Introduction
A benchtop thickness is a measurement that refers to the length of the panel used to make a workbench surface. This length is typically measured in millimeters, or “mm”, and will vary from bench to bench depending on how thick the manufacturer decides it should be. Generally speaking, most woodworking benches will have a top between 25mm (1″) and 50mm (2″) thick. The thicker boards can also provide more support for heavier tools and materials during projects, but they can also be more expensive than their thinner counterparts. Other features can determine how thick a workbench should be, such as its use environment and the weight of what will rest on it. It’s important for craftspeople to understand the details about their project before deciding on the right thickness for their desired benchtop. Knowing what kind of activity you plan on doing with your workbench and where it will go can make sure you get one that suits your needs while still being cost-effective.
Benefits of a Properly Sized Benchtop Thickness
Having a properly sized benchtop thickness with the right amount of mass can help you become more productive and efficient when working in your woodworking shop. The extra mass provides added stability to help reduce vibrations which could slow down or distort your work. The larger top surface allows for a greater range of motions during tasks, allowing for quicker and smoother workflows. Additionally, benchtops that are properly sized will be less prone to damage from overloading, as it will distribute the weight evenly across its surface. This also helps protect any sensitive equipment stored on the workspace. Finally, a properly sized benchtop thickness is safer overall since heavier surfaces offer more resistance against tipping and other accidents. With all these advantages, you’ll be able to create beautiful projects faster and with fewer risks.
What to Consider When Selecting the Right Thickness
When selecting a thickness for your woodworking benchtop, there are several factors you should consider. One is the type of projects you typically work on. If most of your projects involve larger pieces of wood or lumber, you will likely need a thicker benchtop to prevent vibrations from working their way up from the base and into your workpiece. It also helps to evaluate how often heavy items such as tools, supplies, and other materials will be placed on top of the bench. A thicker benchtop is better suited to supporting heavier objects like these than a thinner one. Furthermore, think about how much weight the entire bench itself needs to hold up; if you are concerned with the potential effects of unevenly distributed weight on its structure, opting for a thicker option may help increase its strength and durability over time. Finally, carefully taking into account your individual desired outcome should always be your top priority in making any decision when it comes to woodworking project preparation and planning!
Different Woods and Their Appropriate Thickness Levels
When it comes to woodworking benchtops, the thickness of the wood needed depends on the type of wood and its strength. If a wood isn’t strong enough for certain activities, such as cutting or hammering, then it’ll need to be thicker than normal. Some typical woods used in woodworking benchtops are oak, maple, mahogany, cherry, and pine. All these woods have different strengths and characteristics that determine their ideal thickness level for use in benchtops.
Oak is an all-around Wood suitable for multiple applications due to its straight fibres that offer rigidity and strength. It’s usually used between 1” to 2-1/8” thick in a benchtop depending on how much strength is required.
Maple is known for its durability and smooth surface which makes it an excellent choice for benchtops. Maple can range anywhere from ¾” thick up to 1-3/4” thick when used in a workbench strong enough to support significant weight like hand tools or heavy machinery.
Mahogany is another great choice due to its ability to resist color fading over time with contact from water or other liquids compared to most hardwoods. Typically millworks sell mahogany at 1 ¼” thick but user should go slightly thicker if more stability is required up to a maximum of 2-1/8″.
Cherry has unique colors that add warmth and ambiance but also reduce impact damage better than other woods as it’s flexible yet springy when bent too far creating tensile strength within its fibers that rebounds back into normal form. Cherry wood typically ranges from 7/8″ -1 ¼” Thickness depending on this desired application from a user ranging from furniture making up to 6mm steel fabrication workpiece clamping supports.
Pine is one of the lightest of all hardwoods so it’s best suited for decorative pieces where strength isn’t needed but softness must be maintained; generally 3/4” – 1 ½’ thick planks will do when building furniture This common softwood species because they’re easy to machine while still having good finishing qualities allowing even beginners with low skill levels create beautiful projects with little effort or money expended
Tools Needed for Working with Thickness
In order to successfully and safely work with woodworking benchtop thickness, one needs to invest in various tools. Without the right tools, it is impossible to achieve professional-quality results. A few of the essential tools needed include a power planer and jointer, hand planes, a thickness sander, a belt or oscillating spindle sander, chisels, and specialty knives. For measuring thickness accurately and consistently, one also needs dial calipers or sliding blades. Having sharp blades/knives on planes and chisels is also important for producing finer results. Finally, an adjustable straight edge can be used for flattened edges and faces for creating consistent widths in boards. It is worth investing in quality tools when starting out as buying better ones initially will prevent needing multiple replacements later on down the road.
Ideal Benchtop Thickness Recommendations
When building a woodworking benchtop, the recommended thickness is between 2-3 inches. This provides an ideal blend of durability and stability, as well as a weight that won’t be too heavy for your workspace. The thicker the benchtop, the more solid and sturdy it will be, but also the heavier it will be. Three inch thick tops are sturdier than two inch tops and usually require fewer supports.
When thinking about which thickness works best for you, consider how and where you’ll use your workbench. If portability is important to you, then a lighter two inch top might be your ideal choice. However, if you’re looking for extra support when clamping pieces together or attaching machinery to your workbench then a thicker three inch option could provide added strength and benefit. Additionally, depending on the uses you have in mind for your benchtop, choosing certain types of woods can also be advantageous; hardwoods such as maple or oak can provide an especially durable solution to your woodworking needs and can often give better results than softer woods like pine or poplar. It’s important to remember that the quality of wood used greatly affects the end results – choose boards carefully to ensure that they are without knots or signs of warping before assembly. No matter what thickness or type of wood you ultimately decide on for your wooden workbench top, always make sure to properly seal it with a protective finish for extra longevity and protection from wear and tear over time.
Prepping the Wood for Best Thickness Results
Prepping the wood before cutting it to the desired thickness is essential for producing the best results. It starts with drying out the wood used for the project. Having too much moisture in the wood can make it difficult to achieve even thickness levels, or could warp and distort the board as you’re using it. Luckily, this can be avoided by allowing enough time for the wood to dry out completely – typically a few weeks – before attempting to cut into it.
Also important is making sure that boards are ripped straight so that they can then be jointed together on the benchtop. In order to easily detect any warps or bends throughout its length, use a straight edge across one side of it. If needed, any imperfections can then be adjusted with a plane (or other similar tool) before setting up your benchtop thickness planes. This will ensure proper consistency in each board’s finish and performance during final construction steps when attaching them together on finished pieces.
Tips and Techniques for Handling Thickness
Woodworking benchtop thickness is a common concern for many woodworkers. Depending on the project, different thicknesses can be needed as well as special tools to achieve the right amount. Here are some tips and techniques that can help when handling different levels of thickness in a woodworking benchtop:
1. Start with an understanding of what your desired result should be. Measure precisely and carefully and account for any warping or defects in the wood before cutting. Make sure the pieces you are working with are the same size and shape by using a combination square or straightedge to check it.
2. Use fine-toothed saws when cutting thicker pieces of wood to ensure smooth, clean cuts without wasting too much material in between cuts. A bandsaw or jigsaw can also be used for this purpose but be sure to use appropriate safety equipment such as goggles and dust masks during use.
3. Once each piece is cut according to plan, you’ll need to join them into one piece of wood with glue and clamps or screws depending on what’s required for your project. Take care to evenly spread the clamping force around each section of your workpiece so there isn’t any excess tugging that could cause misalignment while joining them together.
4. Sanding is one of the most important steps in a successful outcome when dealing with thick baize material; this is due to its volatile nature when cut improperly or roughed up during assembly processes which makes it more difficult to shape later on. Start by lightly sanding one side at a time and moving gradually towards finer grits until desired level of finish is achieved respectively along the sides, edges, corners, etc.. Be sure not invest too much pressure while sanding as this may cause abrasions or an uneven look once complete!
Conclusion
The right benchtop thickness depends on the needs of the craftsman and the type of work they will be performing. It should be taken into consideration when selecting a benchtop as it can significantly impact quality and performance. Generally speaking, a thicker benchtop provides greater stability and heavier loads can be supported. Meanwhile, thinner models are lighter, more portable, and may provide limited access to complex projects. Deciding between the two is a matter of determining the balance between support and cost effectiveness.
When selecting a benchtop thickness, there are several factors to consider. Firstly, consider the nature of your work. If you perform detailed work that requires precision cutting or intricate fitting but do not routinely handle heavy items, then a thinner benchtop would be suitable for your needs. On the other hand, if your tasks involve manipulating or securing large pieces or any kind of machining operation then a thicker material is needed for strength and stability. The location where you plan to use it also affects whether a thin or thick model is the most suitable; if space is limited then opting for a thinner option may be preferable as they often require less space than their thicker counterparts. Finally, your budget must always be kept in mind; while thicker benches may cost more initially they generally offer long-term value due to increased durability so this should be weighed up against any potential savings from opting for an initially cheaper alternative.
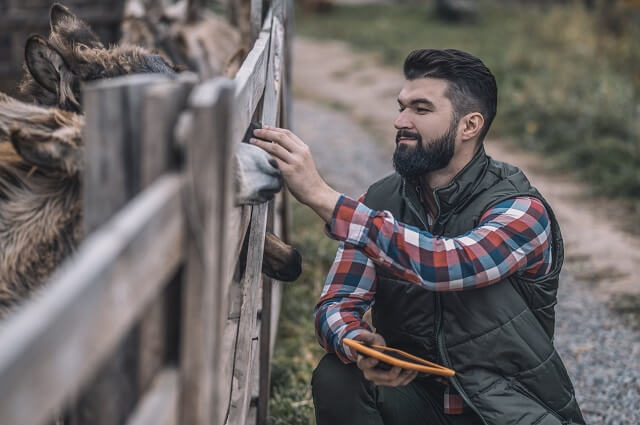
Hi everyone! I’m a woodworker and blogger, and this is my woodworking blog. In my blog, I share tips and tricks for woodworkers of all skill levels, as well as project ideas that you can try yourself.