A shaper is a versatile woodworking tool that is commonly used to shape and mold wood pieces with precision and accuracy. But what is a shaper used for in woodworking? In the world of woodworking, a shaper is a machine tool designed to create decorative edges, shapes, and profiles on wood pieces. It operates by spinning a cutter head at high speeds to cut into the material.
Shapers are an essential tool in any woodworking shop, offering craftsmen the ability to create intricate designs and details on their projects. Whether you are crafting furniture, cabinets, doors, or other wooden items, a shaper can help you achieve clean and precise results. The functionality of a shaper in woodworking extends beyond basic cutting and shaping tasks, allowing for endless possibilities in design and creativity.
In this article, we will delve into the various aspects of shapers in woodworking, from understanding the different types of machines available in the market to learning about the key components that make up a shaper.
Additionally, we will explore safety precautions when using a shaper, advantages of incorporating a shaper into your woodworking projects, common techniques employed with a shaper, maintenance tips to keep your machine in top condition, and ultimately highlight the versatility and importance of using a shaper in woodworking.
The Functionality of a Shaper in Woodworking
A shaper is a versatile woodworking tool that is used to create intricate shapes, profiles, and edges on wooden pieces. It operates by spinning a cutter head at high speeds to trim and shape wood according to the desired design. The primary function of a shaper in woodworking is to produce smooth and consistent cuts that can enhance the appearance and functionality of the final woodwork project.
One of the main uses of a shaper in woodworking is for creating decorative moldings, such as crown moldings, baseboards, chair rails, and window casings. These moldings add intricate details and visual interest to furniture pieces, cabinets, doors, or any other wooden structures. Additionally, shapers are commonly used to create raised panels, doors frames, table edges, and other custom woodwork elements that require precise shaping and detailing.
In addition to decorative applications, shapers are also useful for cutting joints like tenons, grooves, rabbets, dovetails, and lap joints. These joints are essential for connecting different pieces of wood securely while adding strength and stability to the overall structure.
By using a shaper with specialized cutters and fences, woodworkers can achieve accurate cuts for various joinery techniques. Overall what is a shaper used for in woodworking goes beyond just shaping wood surfaces; it plays a crucial role in creating strong connections between wooden elements.
Functionality | Usage |
---|---|
Create intricate shapes and profiles on wood | Decorative moldings production |
Produce smooth cuts with precision | Cutting tenons and other joints |
Enhance appearance & functionality of projects | Create raised panels & door frames |
Types of Shaper Machines Available in the Market
When it comes to woodworking, having the right tools for the job is essential. Shapers are a valuable addition to any woodworker’s arsenal, offering precision and versatility in shaping wood pieces. There are various types of shaper machines available in the market, each designed for specific tasks and projects.
Here are the different types of shaper machines that you can choose from:
- Spindle Shapers: These shapers have a vertical spindle that holds cutting tools such as blades or router bits. They are commonly used for shaping edges, profiles, and moldings.
- Power Shapers: Similar to spindle shapers, but with a more powerful motor for heavy-duty tasks and larger workpieces.
- Handheld Shapers: Portable shaper machines that allow for more flexibility and control when working on smaller projects or intricate designs.
Each type of shaper machine has its own set of advantages and limitations, so it’s important to choose the right one based on your woodworking needs and preferences.
In addition to these types, there are table-mounted shapers that can be attached to a workbench for added stability and precision. These machines offer more control over the shaping process and are ideal for intricate detailing work. No matter which type of shaper machine you choose, it will undoubtedly enhance your woodworking capabilities and allow you to create professional-quality pieces with ease.
Key Components of a Shaper Machine
A shaper machine in woodworking consists of several key components that work together to create precise and intricate wood cuts. One essential component of a shaper machine is the cutter head, which holds the cutting tool in place. The cutter head rotates at high speeds to shape the wood according to the desired design. The cutter head also allows for different types of cutting tools to be used, depending on the specific woodworking project’s requirements.
Another critical component of a shaper machine is the fence, which helps guide the wood material during shaping. The fence can be adjusted to make different cuts and shapes on the wood piece accurately. Additionally, a shaper machine includes a table where the wood material is placed for cutting. The table can be tilted or adjusted in height to achieve various angles and depth of cuts, providing versatility in woodworking projects.
Furthermore, a spindle is a crucial part of a shaper machine that connects the cutter head and powers its rotation. Spindles come in different sizes and capacities, allowing for flexibility in using various cutting tools with different diameters. The combination of these key components working together efficiently is what makes a shaper machine an indispensable tool for woodworking professionals and hobbyists alike.
Component | Function |
---|---|
Cutter Head | Holds and rotates cutting tool for shaping wood |
Fence | Guides wood material during shaping process |
Table | Where the wood material is placed for cutting, adjustable for different cuts |
Spindle | Powers rotation of cutter head, comes in varying sizes for flexibility |
Safety Precautions When Using a Shaper in Woodworking
Proper Personal Protective Equipment
When operating a shaper in woodworking, it is crucial to prioritize safety by wearing the appropriate personal protective equipment. This includes safety goggles to protect your eyes from wood chips and debris, ear protection to guard against the loud noise generated by the machine, and proper work gloves to protect your hands from sharp edges and moving parts.
Machine Inspection and Maintenance
Before using a shaper machine, it is essential to conduct a thorough inspection of the equipment to ensure that all components are in good working condition. Check for any loose or damaged parts, make sure the cutting tools are sharp and securely fastened, and confirm that all safety guards are in place. Regular maintenance of the shaper machine is also necessary to prevent malfunctions during operation.
Safe Operating Practices
When using a shaper in woodworking, it is important to follow safe operating practices to minimize the risk of accidents or injuries. Always read and understand the manufacturer’s instructions before using the machine, never remove safety guards or operate the shaper without them, and avoid wearing loose clothing or accessories that could get caught in moving parts. Additionally, make sure the workpiece is securely held in place with proper clamps or fixtures to prevent kickback or movement during cutting.
By adhering to these safety precautions when using a shaper in woodworking projects, woodworkers can create beautiful and precise pieces while protecting themselves from potential hazards. Remember that proper training, attention to detail, and respect for the power of machinery are key components of ensuring a safe woodworking environment when utilizing a shaper machine.
Advantages of Using a Shaper in Woodworking Projects
A shaper is a versatile woodworking tool that offers numerous advantages when used in woodworking projects. Whether you are a professional woodworker or a hobbyist, incorporating a shaper into your workshop can greatly enhance the precision, efficiency, and quality of your creations. Here are some key advantages of using a shaper in woodworking projects:
- Increased Versatility: One of the primary advantages of using a shaper in woodworking is its versatility. With the right accessories and tooling, a shaper can perform a wide range of cutting operations, such as shaping edges, creating profiles, making dado cuts, and more. This allows woodworkers to tackle various tasks with just one machine, saving time and space in the workshop.
- Precision Cutting: Shapers are known for their ability to deliver precise and accurate cuts, making them ideal for creating intricate details and complex shapes in woodwork. The adjustable speed settings and depth control options on a shaper allow woodworkers to achieve the desired results with ease, ensuring consistency across multiple pieces.
- Time-Saving Efficiency: Compared to manual methods like hand routing or shaping with handheld tools, using a shaper can significantly increase productivity and efficiency in woodworking projects. The power and stability of a shaper machine enable woodworkers to work faster without compromising on the quality of their craftsmanship.
In addition to these advantages, incorporating a shaper into your woodworking arsenal also offers benefits such as reduced material waste, improved safety conditions, and enhanced creativity in designing custom woodwork pieces. By understanding what is a shaper used for in woodworking and leveraging its capabilities effectively, you can elevate your craftmanship to new heights while enjoying the process of creating beautiful wooden creations.
Common Woodworking Techniques With a Shaper
Woodworkers often rely on shapers to perform a variety of woodworking techniques to achieve precision and efficiency in their projects. The versatility of a shaper machine allows craftsmen to create intricate designs, smooth edges, and consistent profiles on wooden pieces. Understanding the common woodworking techniques with a shaper can help woodworkers maximize the use of this powerful tool in their projects.
Profiling
One of the primary uses of a shaper in woodworking is for profiling edges or creating decorative moldings on wooden pieces. By using different cutter heads and fence setups, woodworkers can achieve various profiles such as beads, coves, ogees, and more. This technique adds aesthetic value to furniture pieces, cabinets, doors, and other woodworking projects.
Joinery
Shapers are also commonly used for creating precise joinery in woodworking projects. With the right cutter heads and setups, woodworkers can produce strong and accurate joints like tenons, rabbets, dovetails, and finger joints. The power and stability of a shaper allow for consistent results, making it a preferred tool for joinery tasks that require tight tolerances.
Panel Raising
Another common woodworking technique with a shaper is panel raising, which involves shaping the edges of panels to fit into frames for cabinet doors or furniture components. Using specialized cutters on a shaper machine, woodworkers can create elegant raised panels with different profiles and contours. Panel raising adds depth and dimension to the overall design of furniture pieces and enhances their visual appeal.
Incorporating these common woodworking techniques with a shaper not only expands the capabilities of craftsmen but also enables them to achieve professional-level results in their woodworking projects. Whether it’s creating unique profiles, precise joinery, or elaborate panel designs, the use of a shaper enhances efficiency and accuracy in shaping wood pieces for various applications.
Maintenance Tips for Keeping Your Shaper Machine in Top Condition
Proper maintenance of a shaper machine is crucial to ensure its longevity and optimal performance in woodworking projects. Regular maintenance not only extends the lifespan of the equipment but also improves the quality of work produced. One essential maintenance tip for keeping your shaper machine in top condition is to regularly clean the machine after each use.
Sawdust, wood chips, and debris can accumulate in various parts of the machine, affecting its functionality over time. Use a vacuum or compressed air to remove any build-up and keep the machine running smoothly.
In addition to cleaning, it is important to lubricate the moving parts of the shaper machine to prevent friction and wear. Apply lubricant to the spindle, bearings, and other components as recommended by the manufacturer. This will help reduce heat generated during operation and prevent premature damage to the machine.
Regularly inspecting and tightening loose bolts and screws is another important maintenance tip for ensuring that your shaper machine remains in top condition. Loose fasteners can cause vibrations and affect precision cutting, so it is essential to check them periodically.
Furthermore, checking and replacing worn out or damaged parts on your shaper machine is essential for maintaining its performance. Keep an eye on the cutter heads, belts, pulleys, and other components that may show signs of wear and tear over time.
Replace any damaged parts promptly to prevent further damage to the machine or compromise on safety during operation. By following these maintenance tips diligently, you can ensure that your shaper machine operates efficiently and effectively for years to come, allowing you to achieve professional results in your woodworking projects.
Conclusion
In conclusion, a shaper is an essential tool in woodworking that offers versatility and precision in shaping and molding wood. Whether you are creating intricate designs or simple cuts, a shaper machine can help you achieve the desired results with efficiency.
One of the key advantages of using a shaper in woodworking projects is its ability to produce consistent and uniform cuts. This consistency is vital in ensuring that your pieces fit together seamlessly and that your final product looks polished and professional. Additionally, shapers allow for a wide range of shapes and profiles to be created, giving woodworkers the flexibility to bring their creative visions to life.
It is important to note that safety should always be a top priority when using a shaper machine. By following proper safety precautions, such as wearing protective gear and ensuring the workspace is clear of any obstructions, woodworkers can prevent accidents and injuries.
Regular maintenance of the shaper machine is also crucial to prolonging its lifespan and ensuring it operates smoothly. Overall, understanding what a shaper is used for in woodworking can greatly improve the quality and efficiency of your projects.
Frequently Asked Questions
Is a Shaper the Same as a Router?
A shaper and a router are similar woodworking tools but have key differences. A shaper is typically larger and more powerful than a router, designed for heavier cutting tasks. It also operates vertically instead of horizontally like a router.
What Does Shaper Do?
The primary function of a shaper is to cut profiles into wood or other materials by using cutter heads with various shapes and sizes. It allows for precise shaping of edges, curves, and other intricate designs in woodworking projects. Shapers are commonly used in cabinetry, furniture making, and millwork.
Why Do I Need a Shaper?
Having a shaper in your workshop can significantly increase your capabilities for creating custom wood pieces with detailed designs. Whether you’re working on trim molding, raised panels, or joinery, a shaper provides the precision and power needed for these tasks. It can save time and effort compared to hand tools while ensuring accuracy in your workmanship.
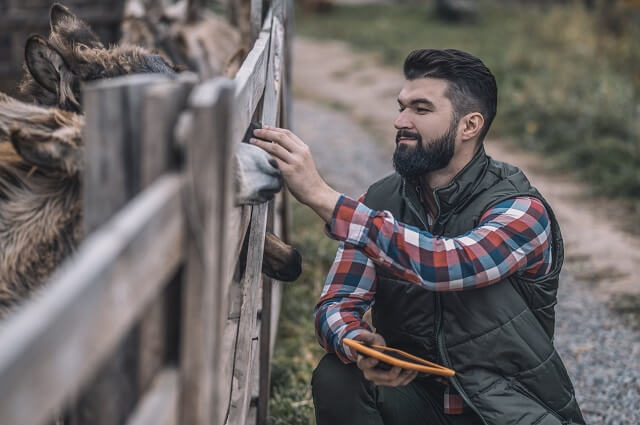
Hi everyone! I’m a woodworker and blogger, and this is my woodworking blog. In my blog, I share tips and tricks for woodworkers of all skill levels, as well as project ideas that you can try yourself.