Introduction
The woodworking flute is used in many different forms of woodworking, and has a history stretching back centuries. This traditional handcrafting tool has evolved over the years from early designs that were crafted from bamboo and animal bones, to the highly advanced metal versions of today. The modern woodworking flute is made up of a circular tube with several parts including an external thread, an internal lip for attaching tools, and a removable head for tight areas.
The flute provides many benefits to both beginners and experienced woodworkers alike. It can be used to make intricate cuts into hardwoods or softwoods due to the flexibility of its design, allowing you to measure and cut accurately along curves or straight lines. Additionally, they can be extremely helpful when creating delicate details such as jigsaw puzzles or ornamental carvings. They are also great for creating clean finishes on wooden surfaces as they can easily remove debris while also offering better control than sanding blocks or files.
Woodworking flutes have been respected craft tools throughout time thanks to their versatility and precision. They have been referenced in ancient texts of numerous cultures across the globe but were first created centuries ago by Metalsmiths in East Asia who utilized them for fine metal work instead of woods; because metals were easier to carve then trees! It wasn’t until much later on that artisans realized the potential advantages these tools had when it came to their preferred material – wood! Today’s modern versions are highly refined pieces of engineering, capable of taking a multitude of projects all around the workbench with ease, accuracy and strength.
Types of Woodworking Flutes & Examples
The type of flute is determined by the material it is made out of. Different types of woodworking flutes include those made of metal, plastic, or wood.
Metal Flutes: Metal flutes are usually made from brass, aluminum, or steel. Examples include instruments like the pennywhistle and the piccolo. These flutes can produce a loud sound, which makes them ideal for classical and jazz music. The range of notes that can be produced on these instruments is also quite wide, giving them versatility within different musical pieces.
Plastic Flutes: Plastic flutes are typically cheaper than their metal counterparts and are often used by beginners who are learning how to play the instrument. They come in a variety of colors and sizes and can produce a softer sound that blends nicely with other instruments in an ensemble. Examples of plastic flutes include recorders, transverse flutes, ocarinas, and quenas.
Wooden Flutes: Wooden flutes are often crafted by experienced luthiers using specialized tools and techniques to ensure they give off a warm tone when played. These types of flutes often contain keys like those found on brass instruments to help control pitch or provide extra notes in different ranges. Examples include concert (or Western) flute, Native American-style wooden flute, alto-flute (an octave lower than conventional), bass flute (two octaves lower than conventional), and double contrabass (three octaves lower than conventional).
Materials Used for Woodworking Flutes & How They Affect Performance
There are many materials used in the construction of woodworking flutes, such as timber and metal. Timber is commonly used as the body of a flute due to its warm sound and lightweight characteristics. Along with the various sizes and shapes available, timber also provides an ideal material for creating beautiful designs on a flute. On the other hand, metal is usually used for creating intricate keywork on a flute and both metal and wooden components are often combined to create an instrument with unparalleled sound quality.
Metal is often key when it comes to performance, being both tough enough to stand up to years of wear-and-tear as well as being flexible and versatile enough to allow for fine adjustments in pitch or intonation. For example, gold or silver plating can be added to fingerholes in order to increase airtightness around them. Similarly, some metals can absorb more vibrations from windway surfaces than others – with sterling silver typically absorbing more than brass – thus providing warmer tone coupled with improved response times when playing notes at higher dynamic ranges. Additionally, soldering techniques like brazing can be employed during assembly of keys on metal components resulting in increased mechanical stability compared to less advanced techniques such as gluing. Furthermore, metals are capable of bearing relatively high loads without affecting their playability. This property makes metals ideal for crafting levers on palm keys that move against springs – giving players greater control over dynamics when playing soft or loud passages requiring complex fingering technique changes i.e transitions between registers (high & low pitches). Grand Ecole models come equipped with multiple springs that precisely support the adjustment lever’s fulcrum which ensures efficient transferral of force when pressing down a note while still providing maximum flexibility when playing mechanically demanding passages found in concert pieces requiring intense finger speed/accuracy changes.
Techniques & Best Practices for Using Woodworking Flutes
Using woodworking flutes is an important component for creating beautiful furniture pieces. The technique involves cutting a groove, or flute, into your wood to add decorative detailing. To ensure successful implementation of this process, there are best practices to keep in mind.
One of the first best practices for using woodworking flutes is to use sharp chisels and routers. Properly sharpened tools help create clean cuts and prevent destruction of the wood when carving your grooves. Additionally, setting the depth of cuts should be done cautiously so you do not cut too deep and damage the material being worked on.
The grain direction of the wood can also affect how your grooves turn out, especially while planning curves and complex designs. In most cases it is best to align smaller cuts with the grain so that they remain crisp and straight-edged throughout their extentions. A miter saw or band saw can also be used to further refine complicated projects, allowing deeper detail work by keeping precision levels high throughout the process.
Finally, after you have completed your project keep in mind that it takes practice to master any technique; take all feedback as a learning opportunity to better your skills in future projects!
Factors to Consider When Choosing the Right Woodworking Flute
When choosing a woodworking flute, there are several important factors to consider. The first is the type of material being turned—wood, plastic, metal, or other. Depending on the material, different types of flutes may be needed to achieve the desired finish.
Other factors in selecting a flute include the number of “teeth” that make up each cutting edge, how efficiently it produces chips and shavings during use, and which type of bit is best for creating specific cuts or designs. For example, a spiral-style flute will work best when designing intricate cuts on any size of wood or metal stock. Troublesome projects can often be made easier with specially designed T-slot bits for improved accuracy and stability as well.
The size of a woodworking flute’s tip should also be taken into account when selecting one for use. Bigger tips mean larger shavings will become easier to produce from wider stocks being cut or carved while smaller tips provide more control over finer details. Finally, personal preference is an important factor when selecting the right tool. Having the right equipment makes all the difference when it comes to achieving accurate results with excellent end products that are perfectly crafted and finely finished!
Popular Accessories for Woodworking Flutes
Woodworking flutes are a popular tool for creating intricate and beautiful wooden sculptures. They come in various sizes, styles and materials to suit the needs of any project. Accessories for woodworking flutes can help enhance the beauty and durability of the finished product.
One popular accessory is a special type of router bit designed specifically for use with woodworking flutes. These special router bits minimize vibration while carving, which helps achieved a smooth finish on whatever woodsculpting project you’re working on. The right router bit can also help reduce scrap wood when carving out delicate details.
Another useful accessory for flutework is a high-quality sharpener and honing oil, which helps keep blades nice and sharp for a longer period of time, reducing the chances of mistakes due to dull edges. There are many different types of sharpeners available depending on your preferences or budget, so it’s important to do your research and decide what works best for your tools.
If you’re looking to add an extra level of detail to carved wood blocks, another great accessory is an engraving pen or burr toolkit. Engraving pens allow you to add lines, patterns or even small shapes along the top or bottom portion of your pieces with precision control, while burr tools are great for hollowing out certain areas with minimum effort and maximum efficiency.
Finally, some extra finishing touches can be added with sandpaper kits or polishing stones. Sandpaper allows you to further refine surfaces before painting them or applying other finishes, while polishing stones give them an enchantingly smooth touch that always stands out in any craftsmanship project. No matter which accessories you choose for completing flute projects, make sure they fit in with your budget but still provide quality results every time!
Common Questions & Answers About Woodworking Flutes
Q: What is a woodworking flute?
A: A woodworking flute is a cutting tool used to cut, shape and drill holes for all types of woodworking projects. It consists of two parts, the straight-edged section which does the bulk of the work, and the spiral head which guides the cutting edge along any curved surface. It can be used in a variety of applications such as grooving, rebating, doweling and moulding.
Q: How do I use a woodworking flute?
A: To use a woodworking flute, you will need to determine what type of pattern or shape you want to produce from the material being worked on. You then adjust the bit or shank size accordingly and insert it into your drill chuck (be sure to use safety glasses when doing so). Finally, you begin cutting by guiding the bit around your desired pattern or shape in either a clockwise or counter-clockwise direction. Be sure to vary your speed depending on how hard or soft the material being worked on is
Q: Are there any other uses for a woodworking flute?
A: Yes! Woodworking flutes can also be used to produce decorative patterns in furniture pieces by tracing around a template or stencil design. Additionally, they can also be used to create different sizes and shapes of holes in casework pieces that are commonly seen in drawers and cabinetry works.
Conclusion
The woodworking flute is a type of pipe that has become popular in recent years due to its many advantages. It is easy to construct, can be ordered from various suppliers, and comes in a range of different sizes and shapes. Furthermore, this type of flute can create unique musical tones and provide the artist with an endless amount of creative possibilities. The woodworking flute also has several distinct advantages over other types of pipes such as metal or synthetic flutes due to its warm sound quality which adds depth and resonance to music pieces. With its ability to create captivating soundscapes, versatile capabilities, and countless customization options, it is no wonder why the woodworking flute continues to be a favorite amongst musicians around the world.
Resources & Further Reading
A woodworking flute is a woodwind instrument which consists of a slender tube that is closed at one end and has holes along the side which are covered by keys for the player to produce melodies. It produces sound when air is blown across the opening at the top of the tube, usually with a wooden reed inserted in the opening. The body of a woodworking flute is typically made out of either cedar, ebony, rosewood or maple. There are also some rarer varieties that use exotic woods such as cocobolo or kingwood.
The process of making a woodworking flute requires many intricate steps and precision, from selecting the wood, cutting it to size and shape and assembling different parts of it together. The player may also want to customize their flute with decorative details such as inlays, engravings or electroplating for an elegant finish on the instrument’s exterior. Woodworking flutes usually require frequent upkeep and maintenance in order to keep them in good condition, such as oiling parts or occasionally replacing pads when they become worn out due to overuse.
Furthermore, there are now courses available that teach beginners how to construct their own wooden wind instruments from scratch and experienced luthiers who specialize in repairing and customizing ornate handcrafted models. For those looking for resources related to playing this wonderful instrument, numerous books have been published covering topics such as playing techniques, traditional songs and scales that can be used with your newfound skillset. As well as this, attending local workshops held by experienced players is a great way to learn more about how to play your handmade piece properly for maximum effect.
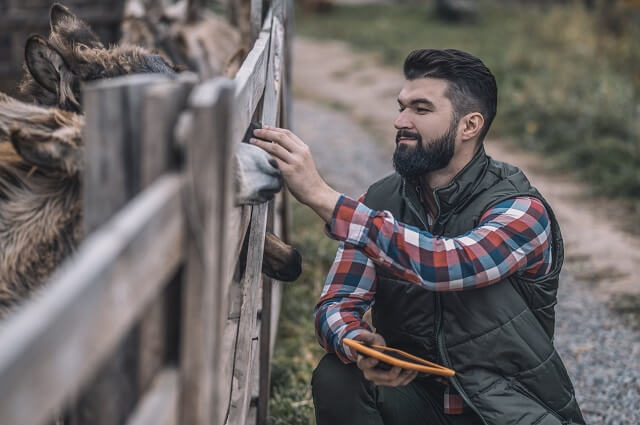
Hi everyone! I’m a woodworker and blogger, and this is my woodworking blog. In my blog, I share tips and tricks for woodworkers of all skill levels, as well as project ideas that you can try yourself.