How much torque is needed in woodworking? Understanding the role of torque in woodworking is essential for achieving precise and efficient results. Torque plays a crucial role in determining the power and efficiency of woodworking tools, making it important to have a good grasp of its significance in the craft.
In woodworking, torque refers to the amount of force required to rotate a tool or workpiece around an axis. It is a key factor in determining the effectiveness of various woodworking tasks such as drilling, cutting, shaping, and fastening. Understanding how much torque is needed for different woodworking tasks can make a significant difference in the quality of your finished projects.
Importance of torque in woodworking tools cannot be overstated. Different types of woodworking tasks have varying torque requirements, depending on factors such as the hardness and thickness of the material being worked on.
Additionally, achieving the right amount of torque is crucial for ensuring safety and preventing any potential damage to both the tools and the workpiece. In this article, we will explore the significance of understanding torque in woodworking, as well as provide recommendations for achieving the appropriate amount of torque for common woodworking tools such as drills, saws, and routers.
Importance of Torque in Woodworking Tools
Understanding the importance of torque in woodworking tools is crucial for achieving precise and efficient results in any woodworking project. Torque refers to the rotational force applied by a tool, such as a drill, saw, or router, and plays a critical role in completing various tasks like drilling holes, driving screws, cutting materials, and shaping wood.
In woodworking, the correct amount of torque is essential for not only ensuring that the tool operates effectively but also for preventing damage to the workpiece and the tool itself. For example, when using a drill to bore holes into hardwood, applying too little torque may result in the bit getting stuck or breaking, while applying too much torque can lead to burning or splintering of the wood.
Understanding how much torque is needed for different woodworking tasks is key to achieving clean and precise results.
Different types of woodworking tasks require varying amounts of torque. For instance, driving screws into hardwood typically requires more torque than drilling holes in softwood. Additionally, shaping wood with a router demands consistent and controlled torque to achieve smooth and even cuts. Therefore, it is essential to be aware of the specific torque requirements for each task when working on a woodworking project.
Proper maintenance of woodworking tools is also crucial for maintaining consistent torque output. Regularly cleaning and lubricating moving parts can help ensure that tools operate at their optimal performance levels. In addition to this, checking and calibrating torque settings as recommended by manufacturers can help prevent inconsistencies and avoid potential mistakes when applying torque in woodworking.
Different Types of Woodworking Tasks and Their Torque Requirements
Woodworking encompasses a wide range of tasks, and each task may have different torque requirements depending on factors such as the type of wood being worked, the size of the project, and the specific woodworking tool being used. Understanding the torque needed for different woodworking tasks is crucial to achieving precise and efficient results.
Drilling
When it comes to drilling in woodworking, the amount of torque needed will depend on factors such as the diameter of the hole being drilled, the density of the wood, and the type of drill bit being used. For example, larger drill bits and denser woods will require higher levels of torque to achieve a smooth and clean cut.
Cutting and Shaping
Saws and routers are commonly used for cutting and shaping wood in woodworking projects. The torque needed for these tasks will vary depending on the thickness and hardness of the wood, as well as the type of blade or router bit being utilized. For example, cutting through hardwood will require more torque compared to softwood.
Screwing and Fastening
Screwing and fastening are essential tasks in woodworking projects, whether it’s assembling furniture or constructing wooden structures. The torque required for driving screws into wood will depend on factors such as the size and material of the screws, as well as the hardness of the wood. Using too much torque can cause damage to both the screws and the wood, while using too little can result in loose or weak joints.
Understanding these various types of woodworking tasks and their corresponding torque requirements is essential for achieving optimal results in woodworking projects. By carefully considering these factors, woodworkers can ensure that they apply just the right amount of torque to accomplish their tasks effectively while preserving their tools and materials.
Recommended Torque Specifications for Common Woodworking Tools (Eg Drills, Saws, Routers)
Woodworking tools such as drills, saws, and routers are essential for various woodworking tasks. Each of these tools requires a specific amount of torque to function properly and produce high-quality results. Understanding the recommended torque specifications for these common woodworking tools is crucial for achieving precision and efficiency in woodworking projects.
Drills
When it comes to drills, the torque setting is crucial for controlling the force used to drive the screw or drill into the wood. For example, when drilling into hardwood, a higher torque setting is required compared to softer woods. It’s important to refer to the manufacturer’s guidelines for the recommended torque specifications based on the type of material being drilled.
Saws
Circular saws and table saws also require a specific amount of torque to cut through different types of wood effectively. The depth of cut and density of the wood are factors that determine how much torque is needed for sawing. It’s important to adjust the torque settings according to the thickness and hardness of the wood being cut to avoid damaging the tool or producing subpar results.
Routers
Routers are commonly used in woodworking for shaping edges, grooves, and intricate designs. The torque required for routers depends on factors such as bit size, wood density, and desired cutting speed. It’s essential to use the appropriate cutting speed and adjust the torque settings accordingly to achieve smooth and precise cuts without causing any tear-out or splintering.
Understanding the recommended torque specifications for common woodworking tools is key in achieving professional-looking results while extending the lifespan of your tools. It’s important to always refer to the manufacturer’s guidelines and make adjustments based on the specific woodworking task at hand.
Calculating Torque Needed for Specific Woodworking Projects
When working on specific woodworking projects, it is crucial to understand the amount of torque needed in order to achieve precise and efficient results. Different tasks require different levels of torque, and it is important to calculate the appropriate amount for each project. Here are some guidelines for calculating the torque needed for specific woodworking projects:
1. Determine the nature of the task: The first step in calculating the torque needed for a specific woodworking project is to determine the nature of the task. For example, drilling holes in hardwood will require more torque than drilling holes in softwood. Similarly, cutting through thick pieces of wood will require more torque than cutting through thinner pieces.
2. Consider the type of woodworking tool: Different woodworking tools have different torque requirements. For example, drills, saws, and routers all have their own recommended torque specifications. It is important to take into account the specific tool being used for the project when calculating the necessary torque.
3. Consult with torque charts: Many manufacturers provide torque charts that outline the recommended specifications for their woodworking tools. These charts can be a valuable resource when calculating the torque needed for a particular project.
By carefully considering these factors and consulting with manufacturer’s recommendations, woodworkers can accurately calculate the amount of torque needed for their specific woodworking projects.
By following these tips, woodworkers can ensure that they are applying the right amount of torque for their specific projects while achieving precise and efficient results.
Tips for Achieving the Right Amount of Torque in Woodworking
When it comes to woodworking, achieving the right amount of torque is crucial for ensuring that your projects are completed with precision and efficiency. Whether you are using drills, saws, routers, or other woodworking tools, understanding how much torque is needed for each task can help you achieve the best results. Here are some tips for achieving the right amount of torque in woodworking:
1. Choose the right tool for the job: Different woodworking tasks require different levels of torque. For example, drilling through hardwood will require more torque than drilling through softwood. Make sure to select a tool with the appropriate torque specifications for the specific task at hand.
2. Use sharp blades and bits: Dull blades and bits can increase the amount of torque needed to effectively cut through wood. Make sure to regularly sharpen or replace your blades and bits to reduce the strain on your tools and achieve smoother cuts with less effort.
3. Maintain proper tool alignment: Misaligned tools can result in an uneven application of torque, leading to inaccuracies in your woodworking projects. Always ensure that your tools are properly aligned before beginning any task to maintain consistent torque throughout the project.
4. Apply even pressure: When using hand tools such as screwdrivers or chisels, it’s important to apply even pressure to avoid over-torquing or under-torquing fasteners or wood joints. This will not only ensure that you achieve precise results but also prevent damage to your materials.
By following these tips, you can ensure that you are applying the right amount of torque for each woodworking task, resulting in high-quality and professional-looking projects every time.
Tool Maintenance and Torque Consistency
Ensuring that woodworking tools are properly maintained is crucial in maintaining torque consistency. Over time, wear and tear on tools can lead to reduced torque output, affecting the quality of the workpiece. Regular cleaning and lubrication of moving parts, as well as proper storage, can help prevent a decrease in torque output. Keeping the cutting edges sharp on blades and bits also plays a significant role in maintaining consistent torque levels.
In addition to maintenance, it is important to regularly calibrate woodworking tools to ensure that they are providing the correct amount of torque. This is especially important for power tools such as drills, saws, and routers. Incorrect torque settings can lead to overworking the tool or poor quality results in the project. Utilizing a torque wrench or a torque screwdriver for adjustments can help achieve precision in torque settings.
Another aspect of maintaining torque consistency is being mindful of the type of material being worked on and adjusting the tool’s torque accordingly. Harder woods may require higher torque levels compared to softwoods when drilling or cutting. Understanding this variance in material properties allows woodworkers to make necessary adjustments for achieving optimal results.
Maintenance Tip | Description |
---|---|
Regular Cleaning | Remove sawdust, debris, and built-up residue from the tool’s moving parts. |
Lubrication | Apply appropriate lubricants to ensure smooth movement of components within the tool. |
Sharp Cutting Edges | Frequently sharpen blades and bits to maintain efficient cutting performance and consistent torque output. |
Common Mistakes When Applying Torque in Woodworking
When it comes to woodworking, understanding the correct amount of torque needed for different tasks is crucial. However, many woodworkers make common mistakes when applying torque, which can result in inefficient or even dangerous outcomes. One common mistake is over-tightening fasteners, which can lead to stripped threads or damage to the woodworking materials.
On the other hand, under-tightening can compromise the structural integrity of the project. It is important to find the right balance and apply just enough torque for a secure and durable result.
Another mistake woodworkers often make is using the wrong tool for the job. Each woodworking task has specific torque requirements, and using an inadequate tool can lead to improper torque application. For example, using a drill with insufficient torque for a particular project may result in incomplete drilling or ineffective screwdriving. It’s essential to match the tool’s torque capabilities with the requirements of the task at hand.
Furthermore, neglecting proper maintenance of woodworking tools can lead to inconsistent torque application. Over time, wear and tear on tools can affect their torque output, leading to imprecise results. Regular maintenance and calibration of tools are necessary to ensure consistent and accurate torque application in woodworking projects.
Common Mistakes | Impact |
---|---|
Over-tightening fasteners | Stripped threads or damage to materials |
Using wrong tool for job | Incomplete drilling or ineffective screwdriving |
Neglecting tool maintenance | Inconsistent and inaccurate torque application |
Conclusion
In conclusion, the role of torque in achieving precise and efficient woodworking results cannot be overstated. Understanding the importance of torque in woodworking tools is essential for both beginners and experienced woodworkers. The right amount of torque ensures that you can make accurate cuts, drill holes cleanly, and create smooth finishes on your projects. By knowing how much torque is needed for different woodworking tasks, you can select the appropriate tools and set them to the correct specifications.
When it comes to specific woodworking tasks and their torque requirements, it’s important to consider the material being worked on, the type of cut or hole being made, and the size of the tool being used. For example, drilling a hole in hardwood will require more torque than drilling a hole in softwood.
Being aware of recommended torque specifications for common woodworking tools such as drills, saws, and routers can help you achieve the best results while minimizing the risk of damage to your tools or workpiece.
To calculate the torque needed for specific woodworking projects, you can use formulas based on factors such as material properties and cutting parameters. Additionally, following tips for achieving the right amount of torque in woodworking – such as maintaining proper tool maintenance and consistency – will contribute to successful outcomes in your projects. Overall, understanding how much torque is needed in woodworking enables woodworkers to work safely and efficiently while producing high-quality results.
Frequently Asked Questions
What Torque Setting for Screws?
The appropriate torque setting for screws depends on the size and material of the screw, as well as the material being fastened. It’s important to consult a torque chart or the manufacturer’s recommendations to ensure proper tightening without damage.
How Do You Calculate Drill Torque?
Calculating drill torque involves multiplying the force applied to the drill bit by the distance from the center of the chuck to the point where force is applied. This determines the torque required to achieve a specific drilling depth in a given material.
What Is the 20 Rule for Torque Wrenches?
The “20 rule” for torque wrenches refers to applying 20% of the wrench’s capacity for final tightening. This helps prevent over-torquing and ensures that fasteners are properly secured without causing damage or failure due to excessive force.
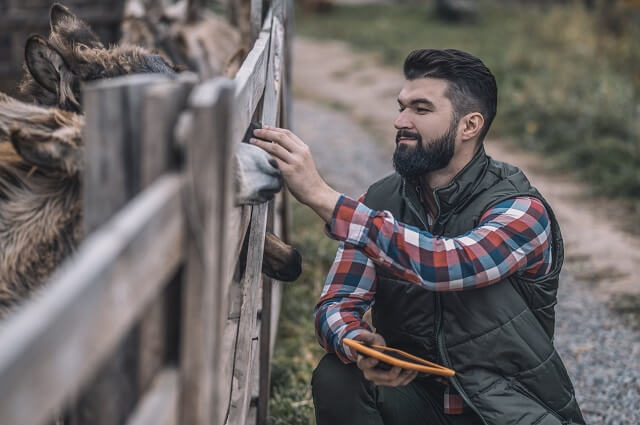
Hi everyone! I’m a woodworker and blogger, and this is my woodworking blog. In my blog, I share tips and tricks for woodworkers of all skill levels, as well as project ideas that you can try yourself.