When it comes to establishing and operating a woodworking shop, understanding the occupancy requirements is crucial for ensuring the safety and legal compliance of the business. The specific occupancy classification for a woodworking shop can have a significant impact on everything from building codes and regulations to zoning and permitting.
It also plays a crucial role in determining the safety measures, equipment, and maximum occupant load necessary for maintaining a safe working environment. In this article, we will explore the various aspects of occupancy requirements for woodworking shops, including building codes, safety considerations, fire protection and prevention, and real-life case studies.
Woodworking shops come in various types, from small hobbyist shops to large-scale industrial operations. Each type may have different occupancy requirements based on their size, layout, equipment, and intended use. Understanding these differences is essential for ensuring that the woodworking shop complies with all relevant regulations. Certain zoning requirements may also come into play when establishing a woodworking shop in different areas, along with the necessary permits to ensure compliance with occupancy regulations.
In addition to meeting legal requirements, ensuring a safe working environment should be a top priority for any woodworking shop. This involves implementing appropriate safety measures such as dust collection systems, fire suppression equipment, personal protective gear, and calculating the maximum occupant load based on the size and layout of the shop. By delving into these important considerations surrounding occupancy requirements, woodworking shop owners can better navigate the process of establishing their businesses while prioritizing safety and legal compliance.
Types of Woodworking Shops
Woodworking shops come in a variety of sizes and scales, each with its unique set of occupancy requirements. From small hobbyist workshops to large-scale industrial operations, the type of woodworking shop can significantly impact the regulations and safety considerations it must adhere to. Hobbyist shops, typically run by individuals for personal projects and small-scale production, may have less stringent occupancy requirements compared to larger industrial woodworking facilities.
In a smaller woodworking shop or hobbyist workshop, the occupancy load is likely to be lower due to the limited number of workers and visitors present at any given time. This type of shop might also operate within a residential area, which could further affect zoning and permitting requirements.
On the other hand, large-scale industrial woodworking operations often require strict adherence to building codes and regulations, including extensive fire protection systems, ventilation requirements, and specific layout guidelines to ensure safe occupancy levels for a greater number of employees and machinery.
Understanding the distinctions between these different types of woodworking shops is crucial for business owners as they navigate through the process of establishing their workshop and ensuring compliance with applicable occupancy requirements. By carefully evaluating these factors from the outset, woodworking shop owners can proactively address safety concerns and legal obligations while creating a conducive environment for their craftsmanship.
Type of Woodworking Shop | Occupancy Requirements |
---|---|
Hobbyist Workshop | Likely to have lower occupancy load due to limited number of workers/visitors |
Large-Scale Industrial Operation | Require strict adherence to building codes & regulations for higher number of employees/machinery |
Building Codes and Regulations
Fire Safety Requirements
Woodworking shops are often at a higher risk of fire due to the presence of flammable materials such as wood dust, solvents, and finishing products. As a result, there are specific fire safety requirements that must be met to ensure the safety of occupants and the surrounding area. These may include the installation of fire-rated materials, sprinkler systems, and proper storage of flammable materials.
Ventilation Standards
Proper ventilation is crucial in woodworking shops to remove potentially harmful dust and fumes from the air. The Occupational Safety and Health Administration (OSHA) sets regulations for indoor air quality in woodworking facilities, including the use of effective dust collection systems and exhaust ventilation to minimize airborne particulates that can pose health hazards.
Electrical Requirements
Woodworking equipment often requires significant electrical power, so it’s essential for woodworking shop owners to comply with electrical codes to prevent hazards such as overloading circuits or inadequate grounding. Ensuring that all electrical installations meet National Electrical Code (NEC) standards will help guarantee a safe working environment.
Understanding these specific building codes and regulations is essential for any woodworking shop owner to operate legally and maintain a safe workspace. By adhering to these requirements, woodworking shops can protect their employees, customers, and business reputation while avoiding potential legal issues related to non-compliance.
Zoning and Permitting
When establishing a woodworking shop, it is crucial to understand the zoning requirements in different areas and obtain the necessary permits to ensure compliance with occupancy regulations. The specific zoning regulations for woodworking shops can vary depending on the location, and it is essential to research and understand these requirements before establishing or relocating a woodworking business. Here are some key considerations when it comes to zoning and permitting for woodworking shops:
- Research: Before starting a woodworking shop, it is important to research the zoning regulations in the desired location. Some areas may have specific industrial zones where woodworking activities are permitted, while others may have more stringent restrictions.
- Zoning Compliance: Once a suitable location has been identified, it is necessary to ensure that the intended use of the property complies with local zoning ordinances. This may involve obtaining a zoning permit or special exception if the property is not currently zoned for industrial activities.
- Permitting Process: In addition to zoning requirements, woodworking shops may be subject to specific permitting processes to ensure compliance with occupancy regulations. This could include obtaining building permits for construction or renovation work, as well as obtaining additional permits for equipment installation, electrical work, and fire safety systems.
Navigating the zoning and permitting process for a woodworking shop can be complex, but it is essential for ensuring legal compliance and safety for both employees and customers. By understanding and adhering to these occupancy requirements, woodworking businesses can operate with confidence while avoiding potential legal issues or safety hazards.
It’s important to note that failure to comply with zoning requirements or obtain necessary permits can result in fines or even shutdowns of the business. Therefore, it is recommended to work closely with local authorities and professionals familiar with zoning and permitting processes to ensure that all requirements are met before establishing or making significant changes to a woodworking shop’s operations.
Safety Considerations
When it comes to operating a woodworking shop, safety should be a top priority. Implementing the right safety measures and equipment is essential to maintaining a safe working environment for both employees and customers. Below are some key safety considerations that woodworking shop owners should keep in mind:
- Dust Collection Systems: Woodworking generates a significant amount of dust, which can pose serious health hazards and fire risks if not properly managed. Installing an effective dust collection system is crucial for maintaining air quality and preventing combustible dust buildup.
- Fire Suppression: Woodworking shops are at risk of fire due to the use of flammable materials and equipment. Implementing fire suppression systems, such as sprinklers and fire extinguishers, can help prevent fires from spreading and minimize damage in the event of an emergency.
- Personal Protective Equipment (PPE): Providing employees with the necessary PPE, such as goggles, respirators, ear protection, and gloves, is essential for safeguarding against potential injuries or exposure to hazardous materials.
In addition to these specific safety measures, woodworking shops should also prioritize general safety practices, such as regular equipment maintenance, proper tool usage training, and emergency evacuation procedures. By proactively addressing safety concerns, woodworking shop owners can create a secure and compliant work environment.
Remember when setting up your woodworking space that redirecting focus on what occupancy would be a woodworking shop can help you better understand how much space you need or what permits you may need to operate safely and legally. It’s vital to adhere to building codes and regulations related to occupational requirements in order to ensure the overall safety of your establishment.
Occupant Load Calculations
Woodworking shops must adhere to specific occupancy requirements to ensure the safety of occupants and legal compliance. One critical aspect of these requirements is determining the maximum number of occupants allowed in a woodworking shop, also known as occupant load. Understanding and calculating the occupant load is essential for maintaining a safe working environment and avoiding potential legal complications.
The process of calculating the occupant load for a woodworking shop involves considering various factors such as the size of the space, its layout, and the equipment present. The size of the woodworking shop will dictate how many individuals can safely occupy the space at any given time. Additionally, factors such as aisles, exits, and clearances must be taken into account when determining the maximum occupant load.
The layout of the woodworking shop also plays a crucial role in determining occupant load. Workstations, machinery placement, and circulation paths all impact how many individuals can safely work within the space. Furthermore, specific equipment used in woodworking shops may require additional safety measures or affect the overall occupant load. For example, if heavy machinery or hazardous materials are present, this could limit the number of occupants allowed in the shop at one time.
Adhering to safety codes while accurately calculating occupant load ensures a safe and compliant working environment for all employees and visitors. This process is an integral part of running a successful woodworking shop while meeting legal obligations.
Understanding how to calculate occupant load is essential to comply with regulations while prioritizing safety within a woodworking shop setting. By carefully considering factors such as size, layout, and equipment, woodworkers can ensure they are operating within legal guidelines while maintaining a safe environment for all occupants.
Fire Protection and Prevention
A woodworking shop presents unique challenges when it comes to fire protection and prevention. Due to the nature of their work, woodworking shops are at a heightened risk for fire hazards, making it crucial to implement specific measures to ensure the safety of occupants and the prevention of potential disasters. This section will delve into the specific fire protection and prevention measures required for woodworking shops, including the use of fire-rated materials, sprinkler systems, and emergency exits.
When considering fire protection in a woodworking shop, the use of fire-rated materials is essential. Woodworking shops are filled with flammable materials such as wood shavings, sawdust, and various types of lumber. Therefore, it is imperative that any construction or renovation within the space meets strict fire resistance standards to minimize the risk of combustion or rapid spread of fire.
In addition to utilizing fire-rated building materials, installing a sprinkler system can greatly enhance fire protection in a woodworking shop. A well-designed sprinkler system can effectively suppress a potential fire outbreak before it spirals out of control. To ensure proper functionality and coverage, it’s important to comply with regulations regarding sprinkler placement and maintenance.
Lastly, having clearly marked emergency exits and ensuring unobstructed pathways is vital for allowing occupants to safely evacuate in the event of a fire. Conducting regular drills and providing appropriate training on evacuation procedures can further enhance safety measures within the woodworking shop.
Fire Protection Measures | Requirements |
---|---|
Fire-Rated Materials | Utilization to minimize risk of combustion or rapid spread of fire. |
Sprinkler Systems | Installation to effectively suppress potential fires. |
Emergency Exits | Importance for safe evacuation in case of a fire. |
Case Studies
When it comes to understanding the occupancy requirements for a woodworking shop, real-life examples can provide valuable insights into how different types of woodworking shops navigate compliance with regulations. For example, a small-scale hobbyist woodworking shop operating out of a home garage may have different occupancy requirements compared to a large industrial woodworking facility.
By examining these case studies, business owners and operators can gain a better understanding of what occupancy would be required for their specific woodworking operations.
One case study involves a small custom furniture woodworking shop located in a mixed-use commercial building. The shop owner had to navigate zoning requirements, building codes, and permits to ensure compliance with occupancy regulations. Through careful consideration of fire safety measures, ventilation systems, and occupant load calculations, the shop was able to meet the necessary requirements for its occupancy while creating a safe working environment for employees and visitors.
In another case study, a medium-sized woodworking shop specializing in cabinetry production had to address specific fire protection and prevention measures as part of its occupancy requirements. This included the installation of fire-rated materials, sprinkler systems, and emergency exits to meet the regulations outlined in building codes. By implementing these measures effectively, the woodworking shop was able to ensure compliance with occupancy requirements while maintaining a focus on safety for all occupants.
By examining these real-life examples of woodworking shops successfully navigating the process of determining their occupancy requirements and ensuring compliance with regulations, other woodworkers can gain valuable insights into what is needed for their specific operations. Understanding the nuances of building codes, zoning regulations, fire safety measures, occupant load calculations is essential for any woodworking shop looking to establish or expand its operations while prioritizing safety and legal compliance.
Conclusion
In conclusion, the occupancy requirements for a woodworking shop are an essential aspect of establishing and maintaining a safe and legally compliant business. As discussed in this article, understanding the specific building codes, zoning regulations, and safety considerations is crucial for woodworking shop owners to ensure the protection of their employees, customers, and property. By adhering to these occupancy requirements, woodworking shops can mitigate potential risks and liabilities while creating a secure and productive working environment.
It is important to recognize that the occupancy requirements for a woodworking shop may vary depending on the type of operation, size of the space, and equipment used. Whether it is a small hobbyist workshop or a large-scale industrial facility, woodworking shop owners must carefully assess their specific needs and responsibilities to ensure full compliance with regulations. By doing so, they can avoid potential fines or closures due to non-compliance with occupancy requirements.
Overall, this article has highlighted the key factors that woodworking shop owners should consider when determining their occupancy requirements. From fire protection measures to zoning regulations and safety considerations, each aspect plays a vital role in the successful operation of a woodworking shop. By prioritizing compliance with these requirements, woodworking shop owners can create a safe and thriving business while contributing to the overall security of their community.
Frequently Asked Questions
What Are Woodworking Shops Called?
Woodworking shops are often called “woodshops” or “woodworking studios.” These spaces are dedicated to woodworking activities such as crafting furniture, cabinetry, and other wooden items using a variety of tools and equipment.
How Big Is a Woodworking Workshop?
The size of a woodworking workshop can vary greatly depending on the available space and the individual’s needs. Some woodworkers may have small, compact workshops in a garage or basement, while others may have larger standalone buildings dedicated solely to woodworking.
Ultimately, the size of a woodworking workshop depends on the scale of projects being undertaken and the amount of equipment needed.
What Do I Need for a Home Woodworking Shop?
A home woodworking shop typically requires several essential tools and equipment such as a table saw, miter saw, jointer, planer, and various hand tools like chisels, hand saws, and clamps. Additionally, it’s important to have a sturdy workbench with adequate lighting and ventilation.
Depending on the type of projects being pursued, woodworkers may also need finishing supplies such as sandpaper, stains, paints, and varnishes to complete their creations. Good organization through storage solutions is also key to maintaining an efficient home woodworking shop.
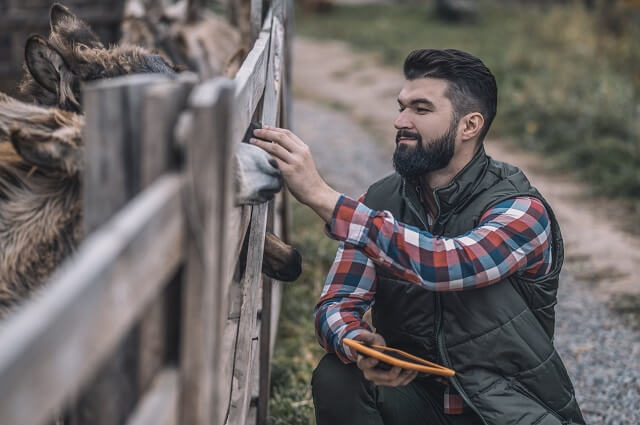
Hi everyone! I’m a woodworker and blogger, and this is my woodworking blog. In my blog, I share tips and tricks for woodworkers of all skill levels, as well as project ideas that you can try yourself.