Introduction to Traditional Japanese Woodworking Bench
The traditional Japanese woodworking bench is a unique piece of furniture that dates back centuries. Concieved in the Edo period (1603 – 1868) the Japanese woodworking bench has remained relatively unchanged for over 400 years. Crafted from solid cherry, walnut and maple woods, these benches were designed to provide fine finishes and precise accuracy when cutting or carving into the wood. The construction techniques and principles used were passed on from generation to generation, contributing to its long-standing history as one of the world’s most beloved pieces of furniture.
This robust craftsmanship is evident in its sturdy build and ornate appearance, often featuring intricate diamond designs that craftspeople lovingly carve into the wood, creating a unique visual aesthetic that is both captivating and functional. Typically constructed with dovetailing joints at each corner and circled twice around pegs known as ‘marugo,’ these benches are made to last through even the most vigorous use.
Not only can this type of furniture be used for woodworking purposes, it also serves as a decorative item in any home or workspace due to its intricate carvings and unique design elements. It is revered as much today as it was hundreds of years ago and continues to captivate artisans across Asia and beyond with its elegant beauty and timeless form. Through its development over generations, the traditional Japanese Woodworking Bench offers an incomparable display of artisanal skill and ingenuity which is integral to any practitioner of fine craftsmanship
Historical Context
Japanese woodworking is an ancient craft that has existed since at least the 8th century and has seen many regional variations throughout its long history. As the country became more industrialized, traditional tools and techniques fell out of use and were replaced by newer methods. In the early 1900s, several craftsmen around Japan developed their own style of woodworking bench called the Watoku-Jyukusei-Danko in an effort to improve traditional woodworking techniques. This style of bench consisted of a large block of wood cut into four rectangles with a variety of angles, creating an ideal area for clamping and attaching objects.
The development of the modern Japanese woodworking bench was influenced by the industrialization process which led to the adoption of efficient production methods and advanced machinery which further improved traditional techniques. The traditional design was kept but it was combined with new materials such as steel or aluminium to create lighter but still reliable structures, capable to withstand heavy workloads. Additionally, different features like adjustable benches or additional storage compartments were introduced.
Today, while there are still some master craftsmen that practice Japanese woodworking with traditional tools and techniques, most people interested in learning this craft are likely to use modern Japanese benches due to their versatility and reliability. Furthermore, they can also be found in a variety of sizes depending on their purpose which gives them even more flexibility to suit any type of project or workspace.
Made With Intricate Detail
A traditional Japanese woodworking bench is crafted from high-quality hardwood with intricate attention to detail. These pieces often feature unique joinery techniques such as where the frame and legs meet, adding strength and allowing for precise alignments throughout the piece. The joints are then reinforced using dovetails or Japanese-style joinery called “tebiki,” which uses wooden pegs to keep them secure.
The surface of the bench is also decorated with elaborate inlays of different types of woods, such as hinoki cypress, ebony, rosewood, and sometimes bamboo. Each shape and pattern is designed particularly to enhance the beauty of its particular type of wood.
The careful attention to detail doesn’t end there either: traditional Japanese woodworking benches may include a variety of fluting on their legs, shaped aprons surrounding the table top and even more ornate designs carved into their surfaces that represent stories or create scenes depicting plants, birds or animals generously filling the piece with personality. As a result of all these details, no two benches are exactly alike; each one only adds to the beauty of its style while also exhibiting history and knowledge by providing information about its maker’s expertise in developing such works of art from their craftsmanship.
Materials Used
Traditional Japanese woodworking benches are generally crafted from local hardwoods, including hinoki cypress and cedar. These woods are durable and well-suited for workbenches due to their natural resistance to wear and tear. As well as these commonly used hardwoods, bamboo can also be used for a more affordable yet sturdy bench.
In addition to the materials used, traditional Japanese woodworkers seek out timber that is sustainably sourced. This means selecting trees that are harvested without causing damage to the surrounding environment and causing minimal impact on ecosystems or habitats.
All of these materials require careful preparation before they can be effectively used in woodworking benches. The type of wood chosen will affect the processes that need to take place such as planing, sanding, jointing and mortising. Additionally, any additional strengthening necessary to support heavier weights must also be considered when crafting with softer woods like bamboo.
Creating a traditional Japanese bench requires great skill and precision in order for it to last for years and remain structurally sound during usage. With thoughtful selection of materials, respect for the environment and adherence to appropriate craftsmanship techniques, this style of bench is set up to offer strength and longevity even under significant use over time.
Finishing Touches
The finishing touches applied to Japanese woodworking benched are a reflection of the incredible craftsmanship and attention to detail of the skilled artisans who handcraft them. Each piece is lovingly worked on by highly trained experts who carefully sand, polish, lacquer, and carve each detail with extreme accuracy. After all the fine details have been completed and perfected, the top layer is heavily lacquered – a process that involves several layers of different resins being applied and left to dry until perfectly smooth.
The final stage involves beautifully intricate carvings that often take weeks or even months to finish. This painstaking effort adds depth, texture, and character to the furniture pieces, while also serving a functional purpose as some traditional designs feature inset drawers and shelves which were carved into the frame. After taking all these steps, the finished product is truly something special – an heirloom for generations that highlights true skill in woodworking artistry.
Where To Purchase A Traditional Japanese Woodworking Bench
When purchasing a traditional Japanese woodworking bench, it is important to ensure that the product you are buying is truly genuine. Unless purchased from a reputable source, there is no guarantee of the authenticity of such pieces.
One way to evaluate a potential purchase is to look for known makers from Japan’s skilled woodworking families, such as Tsukahara and Takahashi. A truly traditional and genuine bench will also have evidence of handwork, such as tool marks or intricate joinery detailing.
When researching where to purchase traditional wooden benches from Japan, try shopping online and attend auctions both internationally and domestically. Websites such as Amazon or Yahoo! Japan auctions often feature listings for luxurious pieces. Specialty websites like ‘Japan Objects’ other dedicated boutiques may be worth exploring as well, if they specialize in antique furniture or carpentry-related items.
Auctions are also an excellent source of rare and collectible benches made during the ‘good ole days’. While attending any auction in person can be helpful; many dealers also offer additional services including customer service support and international shipping options if needed.
It is best to do your research before committing to purchase. Be sure to ask questions related to authentication processes when shopping, such as if the maker has been certified by The Maker Mark Association ” this non-profit organization tries to verify craftsmen, materials used and processes involved with creating the item in question (a necessary indicator for deciding whether or not it can be regarded as true vintage). Additionally read reviews about the vendor or seller online before making a decision ” this will help you assess their selling reputation, know more about their return policies even better decide if the price being offered is competitive enough given what you wish to buy.
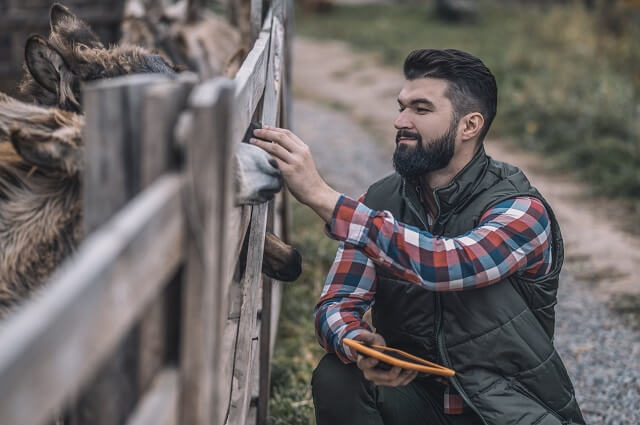
Hi everyone! I’m a woodworker and blogger, and this is my woodworking blog. In my blog, I share tips and tricks for woodworkers of all skill levels, as well as project ideas that you can try yourself.