Carbide indexable inserts play a crucial role in woodworking, offering efficient and reliable cutting performance for a variety of applications. Selecting the right carbide material for these inserts is essential to achieving optimal results. In this article, we will delve into the selection of carbide indexable insert materials for woodworking, exploring the different types of carbide materials used in indexable inserts and the factors to consider when choosing the right material for specific woodworking applications.
Woodworking professionals understand the importance of using high-quality tools and materials to achieve precision and efficiency in their work. Carbide indexable insert materials are widely used in woodworking due to their durability, wear resistance, and ability to withstand high cutting speeds. Understanding the various types of carbide materials and their performance characteristics is vital in making informed decisions when selecting the most suitable material for woodworking projects.
When it comes to choosing the right carbide material for woodworking applications, several factors need to be taken into consideration. These factors include the type of wood being worked on, cutting conditions, desired surface finish, and tool life requirements. By taking these factors into account, woodworkers can make well-informed decisions regarding the selection of carbide indexable insert materials that will deliver optimal performance and longevity.
Understanding the Different Types of Carbide Materials Used in Indexable Inserts
Carbide indexable inserts are essential tools in woodworking, offering durability and precision in cutting and shaping wood materials. However, not all carbide materials are created equal, and it’s important to understand the different types of carbide materials used in indexable inserts to make the best selection for woodworking applications.
Types of Carbide Materials
There are several main types of carbide materials used in indexable inserts for woodworking, each with its own unique characteristics and properties. The most common types include cemented carbide, cermet, and coated carbides. Cemented carbide is a popular choice due to its high hardness and wear resistance, making it suitable for a wide range of woodworking applications.
Cermet, on the other hand, offers excellent heat resistance and thermal conductivity, making it ideal for high-speed cutting operations. Coated carbides provide enhanced performance through the application of various coatings such as titanium nitride or titanium carbonitride.
Properties and Applications
Each type of carbide material has specific properties that make it well-suited for certain woodworking applications. For example, cemented carbide is often used for general-purpose cutting and shaping tasks due to its superior wear resistance. Cermet is preferred for high-speed cutting where heat buildup is a concern, while coated carbides offer improved tool life and performance in specific woodworking environments.
Considerations for Woodworking Applications
When selecting a carbide indexable insert material for woodworking, it’s crucial to consider factors such as cutting speed, feed rate, depth of cut, and the type of wood being processed. Understanding the specific requirements of the woodworking project will help in choosing the right type of carbide material that can withstand the demands of the application while delivering optimal performance.
Additionally, considering environmental factors such as humidity and temperature will further ensure the longevity and effectiveness of the chosen carbide material in woodworking operations.
Factors to Consider When Choosing the Right Carbide Material for Woodworking Applications
When it comes to selecting the right carbide indexable insert materials for woodworking applications, there are several important factors that woodworkers need to consider. The choice of carbide material can significantly impact the performance, durability, and quality of the woodworking process.
One crucial factor to consider is the type of wood being used. Some carbide materials may perform better with hardwoods, while others may be more suitable for softwoods or composite materials. Factors such as hardness, grain pattern, and resin content in the wood can all influence the selection of the appropriate carbide material.
Another important consideration is the specific cutting application. Different woodworking processes, such as roughing, finishing, shaping, and profiling, require different types of carbide materials for optimal results. For example, a woodturner may require a different carbide material compared to a furniture maker due to differences in cutting speed and tool geometry.
The machine or tool being used also plays a significant role in determining the right carbide material. Factors such as spindle speed, feed rate, and tool rigidity can influence the wear and performance of the insert material. It is essential to choose a carbide material that can withstand the specific demands of the woodworking equipment being utilized.
Factors to Consider | Considerations |
---|---|
Type of Wood | Hardness, grain pattern, resin content |
Specific Cutting Application | Roughing, finishing, shaping, profiling |
Machine/Tool Being Used | Spindle speed, feed rate, tool rigidity |
Comparing the Performance of Different Carbide Materials in Woodworking
When it comes to woodworking, the selection of carbide indexable insert materials plays a crucial role in the performance and quality of the finished product. There are several different types of carbide materials used in indexable inserts, each with its own unique properties and characteristics. Understanding how these materials compare in terms of performance can help woodworkers make informed decisions when choosing the right carbide material for their specific woodworking applications.
One of the most common types of carbide materials used in woodworking is tungsten carbide. Known for its hardness and wear resistance, tungsten carbide is often the go-to choice for a wide range of woodworking tasks, including shaping, cutting, and jointing. Another popular option is coated carbide inserts which have a protective coating that provides additional resistance to heat and wear.
In addition to tungsten and coated carbide, there are also newer materials such as cermet and cubic boron nitride (CBN) that are starting to gain popularity in the woodworking industry. These materials offer unique advantages such as improved cutting speeds and longer tool life, making them suitable for high-precision woodworking applications.
Carbide Material | Properties |
---|---|
Tungsten Carbide | Hardness and wear resistance |
Coated Carbide Inserts | Protective coating for heat and wear resistance |
Cermet and CBN | Improved cutting speeds and longer tool life |
When comparing the performance of these different carbide materials in woodworking, factors such as cutting speed, tool life, surface finish quality, and overall cost-effectiveness must be taken into consideration. By analyzing these key factors, woodworkers can determine which carbide material best suits their specific needs and project requirements. In the next section will discusses tips for selecting the best carbide indexable insert material for specific woodworking projects based on these considerations.
Tips for Selecting the Best Carbide Indexable Insert Material for Specific Woodworking Projects
Woodworking projects vary greatly in terms of the type of wood being used, the cutting conditions, and the desired end result. Therefore, it is crucial to select the right carbide indexable insert material for specific woodworking projects to ensure optimal performance and efficiency. Here are some tips for choosing the best carbide material for your woodworking applications:
Consider the Type of Wood
Different types of wood have varying hardness and grains, which can impact the performance of carbide indexable inserts. For softer woods such as pine or cedar, a general-purpose carbide material may suffice. However, for harder woods like oak or maple, a more wear-resistant carbide grade will be necessary.
Evaluate Cutting Conditions
The cutting speed, feed rate, and depth of cut are important factors to consider when selecting carbide indexable insert materials for woodworking. High-speed cutting operations may require a tougher carbide grade with improved fracture resistance, while heavy-duty cutting applications may demand a harder and more wear-resistant grade.
Assess Surface Finish Requirements
In woodworking projects where achieving a smooth surface finish is crucial, selecting a carbide material with sharp cutting edges and high edge retention is essential. Additionally, considering coatings like TiN or TiCN can further enhance surface finish quality and extend tool life in finishing applications.
By taking these tips into account and understanding the specific requirements of your woodworking project, you can make an informed decision when selecting the best carbide indexable insert material for optimal performance and results.
Case Studies of Successful Applications of Carbide Indexable Insert Materials in Woodworking
Carbide indexable inserts are widely used in woodworking for their durability, cutting performance, and cost-effectiveness.
Woodworking applications often require high precision and long tool life, making the selection of the right carbide material crucial for achieving optimal results. Here are some factors to consider when choosing the right carbide material for woodworking applications:
Factors to consider:
1. Hardness: The hardness of the carbide material will determine its wear resistance and overall tool life. Different types of wood have varying levels of density and abrasiveness, so selecting a carbide material with the appropriate hardness is essential.
2. Coating: Some carbide materials are coated with specialized materials such as titanium nitride (TiN) or titanium carbonitride (TiCN) to enhance their wear resistance and reduce friction during cutting.
3. Toughness: In woodworking, the impact resistance of the carbide material is crucial for withstanding potential chipping or breakage during machining operations.
Comparing the performance of different carbide materials in woodworking:
– Carbide grade A:
– Carbide grade B:
– Carbide grade C:
The proper selection of carbide indexable insert materials can significantly impact the efficiency and quality of woodworking operations. By understanding the unique properties and considerations when choosing carbide materials, woodworkers can achieve superior results in their projects.
Common Mistakes to Avoid When Choosing Carbide Indexable Insert Materials for Woodworking
Choosing the right carbide indexable insert materials for woodworking is crucial to achieving optimal performance and efficiency in woodworking applications. However, there are common mistakes that woodworkers should avoid when selecting these materials in order to prevent costly errors and subpar results. Below are some common mistakes to avoid when choosing carbide indexable insert materials for woodworking:
- Ignoring the specific requirements of the woodworking project: One of the most common mistakes is overlooking the unique demands of a particular woodworking project. Different projects may require different carbide materials based on factors such as cutting speed, feed rate, and material being worked on. It’s important to carefully assess the specific requirements of each project before selecting a carbide indexable insert material.
- Not considering the hardness and toughness of the carbide material: Another mistake is failing to consider the hardness and toughness of the carbide material. While hardness is essential for wear resistance, toughness is necessary to withstand impact and prevent chipping or breakage during cutting. It’s crucial to strike a balance between hardness and toughness based on the specific demands of the woodworking application.
- Overlooking cost-effectiveness: Some woodworkers make the mistake of solely focusing on performance without considering cost-effectiveness. While high-performance carbide materials may offer superior durability and cutting capabilities, they may also come with a higher price tag. It’s important to weigh the performance benefits against the overall cost to ensure that it aligns with budget constraints.
Avoiding these common mistakes can help woodworkers make informed decisions when selecting carbide indexable insert materials for woodworking applications, ultimately leading to better outcomes and enhanced productivity.
Through careful consideration of each project’s requirements, as well as an understanding of hardness and toughness factors, woodworkers can ensure that they choose appropriate carbide indexable insert materials that not only meet performance needs but also align with their budget constraints. By avoiding these common mistakes, woodworkers can maximize their investment in carbide tools while achieving superior results in their woodworking projects.
Future Trends and Advancements in Carbide Indexable Insert Materials for Woodworking Applications
In conclusion, the selection of carbide indexable insert materials for woodworking is a crucial decision that can greatly impact the performance and efficiency of woodworking applications. As highlighted in this article, there are various types of carbide materials used in indexable inserts, each with its own unique properties and benefits. Understanding these different materials and their specific characteristics is essential when choosing the right carbide material for woodworking projects.
When considering the factors for selecting the best carbide indexable insert material for woodworking, it is important to take into account parameters such as hardness, toughness, wear resistance, and edge strength. These factors will ultimately influence the tool’s ability to withstand the demanding conditions encountered in woodworking applications.
As future trends and advancements continue to shape the field of carbide indexable insert materials for woodworking applications, industry professionals can anticipate further developments in cutting-edge technology and advanced alloys. These advancements will likely lead to even more specialized and high-performance carbide materials tailored specifically for woodworking processes. Keeping abreast of these developments will be key for woodworkers and manufacturers seeking to optimize their tooling solutions for enhanced productivity and quality output.
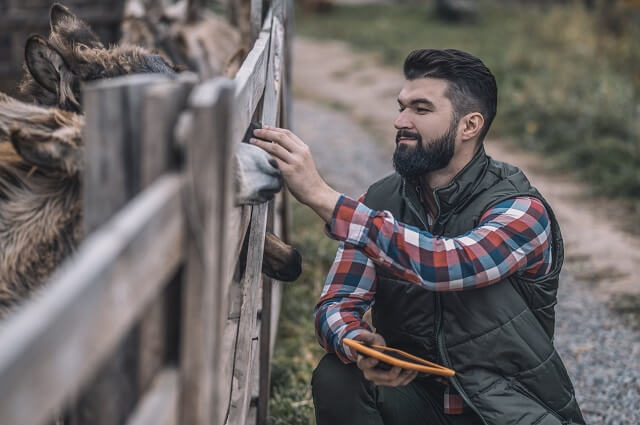
Hi everyone! I’m a woodworker and blogger, and this is my woodworking blog. In my blog, I share tips and tricks for woodworkers of all skill levels, as well as project ideas that you can try yourself.