What type of business is woodworking for OSHA? Woodworking businesses fall under the jurisdiction of the Occupational Safety and Health Administration (OSHA), which sets and enforces safety regulations to ensure the well-being of employees in the workplace. It is crucial for woodworking businesses, regardless of their scale of operation, to understand OSHA’s standards and comply with its regulations to maintain a safe working environment.
Woodworking businesses come in various scales, including small-scale, medium-scale, and large-scale operations. Each classification has its own set of challenges when it comes to complying with OSHA standards. Small-scale businesses may struggle with limited resources for safety protocols, while large-scale operations must navigate the complexities of managing a larger workforce and more extensive equipment.
In this article, we will explore the different aspects of OSHA regulations for woodworking businesses, from safety protocols and equipment regulations to employee training and compliance checks. Understanding these regulations is essential for woodworking businesses to prioritize employee safety and avoid potential risks that could result in accidents or injuries.
Classification of Woodworking Businesses
Woodworking businesses can vary widely in terms of scale, from small-scale operations run by individual craftsmen to large-scale manufacturing facilities. Each type of woodworking business comes with its own unique set of challenges when it comes to complying with OSHA regulations.
Small-scale woodworking businesses typically operate out of small workshops or home-based settings, often with just a few employees or even as sole proprietorships. These businesses may not have the same resources as larger operations, making OSHA compliance more challenging. However, it is still crucial for these businesses to adhere to safety standards to protect their workers and avoid potential fines or penalties.
Medium-scale woodworking businesses may have more employees and operate out of dedicated commercial spaces. These businesses may use a variety of equipment and machinery in their operations, increasing the complexity of OSHA compliance requirements. It is essential for medium-scale woodworking businesses to develop comprehensive safety protocols and provide thorough employee training to ensure compliance with OSHA standards.
Large-scale woodworking operations encompass manufacturing facilities that produce a high volume of wood products. These businesses often use advanced machinery and technology, leading to increased safety risks for workers. OSHA regulations for large-scale woodworking businesses are extensive and require meticulous attention to detail in order to maintain compliance.
Woodworking Business Scale | Key Considerations for OSHA Compliance |
---|---|
Small-Scale | Limited resources may present challenges in meeting OSHA standards; comprehensive safety measures essential. |
Medium-Scale | Increased complexity due to equipment and machinery usage; thorough employee training necessary. |
Large-Scale | Extensive regulations due to high volume production and advanced technology; meticulous attention required for compliance. |
OSHA Standards for Woodworking
Woodworking businesses are subject to specific safety protocols and regulations set forth by the Occupational Safety and Health Administration (OSHA). These regulations are designed to ensure the safety of employees working with wood and using equipment and machinery in woodworking operations. OSHA standards for woodworking cover a wide range of safety measures, including guidelines for equipment maintenance, proper use of tools, and protective measures for employees.
One of the key aspects of OSHA standards for woodworking businesses is the requirement for employers to provide a safe working environment, including properly maintained equipment and machinery. This includes regular inspections of tools and machines to identify any potential hazards or malfunctions that could pose a risk to workers. Additionally, OSHA mandates that woodworking equipment be equipped with necessary safeguards to prevent accidents and injuries.
In addition to equipment regulations, OSHA standards for woodworking also outline specific safety protocols for using various types of machinery commonly found in woodworking businesses. Employers are required to provide thorough training on the safe operation of tools such as saws, drills, sanders, and lathes.
This training ensures that employees understand how to use these machines safely and are aware of potential hazards associated with their operation. Overall, OSHA’s focus on safety protocols and regulations for woodworking equipment and machinery aims to protect employees from workplace accidents and injuries.
Employee Training and Education
Woodworking businesses, regardless of their size and scale of operations, are required to comply with OSHA regulations to ensure the safety and well-being of their employees. OSHA, or the Occupational Safety and Health Administration, has specific standards in place for woodworking businesses to follow in order to create a safe working environment. Employee training and education play a crucial role in ensuring OSHA compliance within woodworking businesses.
The importance of OSHA compliance in employee training and education cannot be overstated. By providing comprehensive training programs, woodworking businesses can ensure that their employees are aware of potential hazards and know how to handle machinery and equipment safely. This not only reduces the risk of workplace accidents but also contributes to overall productivity and efficiency.
To achieve OSHA compliance in employee training and education, woodworking businesses should consider implementing the following measures:
- Conducting regular safety training sessions for all employees
- Providing detailed instruction manuals for each piece of machinery
- Offering refresher courses on safety protocols and procedures
- Encouraging open communication between management and employees regarding safety concerns
Overall, OSHA compliance in employee training and education is essential for creating a safe and secure working environment within woodworking businesses. By prioritizing employee safety through proper training and education, woodworking businesses can minimize workplace accidents and ensure that they are meeting OSHA regulations.
Personal Protective Equipment (PPE) Requirements
Woodworking environments can pose various hazards to employees, making the use of Personal Protective Equipment (PPE) crucial for ensuring their safety. OSHA has established specific requirements for PPE in woodworking businesses to protect workers from potential injuries and health risks. It is important for all types of woodworking businesses, whether small-scale, medium-scale, or large-scale operations, to adhere to these regulations to create a safe work environment.
Types of PPE Required by OSHA
OSHA regulations mandate the use of certain types of PPE in woodworking environments. This includes but is not limited to, eye and face protection such as safety glasses or goggles to prevent eye injuries from flying debris, dust masks or respirators to protect against inhaling wood dust and other airborne particles, hearing protection such as earplugs or earmuffs to guard against noise exposure from machinery, and gloves to prevent cuts and puncture wounds while handling wood materials.
Employer Responsibilities Regarding PPE
It is the responsibility of employers in woodworking businesses to provide the necessary PPE required by OSHA regulations at no cost to employees. Employers must also ensure that PPE is properly maintained, replaced when necessary, and that employees are trained on how to use the equipment correctly. Additionally, employers are responsible for enforcing the usage of PPE in the workplace and conducting regular assessments of its effectiveness.
Employee Compliance With PPE Requirements
Employees have a duty to comply with the use of assigned PPE when working in woodworking environments. They should wear all required protective gear as directed by their employer during tasks that pose potential risks. Employees should also properly maintain their personal protective equipment and promptly report any concerns about its fit, function, or condition to their supervisors. By adhering to OSHA’s PPE requirements, both employers and employees can contribute to creating a safer work environment in woodworking businesses.
Hazard Communication and Material Safety Data Sheets (MSDS) in Woodworking Businesses
In woodworking businesses, it is crucial to prioritize hazard communication and the use of Material Safety Data Sheets (MSDS) as part of Occupational Safety and Health Administration (OSHA) compliance. OSHA requires woodworking businesses to have a comprehensive hazard communication program in place to ensure that employees are aware of the potential risks associated with their work environment. This includes properly labeling hazardous materials and providing safety data sheets for employees to reference.
Woodworking businesses must maintain SDS for all hazardous chemicals used in their operations. These sheets contain essential information about the properties of each chemical, potential health effects, safe handling procedures, and emergency measures. Employees should have access to these sheets at all times and be trained on how to interpret the information provided. It is also important for woodworking businesses to regularly review and update SDS as necessary, ensuring that all information remains accurate and current.
Proper communication of hazards and easy access to MSDS can significantly reduce the risk of accidents and injuries in woodworking businesses. By equipping employees with the knowledge they need to identify and handle hazardous materials safely, businesses can maintain a compliant and secure work environment under OSHA regulations.
Hazard Communication Program | Material Safety Data Sheets |
---|---|
Properly label hazardous materials | Contains essential information about chemical properties |
Employee training on potential risks | Includes safe handling procedures |
Regular review and updating of MSDS | Accessible to employees at all times |
Record-Keeping and Reporting
Woodworking businesses are required to maintain comprehensive records and reports of all incidents, accidents, and near misses as per OSHA requirements. Proper record-keeping is essential for not only complying with OSHA regulations but also for creating a safe work environment for employees. Here are some key points to consider when it comes to record-keeping and reporting for woodworking businesses:
- Incident Documentation: Woodworking businesses must document any workplace incident, injury, or illness that occurs on the premises. This includes detailed information about the nature of the incident, the individuals involved, and any contributing factors. Keeping accurate records of incidents helps identify trends and areas for improvement in safety protocols.
- Reporting Requirements: In addition to documenting incidents, woodworking businesses are obligated to report certain types of incidents to OSHA. This typically includes serious injuries, fatalities, or situations that pose an imminent danger to employees. Understanding what needs to be reported and how to do so in a timely manner is crucial for OSHA compliance.
- Retention Period: OSHA mandates that incident records be retained for a specific period of time. For example, some records must be kept for five years while others may need to be kept indefinitely. It is important for woodworking businesses to understand these retention requirements and ensure that their records are maintained accordingly.
In summary, record-keeping and reporting play a vital role in ensuring OSHA compliance within woodworking businesses. By maintaining accurate documentation of incidents and promptly reporting when necessary, woodworking businesses can create a safer work environment for their employees while also meeting regulatory requirements set by OSHA.
Inspections and Compliance Checks
OSHA, the Occupational Safety and Health Administration, plays a crucial role in ensuring the safety and well-being of employees in woodworking businesses. OSHA monitors these businesses through a series of inspections and compliance checks to ensure that they are following safety regulations and protocols.
During inspections, OSHA officials will assess the woodworking environment to identify any potential hazards or violations of safety standards. This includes examining equipment and machinery, checking for proper employee training and education, and assessing the implementation of personal protective equipment (PPE) requirements. OSHA also looks into whether woodworking businesses are complying with hazard communication and material safety data sheets (MSDS) requirements.
Compliance checks are another way that OSHA monitors woodworking businesses to ensure safety. These checks may be conducted periodically or in response to specific complaints or concerns. During these checks, OSHA officials will review records related to incident documentation and reporting, as well as other pertinent information to verify that the business is adhering to OSHA regulations.
Overall, OSHA’s inspections and compliance checks are essential for maintaining a safe work environment within woodworking businesses. By monitoring these businesses closely, OSHA can help prevent workplace accidents, injuries, and illnesses, ultimately ensuring the well-being of employees within the industry. This demonstrates just how important it is for woodworking businesses to adhere to OSHA regulations and prioritize workplace safety.
Conclusion
In conclusion, OSHA compliance is crucial for all types of woodworking businesses, regardless of their scale of operations. Small-scale, medium-scale, and large-scale woodworking businesses must adhere to OSHA standards to ensure the safety and well-being of their employees.
By implementing safety protocols and regulations for equipment and machinery, providing adequate employee training and education, ensuring the use of personal protective equipment (PPE), and effectively communicating hazards through material safety data sheets (MSDS), woodworking businesses can create a safe working environment in line with OSHA requirements.
It is important for woodworking businesses to prioritize OSHA compliance in order to prevent workplace injuries and illnesses. By maintaining thorough record-keeping and reporting procedures, including incident documentation and reporting, woodworking businesses can demonstrate their commitment to upholding OSHA standards. Additionally, undergoing regular inspections and compliance checks from OSHA helps woodworking businesses identify and address any potential safety hazards in their operations.
In essence, OSHA compliance is not just a legal requirement but also a moral obligation for woodworking businesses. Prioritizing the safety of employees through adherence to OSHA standards ultimately contributes to the overall success and sustainability of woodworking operations. It ensures that employees are able to work in a safe environment while also fostering a positive company culture focused on employee well-being.
What type of business is woodworking for OSHA? It is a business that must prioritize safety and compliance at every level of its operations in order to protect its most valuable asset – its employees.
Frequently Asked Questions
What Type of Business Is OSHA?
OSHA, which stands for the Occupational Safety and Health Administration, is a regulatory agency of the United States Department of Labor. Its primary function is to ensure safe and healthy working conditions for employees.
What Category Does OSHA Fall Under?
OSHA falls under the category of government agencies responsible for regulating and enforcing workplace safety standards. It specifically operates within the realm of labor and employment laws, focusing on safeguarding workers from hazards and dangers in the workplace.
What Is Considered a Small Business for OSHA?
For OSHA, a small business is generally defined as one with fewer than 250 employees. However, OSHA offers exemptions and partial exemptions for certain industries based on their size, including those with 10 or fewer employees. Each size classification may have unique compliance requirements based on the industry’s specific risk factors associated with occupational safety and health.
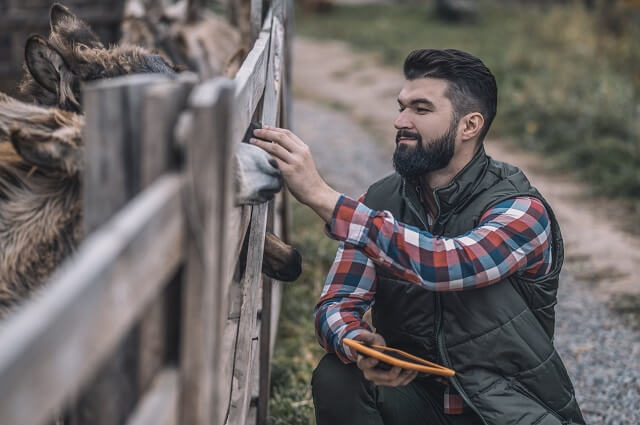
Hi everyone! I’m a woodworker and blogger, and this is my woodworking blog. In my blog, I share tips and tricks for woodworkers of all skill levels, as well as project ideas that you can try yourself.