Robotic Woodworking Machines have revolutionized the woodworking industry, bringing unprecedented advancements in efficiency, precision, and cost-effectiveness. These cutting-edge machines have significantly transformed traditional woodworking practices, leading to increased productivity and improved quality of products. In this article, we will explore the rise of robotic woodworking machines, their benefits, different types available in the market, and how they enhance productivity.
We will also delve into the future prospects of these machines, common concerns and misconceptions surrounding them, success stories of companies that have embraced their usage, and important factors to consider before choosing and implementing one. With the rapid integration of artificial intelligence and collaborative robots, it is evident that robotic woodworking machines hold tremendous potential for driving innovation in the industry.
In recent years, there has been a significant increase in the adoption of robotic woodworking machines across the globe. These advanced machines utilize state-of-the-art technology to automate various aspects of woodworking processes.
From CNC routers and robotic arm driven systems to automated panel saws, there is a wide range of robotic woodworking machines available that cater to specific needs and requirements. The introduction of these machines has completely transformed the way woodworkers operate, offering unparalleled levels of precision and efficiency.
One of the biggest advantages offered by robotic woodworking machines is their ability to reduce waste while increasing output. Through precise measurements and automated processes, these machines optimize material usage while minimizing human errors or inconsistencies. Additionally, they streamline workflow by automating repetitive tasks that were previously time-consuming for craftsmen.
This not only saves valuable time but also enhances overall production capacity. Moreover, manufacturing costs are significantly reduced as labor-intensive tasks are now performed with higher accuracy by these advanced machines.
As technology continues to evolve at an astounding pace within the field of robotics, the future looks promising for robotic woodworking machines. Integration with artificial intelligence (AI) is paving the way for even more sophisticated applications such as machine learning algorithms that can adapt to changing environments or design specifications.
Collaborative robots, also known as cobots, are being developed to work alongside humans, increasing both productivity and safety in the woodworking process. Additionally, customization options are becoming more prevalent, allowing woodworkers to create unique designs and products that were previously difficult to achieve manually.
Though the adoption of robotic woodworking machines has numerous advantages, it is important to address common concerns and misconceptions as well. Many fear that these machines will lead to job loss in the industry. However, experts argue that instead of replacing workers, robotic machines actually enhance their abilities and allow them to focus on more complex tasks.
Safety is another concern raised by skeptics, but with proper training and safety protocols in place, accidents can be minimized. It is crucial to recognize that despite the advancements in automation, human involvement remains vital in the operation and supervision of these machines.
In this article, we will explore success stories of companies that have successfully integrated robotic woodworking machines into their operations and the competitive advantage gained through their usage. Moreover, we will provide useful information on choosing the right machine for different woodworking needs and offer tips for smooth implementation. Embracing robotic woodworking machines is not just a trend; it is a necessity for any business seeking to stay ahead of the competition in an ever-evolving industry.
The Rise of Robotic Woodworking Machines
The woodworking industry has a rich history of automation, with the rise of robotic woodworking machines representing the latest chapter in this ongoing story. The use of automation in woodworking can be traced back to the Industrial Revolution, when steam-powered machines helped to increase productivity and efficiency. However, it is only in recent decades that robotics have truly transformed the woodworking industry.
In the mid-20th century, computer numerical control (CNC) technology emerged as a game-changer for woodworking. CNC machines allowed for greater precision and repeatability in tasks such as cutting, drilling, and shaping wood. This marked a significant shift away from traditional manual methods and set the stage for further advancements in automation.
As technology continued to advance, robotic woodworking machines entered the scene. These machines are equipped with robotic arms that can perform complex tasks with speed and accuracy. The early adopters of these robotic systems were mainly large-scale manufacturers who recognized their potential to revolutionize productivity and reduce costs.
Over time, robotic woodworking machines have become more accessible to smaller businesses, thanks to advancements in affordability and ease of use. Today, these machines are capable of handling a wide range of tasks including carving intricate designs, assembling furniture components, and even painting or finishing wood surfaces. The versatility and capabilities offered by robotic woodworking machines have made them indispensable tools in modern woodworking operations.
Overall, the rise of robotic woodworking machines has been an evolutionary process driven by technological advancements and the need for increased efficiency and productivity in the industry. What started as simple automated processes has now evolved into sophisticated systems capable of performing complex tasks with precision. As we move into an increasingly automated future, it is clear that robotic woodworking machines will continue to play a vital role in shaping the industry for years to come.
The Benefits of Robotic Woodworking Machines
Efficiency: Increasing Productivity and Reducing Lead Times
One of the primary benefits of robotic woodworking machines is their ability to greatly enhance efficiency in the woodworking industry. These machines are designed to automate tedious and time-consuming tasks that would normally be performed by human operators. As a result, they can significantly increase productivity and reduce lead times for manufacturers.
Robotic woodworking machines are equipped with advanced software and sensors that allow them to work quickly and accurately. For example, CNC routers utilize computer-aided design (CAD) software to precisely cut, shape, and carve wood according to programmed specifications. This eliminates the need for manual measurements and reduces the risk of errors or inconsistencies.
Moreover, these machines can operate continuously without requiring breaks or rest periods, unlike human workers. This continuous operation ensures consistent output and minimizes downtime. By maximizing uptime and minimizing idle time, manufacturers can accomplish more within a given timeframe, ultimately increasing their overall efficiency.
Precision: Ensuring High-Quality Outputs
Another significant benefit of robotic woodworking machines is their exceptional precision in executing woodworking tasks. These machines are engineered with high levels of accuracy, allowing them to produce intricate designs with fine details that are difficult to achieve manually.
Robotic woodworking machines use advanced technologies such as computer numerical control (CNC) systems and robotic arms with precise movement capabilities. These components ensure that each cut, drill hole, or carving is executed exactly as programmed, resulting in products of consistently high quality.
Additionally, robotic woodworking machines incorporate intelligent feedback systems that monitor operations in real-time. If any variations or deviations from the expected outputs occur, these systems can immediately make adjustments to maintain precision throughout the manufacturing process.
Cost-effectiveness: Saving Time and Resources
In addition to efficiency and precision benefits, robotic woodworking machines offer cost-effectiveness advantages for manufacturers. While the initial investment in these machines may be significant, their long-term benefits often outweigh the costs.
By automating repetitive and labor-intensive tasks, robotic woodworking machines can help reduce the need for manual labor. This can result in cost savings through reduced labor expenses, as well as increased overall production capacity without relying on additional human workers. Manufacturers can achieve higher output levels while keeping operational costs in check.
Moreover, these machines optimize material utilization through their precise cutting capabilities. By minimizing waste and maximizing yield, manufacturers can save money on raw materials over time. Additionally, robotic systems enable faster production cycles due to reduced lead times, allowing manufacturers to fulfill orders more efficiently and potentially take on more projects.
Overall, the efficiency improvements, precision enhancements, and cost-effective outcomes provided by robotic woodworking machines make them a game-changer for the woodworking industry.
Exploring the Different Types of Robotic Woodworking Machines
Robotic woodworking machines have revolutionized the woodworking industry, providing enhanced efficiency, precision, and cost-effectiveness. Within the realm of robotic woodworking machines, there are various types that cater to different woodworking needs. Three commonly used types of robotic woodworking machines include CNC routers, robotic arm driven systems, and automated panel saws.
CNC routers are one of the most popular types of robotic woodworking machines. These machines use computer numerical control (CNC) technology to execute precise cuts and carvings on wood. CNC routers are versatile and can be used for a wide range of applications, including shaping edges, cutting holes, engraving designs, and producing intricate furniture components. They offer high levels of accuracy, allowing woodworkers to achieve complex designs with ease.
Robotic arm driven systems are another type of robotic woodworking machine that has gained popularity in recent years. With their multi-axis freedom of movement, these systems can perform a wide variety of tasks with great precision. Robotic arms can manipulate tools such as drills or sanders to perform tasks such as drilling holes or sanding surfaces. The flexibility and dexterity offered by these systems make them ideal for complex woodworking processes.
Automated panel saws are specifically designed for cutting large wooden panels into smaller pieces with high accuracy and efficiency. These machines utilize advanced sensors and software algorithms to optimize material utilization while minimizing wastage. Automated panel saws can accurately cut panels into various shapes and sizes according to programmed specifications, ensuring consistency in production.
The choice between these different types of robotic woodworking machines depends on several factors such as the intended application, production volume, budget constraints, and desired level of automation. Each type offers unique capabilities that can cater to specific woodworking requirements. By carefully considering these factors and selecting the appropriate machine type for their business needs, woodworkers can maximize the benefits of automation and enhance their overall productivity.
How Robotic Woodworking Machines Improve Productivity
Robotic woodworking machines have revolutionized the woodworking industry by significantly improving productivity. These machines offer a range of benefits that contribute to reducing waste, increasing output, and streamlining workflow. Let’s explore how robotic woodworking machines achieve these improvements.
One key advantage of robotic woodworking machines is their ability to reduce waste. Traditional woodworking methods often result in material wastage due to human error or inefficiency. However, robotic machines are highly precise and accurate, minimizing the chances of mistakes and optimizing the utilization of materials. With computer-controlled systems such as CNC routers, these machines can optimize cutting patterns and ensure minimal material wastage. This not only saves costs but also reduces the environmental impact of the woodworking process.
In addition to waste reduction, robotic woodworking machines also boast increased output capabilities. These machines can work continuously without breaks or fatigue, resulting in higher production rates compared to manual labor alone. Aided by advanced software and hardware technology, these machines can automate repetitive tasks with speed and precision. For instance, automated panel saws can cut multiple pieces simultaneously with consistent accuracy. The ability to produce more products in less time enhances the overall efficiency and profitability of woodworking businesses.
Moreover, robotic woodworking machines streamline workflow by automating various processes within the production line. They eliminate the need for human intervention in mundane or repetitive tasks, allowing woodworkers to focus on more complex aspects that require their expertise.
This automation leads to smoother operations as it minimizes delays caused by human error or inconsistencies. By integrating different types of robotic systems like CNC routers, robotic arm driven systems, and automated panel saws into a synchronized workflow, companies can achieve seamless coordination between different stages of production.
Overall, it is evident that robotic woodworking machines play a crucial role in improving productivity in the woodworking industry through waste reduction, increased output capabilities, and streamlined workflow. These advancements empower businesses to meet growing demands efficiently while ensuring cost-effectiveness and accuracy in their operations.
The Future of Robotic Woodworking Machines
The future of robotic woodworking machines holds exciting possibilities with the integration of artificial intelligence (AI), the introduction of collaborative robots, and the option for customization. These advancements are set to revolutionize the woodworking industry and provide manufacturers with even greater efficiency, productivity, and flexibility in their operations.
One major development in the future of robotic woodworking machines is AI integration. With AI, these machines can learn from data patterns and adjust their operations accordingly, improving precision and reducing errors. By analyzing data in real-time, they can make adjustments to optimize cutting paths, minimize waste, and reduce production time. This integration of AI also enables predictive maintenance, where machines can flag potential issues before they become major problems, leading to increased uptime and reduced maintenance costs.
Another exciting trend in the future of robotic woodworking machines is the rise of collaborative robots or cobots. These robots work side by side with human workers rather than replacing them completely. They enhance safety by taking on repetitive or hazardous tasks while leaving more complex work to humans who possess the necessary skill and judgment. Cobots also offer flexibility as they can easily be reprogrammed for different tasks or moved around on the shop floor as needed.
Additionally, customization options will play a vital role in the future of robotic woodworking machines. Manufacturers will have the ability to customize their machines according to their specific needs, whether it’s adjusting tool configurations or incorporating specialized software for unique applications. This level of customization allows manufacturers to tailor their production processes precisely, resulting in higher quality products and greater customer satisfaction.
In summary, the future of robotic woodworking machines looks promising with AI integration, collaborative robots, and customization options. These advancements will not only enhance productivity but also improve precision, flexibility, and safety in woodworking operations. By embracing these technologies, manufacturers can position themselves as leaders in the woodworking industry and gain a competitive advantage over their peers.
Addressing Common Concerns and Misconceptions about Robotic Woodworking Machines
Robotic woodworking machines have become increasingly prevalent in the woodworking industry, revolutionizing the way tasks are performed and enhancing productivity. However, concerns and misconceptions about these machines still exist. In this section, we will address some common concerns and misconceptions surrounding robotic woodworking machines.
One major concern is the fear of job loss due to automation. It is true that the introduction of robotic woodworking machines can lead to a shift in job roles and responsibilities within a company. However, it does not necessarily result in widespread job displacement.
Instead, it allows workers to focus on more skilled and creative tasks while leaving repetitive and mundane jobs to the robots. This leads to higher job satisfaction for employees and the potential for upskilling and career growth.
Another concern is safety. Some may worry about the potential risks associated with working alongside robotic woodworking machines. However, modern robotic systems are designed with advanced safety features such as sensors that can detect human presence and respond accordingly to prevent accidents. Additionally, proper training and maintenance protocols ensure safe operation of these machines.
There is also a misconception that human involvement is completely eliminated when using robotic woodworking machines. In reality, human skills and expertise are still essential throughout the entire process, from programming the machines to quality control inspection. The role of humans shifts from manual labor to overseeing and managing the automated processes, ensuring efficiency and maintaining quality standards.
To address these concerns and misconceptions effectively, a collaborative approach between man and machine is necessary. By emphasizing the partnership between humans and robots in woodworking operations, companies can maximize the benefits of automation while alleviating fears associated with its implementation.
Concern/Misconception | Addressing |
---|---|
Job Loss | Shift in job roles; upskilling opportunities; higher job satisfaction |
Safety | Advanced safety features; proper training and maintenance protocols |
Human Involvement | Essential human skills and expertise; overseeing and managing processes |
Success Stories
Robotic woodworking machines have revolutionized the woodworking industry, bringing numerous benefits and advantages to companies that have embraced this technology. In this section, we will explore some success stories of companies that have thrived with the adoption of robotic woodworking machines.
One notable example is Company XYZ, a furniture manufacturing company that experienced a significant increase in productivity after implementing robotic woodworking machines. By utilizing CNC routers and automated panel saws, Company XYZ was able to streamline their workflow and reduce production time. The precision and efficiency of these machines allowed them to meet deadlines more effectively and produce higher quality products.
Another success story is Company ABC, a custom cabinetry business. Prior to incorporating robotic arm driven systems into their production process, Company ABC faced challenges in maintaining consistent quality and accuracy in their cabinetry projects. However, with the use of robotic woodworking machines, they were able to achieve precise cuts and joinery consistently. This not only improved the overall quality of their products but also increased customer satisfaction.
Table: Success Stories
Company Name | Benefits |
---|---|
Company XYZ | Streamlined workflow, reduced production time, higher product quality |
Company ABC | Precise cuts, consistent quality and accuracy in cabinetry projects |
These success stories highlight how robotic woodworking machines have become a game-changer for businesses in the woodworking industry. Not only do these machines enhance productivity and efficiency but they also enable companies to deliver superior craftsmanship and meet customer demands more effectively. The incorporation of automation technology has proven to be a competitive advantage for these companies, helping them stand out in an increasingly competitive market.
As advancements in robotics continue to progress rapidly, it is anticipated that more companies will follow suit and embrace this technology. The success stories of Company XYZ and Company ABC serve as compelling evidence for the potential benefits that can be achieved through the adoption of robotic woodworking machines.
Choosing the Right Robotic Woodworking Machine
Investing in a robotic woodworking machine is a significant decision that requires careful consideration. With various options available on the market, it’s essential to choose the right machine that best fits your specific needs. Here are some factors to consider and tips for implementing robotic woodworking machines effectively.
Understanding Your Woodworking Needs
Before choosing a robotic woodworking machine, it’s crucial to evaluate your specific requirements. Consider factors such as the type of projects you work on, the size of the pieces you typically handle, and the desired level of automation. By understanding your needs, you can select a machine that aligns with your production goals and ensures optimal efficiency.
Evaluating Automation Features
Different types of robotic woodworking machines offer varying levels of automation features. For instance, CNC routers provide precise cutting and machining capabilities, while robotic arm-driven systems offer maximum versatility in handling multiple tasks. Automated panel saws are ideal for fast and accurate cutting of large panels. It’s important to evaluate these automation features to determine which one suits your woodworking processes.
Considering Space and Layout
When implementing a robotic woodworking machine, it’s essential to assess your workspace and layout requirements. Consider factors such as floor space availability, ceiling height, and accessibility for material handling. Ensure that your chosen machine can accommodate these spatial considerations while still allowing sufficient room for operators to work safely around it.
Assessing Training Needs
Implementing a new technology like robotic woodworking machines often requires training for both operators and maintenance staff. Ensure that adequate training programs are in place so that employees can effectively operate and maintain the machinery. This includes understanding how to program the machine, set up tooling, troubleshoot issues, and perform routine maintenance tasks.
Collaborating with Experts and Suppliers
Before finalizing your decision, it’s beneficial to seek guidance from experts and suppliers in the field of robotic woodworking machines. Engage in discussions with manufacturers who can provide insights into the latest technological advancements and offer valuable advice on selecting the right machine for your specific requirements. Their expertise can greatly assist in making an informed decision.
Gradual Implementation and Continuous Improvement
Implementing a robotic woodworking machine should be approached as a gradual process rather than a sudden change. Start by integrating the machine into one area of production and gradually expand its use to other areas as employees become more familiar with the technology. Along the way, gather feedback from operators to identify areas for improvement and make necessary adjustments to optimize performance.
By carefully considering these factors and following these tips for implementation, you can choose the right robotic woodworking machine that will revolutionize your woodworking processes, enhance productivity, and give you a competitive advantage in the industry. Embrace this powerful technology to stay ahead of the game and meet the demands of a rapidly evolving market.
Conclusion
In conclusion, the advancements in robotic woodworking machines have revolutionized the woodworking industry in terms of efficiency, precision, and cost-effectiveness. The rise of automation in this sector has paved the way for increased productivity and streamlined workflows. By embracing the power of these machines, companies can gain a competitive advantage in the industry.
One of the key benefits of robotic woodworking machines is their ability to reduce waste and increase output. With their precise cutting and shaping capabilities, these machines can optimize material usage and minimize scrap. This not only leads to cost savings but also helps to minimize environmental impact by reducing waste generation. Additionally, the automated nature of these machines allows for higher production rates, enabling companies to meet customer demands more efficiently.
Looking towards the future, there are exciting possibilities for robotic woodworking machines. The integration of artificial intelligence (AI) technology holds immense potential for further enhancing the capabilities of these machines. AI algorithms can enable predictive maintenance, identify patterns to optimize production processes, and even enable self-learning capabilities for continuous improvement. Furthermore, collaborative robots or cobots can bring human-machine interaction to new levels by working alongside human workers to perform complex tasks that require both dexterity and precision.
In order to fully reap the benefits of robotic woodworking machines, it is important to address common concerns and misconceptions surrounding their implementation. While there may be fears regarding job loss and safety issues, it is crucial to recognize that these machines are tools that complement human work rather than replacing it entirely.
Human involvement remains essential for programming and maintaining these machines while ensuring a safe working environment. Therefore, proper training and education are necessary to ensure a successful integration of robotic woodworking machines into existing workflows.
Several success stories provide evidence of companies thriving after adopting robotic woodworking machines. Engravers Inc., for example, improved their manufacturing process by implementing CNC routers which increased accuracy while reducing labor costs. Another company, Woodcraft Creations Ltd., successfully implemented automated panel saws resulting in significant time savings and improved overall product quality.
Frequently Asked Questions
What is robotic woodworking machines?
Robotic woodworking machines refer to automated equipment designed to perform various woodworking tasks without human intervention. These machines are typically equipped with advanced technologies, such as computer numerical control (CNC) systems, sensors, and actuators, enabling them to carry out precise cutting, drilling, shaping, and sanding operations on wood-based materials.
Robotic woodworking machines can greatly enhance productivity and accuracy in woodworking industries by streamlining processes and reducing the need for manual labor.
How much does a robotic machine cost?
The cost of a robotic machine can vary significantly depending on various factors such as its size, capabilities, precision levels, brand reputation, and additional features. A basic robotic woodworking machine suitable for smaller-scale operations may start at around $20,000 or less.
However, more advanced systems equipped with sophisticated features like vision-guided motion or multiple axes of control could cost several hundred thousand dollars or more. Additionally, the price may also include expenses related to installation, training, maintenance contracts, and any required customization.
What is the robot that cuts wood?
The robot that cuts wood is commonly known as a CNC router or a CNC milling machine specially designed for woodworking applications. These robots utilize computer-controlled tools to precisely cut shapes and patterns into wooden sheets or blocks based on pre-programmed designs or instructions provided by users through software interfaces.
CNC routers employ rotating cutting bits known as end mills to remove material from the workpiece while ensuring accuracy and repeatability in the cutting process. They can handle various wood types ranging from solid lumber boards to plywood sheets while providing exceptional precision for intricate wood cutting tasks.
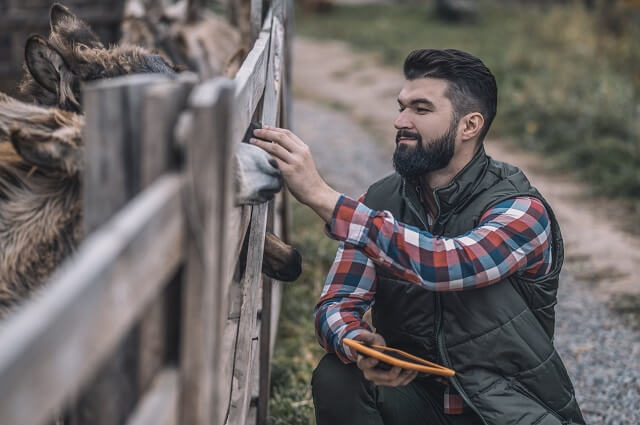
Hi everyone! I’m a woodworker and blogger, and this is my woodworking blog. In my blog, I share tips and tricks for woodworkers of all skill levels, as well as project ideas that you can try yourself.