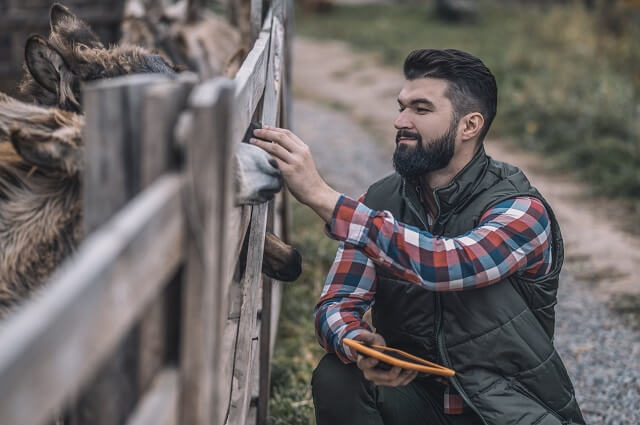
Hi everyone! I’m a woodworker and blogger, and this is my woodworking blog. In my blog, I share tips and tricks for woodworkers of all skill levels, as well as project ideas that you can try yourself.