Woodworking machinery plays a vital role in the woodworking industry, allowing artisans and craftsmen to transform raw materials into beautiful and functional pieces of furniture, cabinets, and more. While there are numerous woodworking machinery options available on the market, there is also an opportunity to create your own equipment.
In this article, we will explore the importance of woodworking machinery, as well as the benefits of making your own. Whether you are a hobbyist or a professional woodworker, understanding how to make woodworking machinery can provide you with greater flexibility, customization options, and even cost savings.
Woodworking machinery is essential for efficiently cutting, shaping, and joining various pieces of wood. It allows woodworkers to achieve precise results and tackle complex projects that would be difficult or time-consuming to accomplish by hand alone. From table saws and planers to routers and jointers, these tools not only speed up the production process but also ensure accuracy and consistency in every detail.
Making your own woodworking machinery offers several significant advantages. Firstly, it provides an opportunity for customization based on your specific requirements. By designing your equipment from scratch or modifying existing models, you can tailor it to your unique needs and preferences. Secondly, building your own machines can be a cost-effective option in comparison to purchasing brand-new equipment. With a little bit of technical knowledge and resourcefulness, you can obtain high-quality results without breaking the bank.
In the following sections of this article, we will dig deeper into understanding different types of woodworking machinery, explore step-by-step guides on designing your own equipment, discuss selecting the right materials and components for optimal performance, list the tools needed for construction with recommended brands included. We will also emphasize safety precautions while building homemade woodworking machinery to ensure a secure working environment.
Lastly we will guide you through assembly process from start to end providing troubleshooting techniques and maintenance tips along way ensuring longevity of your self-built woodworking machinery.
Understanding the Different Types of Woodworking Machinery
Woodworking machinery plays a crucial role in the woodworking industry, making tasks more efficient and precise. Understanding the different types of woodworking machinery is essential for woodworkers who want to create their own machinery. This section will explore the various types of woodworking machinery available and their specific functions.
- Table Saw: A table saw is one of the most common types of woodworking machinery. It consists of a circular saw blade mounted on an arbor that is driven by an electric motor. The blade protrudes through a slot in a flat surface, allowing users to make straight cuts on wooden boards.
- Jointer: A jointer is used to flatten and straighten an edge or face of a wooden board. It consists of a rotating cutter head with multiple blades that removes material from the surface of the wood as it passes over an adjustable fence.
- Planer: A planer is used to create smooth, flat surfaces on wooden boards by removing material from their faces. It consists of a cutter head with multiple blades that spins rapidly, passing over the surface of the wood.
- Band Saw: A band saw uses a continuous band blade with teeth along one edge to cut various materials, including wood. It can make curved and irregular cuts due to its flexible design.
- Drill Press: A drill press is a stationary drilling machine that allows for accurate drilling at specific angles and depths in wood. It consists of a motor-driven drill head mounted on a column, providing stability during operation.
- Router: A router is a versatile tool used for shaping edges, cutting grooves, and creating intricate designs in wood. It can be handheld or mounted on a table for more precise control.
- Miter Saw: A miter saw, also known as a chop saw or drop saw, is designed to make accurate crosscuts and miter cuts in wood at various angles. It features a circular blade mounted on a pivoting arm that can be angled and lowered onto the material.
Understanding the different types of woodworking machinery allows woodworkers to select the appropriate tools for their projects. Each type of machinery serves a specific purpose and offers unique capabilities. By familiarizing themselves with these machines, woodworkers can enhance their woodworking skills and achieve more professional results.
Step-by-Step Guide on Designing Woodworking Machinery
Designing your own woodworking machinery can be a rewarding and cost-effective way to meet your specific needs in the woodworking industry. Whether you are a hobbyist or a professional, having the ability to create customized machinery gives you greater flexibility and control over your projects. In this section, we will provide a step-by-step guide on how to design woodworking machinery, including essential steps and considerations.
- Identify Your Needs: The first step in designing woodworking machinery is identifying your specific needs and requirements. Consider the type of projects you will be working on, the desired output, and any unique features or functionalities you require. This will serve as the foundation for designing your machinery.
- Research Existing Designs: Before diving into the design process, it is important to research existing designs and technologies in order to understand what has already been done. Analyze different types of woodworking machinery available in the market and study their functions, features, and mechanisms. This will help you gain inspiration and insights for your own design.
- Create a Design Concept: Once you have gathered enough information and ideas, it’s time to create your own design concept. Sketch out your ideas on paper or use computer-aided design (CAD) software to visualize your concept more accurately. Consider factors such as dimensions, materials, components, safety features, ergonomics, and ease of use while creating the design concept.
- Consult with Experts: It can be beneficial to consult with experts or professionals in the field of woodworking machinery during the design process. They can provide valuable input based on their knowledge and experience that may help refine or improve your design concept.
- Develop Detailed Drawings: Once you have finalized your design concept, it’s time to create detailed drawings that include all the necessary measurements, specifications, and components required for construction. These detailed drawings will serve as a blueprint for building your woodworking machinery.
- Test Your Design: Before proceeding with construction, it is recommended to test your design concept virtually using simulation software or create a prototype to identify any potential flaws or areas for improvement. This will help ensure that your final woodworking machinery design will meet your expectations and requirements.
By following these steps and considerations, you can successfully design your own woodworking machinery. Remember to take your time during the design process and iterate as needed to create a machine that is efficient, safe, and tailored to your specific needs.
Step | Description |
---|---|
Identify Your Needs | Consider the type of projects, desired output, and unique features required. |
Research Existing Designs | Analyze different types of woodworking machinery available in the market. |
Create a Design Concept | Sketch out ideas on paper or use computer-aided design (CAD) software. |
Selecting the Right Materials and Components
When it comes to making your own woodworking machinery, one of the most crucial aspects is selecting the right materials and components. Choosing high-quality materials and components ensures that your homemade machinery will have excellent durability and performance. In this section, we will explore the key considerations when selecting materials and components for your woodworking machinery.
Durability
Durability is a vital factor to consider when choosing materials for your homemade woodworking machinery. The constant stress and pressure exerted on the machinery require sturdy materials that can withstand heavy use over time. Opt for durable options such as high-grade steel, aluminum, or cast iron for critical structural parts like frames, tables, and bases. These materials offer robustness, stability, and longevity to withstand the demands of wood processing.
Performance
Apart from durability, you also need to prioritize performance when selecting materials and components. For instance, motors play a significant role in powering various tools in woodworking machinery. Consider high-performance motors that can deliver sufficient power output consistently without compromising efficiency. Additionally, choose bearings with high load capacities to ensure smooth operation under heavy loads while minimizing wear and tear.
Compatibility
Another important consideration is compatibility between different materials and components within your homemade woodworking machinery. Ensure that all parts are designed to work together seamlessly to avoid any issues with fitting or functionality. You may consult technical specifications or seek guidance from experts in the field to ensure compatibility between different elements within your machinery.
By carefully selecting durable materials that deliver optimal performance while being compatible with each other, you can ensure that your homemade woodworking machinery operates smoothly and efficiently for years to come. Taking the time to research reliable suppliers for quality materials will contribute significantly to the overall success of building your own woodworking machinery.
Tools and Equipment Needed
When it comes to building woodworking machinery, having the right tools and equipment is crucial. This section will provide a comprehensive list of the tools and equipment needed for this project, along with their uses and some recommended brands.
Power Tools
Power tools play a vital role in building woodworking machinery due to their efficiency and precision. Some of the essential power tools you’ll need include:
- Table Saw: A table saw is used for cutting large wooden pieces with accuracy. Recommended brands include DeWalt, Bosch, and SawStop.
- Drill Press: Essential for drilling precise holes, a drill press helps create accurate joints in woodworking machinery. Brands like Jet, Craftsman, and WEN offer reliable options.
- Router: A router aids in shaping wood surfaces and creating intricate patterns. Bosch, Makita, and Festool are known for producing reliable routers.
Hand Tools
While power tools are essential, hand tools also have their place in building woodworking machinery. Some important hand tools include:
- Chisels: Chisels are used for carving out wood and making detailed slots or cuts. Stanley, Narex, and Two Cherries offer high-quality chisels.
- Hand Planes: Hand planes help smooth and flatten wood surfaces for precise fitting of components. Popular brands include Lie-Nielsen, Veritas, and Stanley.
- Measuring Tools: Accurate measurements are key in woodworking machinery construction. A combination square, tape measure, and calipers from reputable brands like Starrett or Stanley should be included in your toolbox.
Safety Equipment
Safety should always be a top priority when working with woodworking machinery. Ensure you have the following safety equipment before starting your project:
- Safety Glasses: Protecting your eyes from flying debris is crucial; choose safety glasses that meet ANSI standards.
- Dust Mask/Respirator: Woodworking generates a lot of dust, and wearing a mask or respirator will help protect your lungs from harmful particles.
- Hearing Protection: Power tools can be noisy, so investing in earplugs or earmuffs is essential for preventing hearing damage.
Remember, the brands mentioned here are just recommendations. It’s always important to research and read reviews to find the best options for your budget and needs. Having the right tools and equipment ensures that you can build woodworking machinery efficiently and safely.
Safety Precautions
When it comes to working with woodworking machinery, safety should always be the top priority. Building your own woodworking machinery can be a rewarding and cost-effective endeavor, but it is crucial to take the necessary precautions to prevent accidents and injuries. This section will highlight the importance of safety measures and guidelines while building woodworking machinery, ensuring a secure working environment.
First and foremost, it is essential to wear appropriate personal protective equipment (PPE) throughout the construction process. This includes safety glasses or goggles to protect your eyes from flying debris or sawdust, hearing protection such as earplugs or earmuffs if working in a noisy environment, and sturdy work gloves to protect your hands from sharp edges or rough surfaces. Additionally, a dust mask should be worn when working with materials that generate significant amounts of dust.
Before starting any construction, thoroughly familiarize yourself with the plans or blueprints for your woodworking machinery. It is crucial to have a clear understanding of each step before proceeding. Take the time to read through any accompanying instructions or manuals provided by manufacturers. This will help you identify any potential hazards associated with specific tools or equipment you may be using.
During the construction process, pay close attention to electrical safety. When connecting wires or installing electrical components, always make sure that power sources are turned off and unplugged before making any adjustments. Inspect all cords and plugs for signs of damage and replace them if necessary. Proper grounding is also essential to prevent electrical shock, so ensure that all electrical connections are secure.
Lastly, keep your workspace clean and organized throughout the construction process. This includes regularly removing sawdust, wood chips, or other debris that may accumulate during the build. Cluttered work areas increase the risk of trips and falls, so make sure tools are properly stored away when not in use.
By following these safety precautions, you can create a secure working environment while building your own woodworking machinery. Remember, it is always better to prioritize safety and take preventative measures rather than risk potential accidents or injuries.
Assembly and Construction Process
To build your own woodworking machinery, it is important to have a clear understanding of the assembly and construction process. This section will break down the construction process into step-by-step instructions, explaining each stage in detail to guide readers through the assembly of their homemade woodworking machinery.
- Planning: Before starting the assembly process, it is crucial to have a well-thought-out plan in place. Begin by reviewing your designs and ensuring that you have all the necessary components and materials readily available. This will help streamline the construction process and prevent any delays or issues along the way.
- Preparing the Workspace: Set up a clean and organized workspace that is free from clutter and distractions. Ensure proper lighting and ventilation for a comfortable working environment.
- Initial Assembly: Start by assembling the base frame of your woodworking machinery according to your design. Use high-quality fasteners such as screws or bolts to ensure stability and durability.
- Mounting Motors and Components: Carefully mount motors, belts, pulleys, gears, or any other components required for the proper functioning of your woodworking machinery. Follow manufacturer instructions and use appropriate hardware to secure them in place.
- Wiring and Electrical Connections: If your woodworking machinery requires electrical power, carefully route wires following electrical codes and safety guidelines. Use designated wire connectors or terminal blocks for secure connections.
- Fine-Tuning and Calibration: Once all components are securely mounted, it is time to fine-tune your homemade machinery for optimal performance. Check alignments, adjust tension on belts or chains if needed, and calibrate any necessary settings according to your design specifications.
- Safety Adjustments: Prioritize safety by installing necessary safety features such as emergency stop buttons, guards, or switches that prevent accidental startups or protect operators from potential hazards.
- Testing: Before putting your homemade woodworking machinery into regular use, thoroughly test its functionality and performance. Run different operations at various speeds to ensure smooth operation and proper functioning of all components.
- Documentation and Maintenance: Keep a record of your assembly process, noting any modifications or adjustments made along the way. Regularly inspect and maintain your machinery to ensure its longevity and efficient performance.
By following these step-by-step instructions, you can successfully assemble your homemade woodworking machinery. However, it is important to note that this process may vary depending on the specific design and type of machinery being built. Always refer to manufacturer instructions, seek professional advice when needed, and prioritize safety throughout the construction process.
Troubleshooting and Maintenance Tips
Once you have successfully built your own woodworking machinery, it is important to know how to troubleshoot common issues and properly maintain it to ensure its longevity. With regular maintenance and timely troubleshooting, you can keep your homemade woodworking machinery in excellent working condition. Here are some valuable tips to help you troubleshoot and maintain your machinery:
- Regular Cleaning: One of the most crucial aspects of maintaining woodworking machinery is keeping it clean. Sawdust, debris, and dust particles can accumulate over time and affect the performance of your equipment. To prevent this, make sure to clean your machinery regularly by vacuuming or wiping down all surfaces. Pay special attention to hard-to-reach areas such as corners or crevices where dust may settle.
- Lubrication: Proper lubrication is essential for smooth operation and reduced friction in woodworking machinery. Regularly inspect all moving parts such as bearings, hinges, sliders, or blades, and apply the appropriate lubricant recommended by the manufacturer. This will not only keep your machine running smoothly but also extend its lifespan.
- Blade Maintenance: The blade is one of the most important components of woodworking machinery. It is crucial to keep it sharp for precise cuts and safety reasons. Check regularly for signs of dullness or damage on the blade’s edges. If necessary, sharpen or replace the blade according to manufacturer guidelines.
- Belt Tension: Belts play a significant role in transmitting power in many types of woodworking machinery such as table saws or planers. Over time, belts can become loose or worn out, affecting the overall performance of your machine. Check belt tension regularly using manufacturer guidelines and adjust if necessary.
- Electrical Connections: Ensure that all electrical connections are secure and free from corrosion or damage. Loose connections can lead to power fluctuations or electrical shorts, which can be hazardous. Regularly inspect and clean electrical connections to avoid potential issues.
By following these troubleshooting techniques and maintenance tips, you can maximize the performance and lifespan of your homemade woodworking machinery. However, it is important to remember that each machine may have specific maintenance requirements. Always refer to the manufacturer’s instructions and guidelines for proper care and maintenance practices.
Final Thoughts and Future Considerations
In conclusion, this article has provided a comprehensive guide on how to make woodworking machinery. We have explored the different types of woodworking machinery available, discussed the steps and considerations in designing your own machinery, highlighted the importance of selecting quality materials and components, and provided a detailed list of tools and equipment needed for construction.
Additionally, we have emphasized the significance of safety precautions while building woodworking machinery to ensure a secure working environment. The assembly and construction process have been broken down into detailed steps, guiding readers through each stage. Troubleshooting techniques and maintenance tips have also been offered to help readers troubleshoot common issues and prolong the lifespan of their homemade woodworking machinery.
In summarizing the key takeaways from this blog post, it is clear that making your own woodworking machinery can offer numerous benefits such as cost-effectiveness, customization options, and a deeper understanding of the craft. By following the step-by-step guide and considering all necessary factors like materials selection, tool requirements, safety measures, assembly process, troubleshooting techniques, and maintenance tips, readers can successfully create high-quality woodworking machinery.
For further exploration in the realm of homemade woodworking machinery, readers can consider researching advanced designs or modifications to incorporate additional features or functionalities into their machines. Moreover, staying updated with new technologies or innovations in the industry will provide valuable insights for improving homemade machinery. Collaboration with fellow woodworkers could also be beneficial in sharing expertise and ideas.
Ultimately, by investing time and effort into making your own woodworking machinery using this guide as a reference point, you will be equipped with a valuable tool that enhances your woodworking skills while saving money in the long run. So go ahead and embark on this exciting journey towards creating your very own custom-made woodworking machinery.
Frequently Asked Questions
What woodworking projects sell well?
Woodworking projects that tend to sell well are those that are practical and in high demand. Examples of such projects include furniture pieces like coffee tables, bookshelves, and dining tables. These items are constantly sought after by individuals looking to furnish their homes or businesses.
Additionally, smaller decorative items like cutting boards, picture frames, and wooden toys can also be popular sellers. Customized projects that cater to specific needs or preferences of customers are often in high demand as well.
What machines do I need for woodworking?
The machines needed for woodworking depend on the complexity of the projects you wish to undertake. However, some essential machines commonly found in woodworking shops include a table saw, miter saw, band saw, jointer/planer, drill press, and a router table.
These machines cover a wide range of functions like cutting lumber accurately and precisely (table saw), creating angled cuts (miter saw), resawing thick stock (band saw), smoothing rough lumber (jointer/planer), drilling holes (drill press), and shaping edges and profiles (router table). Additionally, a dust collector or shop vacuum is necessary for maintaining a clean work environment and reducing health risks associated with wood dust.
What is the most popular machine in a woodworking shop?
Among the various machines found in a woodworking shop, the table saw is arguably the most popular machine due to its versatility and importance in many woodworking operations. A table saw consists of a circular blade mounted on an arbor that protrudes through the surface of a flat tabletop-like structure. It allows precise cutting of wood pieces by adjusting the height and angle of the blade accordingly.
With this machine, woodworkers can make straight rip cuts along the grain or crosscuts across it with accuracy and ease. The ability to create dadoes and rabbets using various accessories adds further versatility to its usage. Table saws come in different sizes and configurations depending on the space available in your workshop as well as your specific woodworking needs.
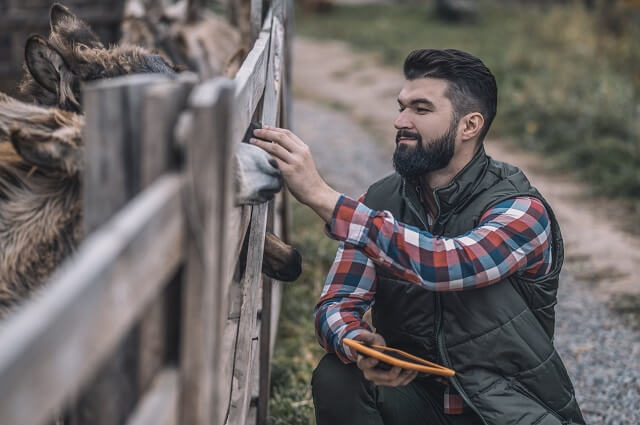
Hi everyone! I’m a woodworker and blogger, and this is my woodworking blog. In my blog, I share tips and tricks for woodworkers of all skill levels, as well as project ideas that you can try yourself.