Are you looking to add a unique and eye-catching element to your woodworking projects? Learn how to make a curved pocket woodworking and elevate your craftsmanship to the next level. Curved pockets not only add visual interest but also serve functional purposes, making them a valuable skill for any woodworker to master.
Curved pocket woodworking involves creating concave or convex pockets in wood, allowing for interesting joinery and design possibilities. Whether it’s for decorative accents, hidden storage compartments, or structural support, curved pockets can enhance the aesthetic appeal and functionality of your woodworking projects.
In this article, we will delve into the world of curved pocket woodworking, providing step-by-step guidance on how to create these unique features. From planning and design considerations to cutting, joinery, and finishing techniques, we’ve got you covered. Whether you’re a seasoned woodworker or just starting out, mastering curved pockets will open up a world of creative possibilities for your craft. So grab your tools and let’s get started.
Tools and Materials
When it comes to creating a curved pocket in woodworking, having the right tools and materials is crucial for achieving a successful result. In this section, we will discuss the specific tools and materials needed for making a curved pocket, along with some recommendations and examples to consider.
Tools
One of the key tools needed for creating a curved pocket in woodworking is a jigsaw or band saw. These versatile cutting tools are essential for cutting and shaping the curved pocket, allowing for precision and control during the process. Additionally, you will also need clamps to secure the wood in place while cutting, as well as measuring tools such as a ruler or tape measure to ensure accuracy.
Materials
The type of wood you choose for your curved pocket woodworking project is important. Different woods have varying levels of hardness and grain patterns, which can affect how they handle curves and cuts. Some recommended woods for creating curved pockets include maple, cherry, and walnut due to their strength and workability. In addition to wood, you may also need screws or other fasteners depending on how you plan to incorporate the curved pocket into your woodworking project.
Examples
For those looking for specific examples of tools and materials needed for making a curved pocket in woodworking, there are various options available on the market. Brands such as DEWALT, Bosch, and Makita offer quality jigsaws and band saws that are suitable for cutting curves in wood. When it comes to wood selection, specialty lumber stores or online retailers may offer a wider range of hardwood options for creating curved pockets.
By ensuring that you have the right tools and materials at your disposal, you can set yourself up for success when making a curved pocket in woodworking. Whether it’s investing in quality cutting tools or selecting the right type of wood for your project, these considerations will play an integral role in achieving a well-crafted and visually appealing curved pocket.
Planning and Design
- Consider wood choice: When planning a curved pocket woodworking project, it’s essential to consider the type of wood you’ll be using. Some woods are more suitable for bending and shaping, such as walnut, cherry, or maple, while others may be too brittle or prone to splitting. Be sure to choose a wood species that is suitable for the level of curvature you intend to achieve.
- Determine the size and shape: Before cutting into your selected wood, take the time to carefully plan out the size and shape of your curved pocket. Consider the overall dimensions of your project and how the curved pocket will fit into the design. Use precise measurements and consider creating a template or mockup before making any cuts.
- Test your design: Once you have drafted a plan for your curved pocket woodworking project, it’s crucial to test your design before committing to the final piece. You can create a prototype with inexpensive materials or use computer-aided design (CAD) software to visualize the end result.
By following these tips and techniques for planning and designing a curved pocket woodworking project, you can set yourself up for success in creating a unique and visually appealing element in your next woodworking endeavor.
Cutting the Curved Pocket
If you have decided to incorporate a curved pocket into your woodworking project, you will need to carefully cut and shape the wood to create the desired curve. In this section, we will provide you with step-by-step instructions on how to achieve this using various woodworking tools such as a jigsaw or band saw.
Choosing the Right Tool
When it comes to cutting a curved pocket in woodworking, choosing the right tool is crucial. A jigsaw is an excellent choice for creating gentle curves and intricate designs, while a band saw is better suited for larger, more complex curves. Take into consideration the size and intricacy of your curved pocket when selecting the appropriate tool for the job.
Setting Up the Workpiece
Before making any cuts, it’s essential to properly secure your workpiece. Use clamps or a vise to hold the wood firmly in place, ensuring stability and safety while operating the woodworking tools. Additionally, mark the outline of your curved pocket on the wood to serve as a guideline during cutting.
Cutting and Shaping
Using a jigsaw or band saw, carefully follow the marked outline of your curved pocket, making smooth and controlled cuts. Take your time and use steady hands to achieve precise shaping. If needed, make multiple passes with the woodworking tool to gradually contour the wood to match the desired curve.
By following these step-by-step instructions and utilizing the appropriate woodworking tools, you can successfully cut and shape a curved pocket for your woodworking project. With patience and attention to detail, you will be able to achieve a beautifully crafted curved pocket that enhances the overall design of your creation.
Joinery and Assembly
When incorporating a curved pocket into your woodworking project, selecting the right joinery method is crucial to ensure a strong and visually appealing finished product. There are several joinery methods that can be used to seamlessly integrate the curved pocket into your woodworking project. Here are some popular options to consider:
- Pocket Hole Joinery: This method involves creating angled holes in the wood pieces and then joining them together using screws. It is a versatile and easy way to create strong joints for cabinets, frames, and other woodworking projects.
- Mortise and Tenon Joints: This traditional joinery method involves cutting a mortise (a hole) in one piece of wood and creating a tenon (a protruding tongue) on the other piece, which fits into the mortise. It is known for its strength and durability, making it an excellent choice for joining pieces with curved pockets.
- Dowel Joinery: Using wooden dowels to join two pieces of wood together is another effective method, especially when working with curved pockets. It provides great structural support and is relatively simple to execute.
Visual Examples:
To better understand how these joinery methods can be applied to incorporate curved pockets into woodworking projects, here are some visual examples:
- Pocket Hole Joinery Example
- Mortise and Tenon Joints Example
- Dowel Joinery Example
By exploring these different joinery methods, woodworkers can choose the most suitable technique based on their specific project requirements and skills.
Remember that choosing the right joinery method will not only affect the strength and stability of your finished piece but also contribute to its overall aesthetic appeal. Considerations such as visibility of joints, wood movement, and desired finish will all play a role in determining which joinery method is best for your project incorporating a curved pocket.
Whether you’re constructing furniture or decorative pieces with curved pockets, incorporating these various joinery methods will elevate the quality of your woodworking projects while adding unique visual interest.
Sanding and Finishing
When it comes to woodworking, creating a curved pocket adds a unique and visually appealing element to your projects. Once you have successfully cut and shaped the curved pocket, the next step is to sand and finish it to achieve a smooth and polished look. In this section, we will explore various techniques for sanding and finishing curved pockets in woodworking, as well as provide recommendations for wood sealers and stains.
Before you begin the sanding process, it’s important to ensure that the curved pocket is free of any rough edges or uneven surfaces. Start by using a coarse-grit sandpaper to smooth out any imperfections and gradually work your way up to finer grits for a smoother finish. Be sure to sand both the inside and outside of the curved pocket to achieve a consistent appearance.
After sanding, applying a wood sealer can help protect the wood and enhance its natural beauty. Choose a high-quality wood sealer that is compatible with the type of wood you are working with. Additionally, applying a stain can add color and depth to the curved pocket, further enhancing its visual appeal. When selecting a stain, consider the overall design and aesthetic of your woodworking project to ensure that the color complements the rest of the piece.
Troubleshooting and Tips
Working with curved pockets in woodworking can present its own set of challenges, but with the right knowledge and techniques, these issues can be easily overcome. One common issue that woodworkers encounter when creating curved pockets is achieving a smooth and even curvature.
This can be particularly tricky when working with harder woods or intricate designs. To combat this, it is important to carefully plan and mark out the curve before cutting, ensuring that the appropriate tools are used to achieve a clean and precise cut.
Another challenge that woodworkers may face when working with curved pockets is securing the pocket in place during assembly. The curved nature of the pocket can make it difficult to attach securely without compromising its shape.
To address this issue, utilizing clamps specifically designed for irregular shapes can help to hold the pocket firmly in place while allowing for adjustments as needed. Additionally, using specialized joinery methods such as dowels or pocket hole screws can provide added structural support to ensure that the curved pocket remains secure within the project.
It is also common for woodworkers to encounter difficulties in achieving a seamless finish on curved pockets. Sanding along the curve can pose challenges, as traditional sanding blocks and methods may not conform effectively to the shape of the pocket.
To remedy this, utilizing flexible sanding materials such as foam-backed sandpaper or sanding sponges can aid in achieving a smooth finish along the curves. Additionally, applying multiple coats of wood sealer or finish can help to enhance the appearance of the curved pocket while adding an extra layer of protection against wear and tear.
Project Ideas and Inspiration
After learning about the essential tools and techniques for creating curved pockets in woodworking, it’s time to put that knowledge into practice with some inspiring project ideas. Incorporating curved pockets into your woodworking projects can add a unique and visually appealing element to your creations. Whether you’re a seasoned woodworker or just starting out, there are endless possibilities for incorporating this technique into your work.
One idea is to create a sleek and modern coffee table with curved pockets incorporated into the design. These curved pockets could serve as stylish and functional areas for storing magazines, books, or remote controls. By carefully planning the size and placement of the curved pockets, you can achieve a seamless and elegant look that complements the overall aesthetic of the table.
Additionally, consider experimenting with curved pocket shelving units to add both functionality and visual interest to your space. The use of curved pockets in the design of shelves not only adds a touch of uniqueness but also provides an opportunity for creating storage solutions that are both practical and visually appealing.
In conclusion, incorporating curved pockets into woodworking projects opens up a world of creative possibilities. With careful planning, attention to detail, and precision cutting techniques, you can bring your woodworking projects to the next level with this innovative design element. So go ahead and start brainstorming project ideas that incorporate curved pockets – the possibilities are endless.
Frequently Asked Questions
How Do You Sew a Curve Pocket?
Sewing a curve pocket requires careful pinning and stitching to ensure a smooth and even finish. Start by creating the pocket pattern, then carefully pin it to the garment, ensuring the curve lays flat as you sew.
How Do You Sew Trim on a Curve?
When sewing trim on a curve, it’s important to use a flexible or bias trim that can easily bend along the curve without puckering or pulling. Pin the trim in place, gently stretching it if necessary to match the curve as you stitch.
How to Make a Pocket Pattern?
Making a pocket pattern involves determining the size and shape of the pocket you want to create, then transferring those measurements onto paper or fabric to create a template. Be sure to add seam allowances and any necessary markings for placement on your garment.
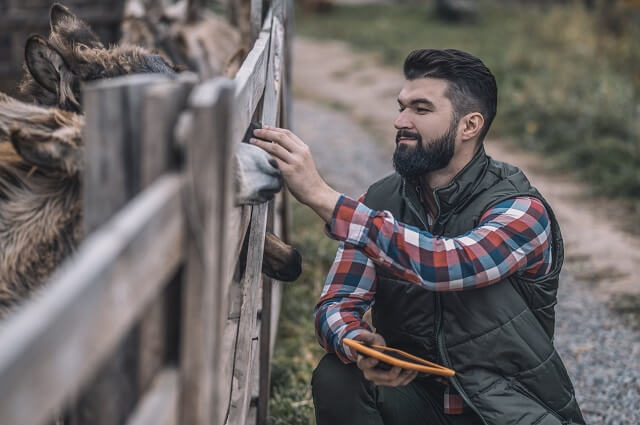
Hi everyone! I’m a woodworker and blogger, and this is my woodworking blog. In my blog, I share tips and tricks for woodworkers of all skill levels, as well as project ideas that you can try yourself.