Traditional woodworking, once a revered and thriving craft, has experienced a significant decline in recent decades. The expertise and skill of the traditional woodworker, who meticulously handcrafted furniture and other wooden objects, have gradually faded away in the face of modern techniques and machinery. This article delves into the factors that have contributed to the decline of traditional woodworking, including the emergence of mass production, shifting consumer trends, technological advancements, economic challenges, and societal changes.
For centuries, traditional woodworkers were highly esteemed artisans who possessed an innate understanding of wood and its potential. They showcased their craftsmanship through intricate joinery techniques, hand-carved details, and precise measurements. However, with the introduction of modern techniques and machinery in woodworking during the industrial revolution, the demand for mass-produced furniture at lower prices began to outweigh the value placed on craftsmanship.
Mass production brought about a profound change in the woodworking industry. Factories equipped with advanced machinery could produce items quicker and more efficiently than individual woodworkers. As a result, traditional craftsmen struggled to compete with larger-scale manufacturers. The shift in consumer preferences towards affordability over quality also played a role in diminishing the demand for handcrafted wooden products.
The rise of technology further compounded the challenges faced by traditional woodworkers. Digitalized design tools allowed for precision cutting and replication on an unprecedented level. While these advancements offered greater efficiency and productivity for woodworking businesses, they marginalized traditional practitioners who relied heavily on manual skills honed over years of practice.
The decline in traditional woodworking can also be attributed to economic factors such as rising costs of materials and labor as well as societal changes that led to an overall devaluation of skilled manual labor. As a result, traditional woodworkers found themselves grappling with financial insecurity and dwindling opportunities to showcase their expertise.
Despite these challenges however there is hope on the horizon for traditional woodworking. A growing movement to revive appreciation for handmade goods coupled with an increased interest in sustainable practices has sparked a renaissance of traditional woodworking.
This article will explore the various initiatives aimed at preserving and revitalizing the craft, including the role of education, apprenticeships, and the need for adaptation to a changing industry landscape. As the face of woodworking continues to evolve, it is crucial to understand the history and challenges faced by traditional woodworkers in order to appreciate and support their unique skills in modern times.
The Emergence of Modern Techniques and Machinery in Woodworking
The Industrial Revolution and Its Impact
With the advent of the Industrial Revolution in the 18th century, the woodworking industry saw a significant shift towards mechanization and mass production. Modern techniques and machinery began to emerge, allowing for faster and more efficient production of wood products. This marked a turning point for traditional woodworking, as hand tools and manual craftsmanship were gradually replaced by automated processes.
One key development during this time was the invention of steam-powered machinery, such as sawmills and planing machines. These innovations drastically increased productivity, enabling larger quantities of wood to be processed in a shorter period of time. Additionally, the introduction of power tools like drills and sanders further sped up the manufacturing process, leading to higher output levels.
The Benefits and Challenges Posed by Modern Techniques
The emergence of modern techniques and machinery brought both benefits and challenges to the woodworking industry. On one hand, these advancements allowed for greater efficiency, improved precision, and reduced labor requirements. Woodworking became more accessible to a wider population as mass-produced furniture became available at lower prices.
However, traditional woodworkers faced significant challenges during this period of transition. Many craftsmen struggled to compete with mass-produced goods that could be manufactured at a fraction of the cost. The demand for handcrafted furniture declined as consumers sought cheaper alternatives produced through industrial methods.
Furthermore, the skills required for traditional woodworking began to lose their value in the market. The focus shifted from craftsmanship to efficiency and speed, leading to a decline in appreciation for handmade items. Traditional woodworkers faced difficulties finding customers who were willing to pay higher prices for their meticulously crafted pieces.
In this changing landscape, traditional woodworkers had to adapt or risk becoming obsolete. Some embraced modern techniques alongside their traditional skills while others concentrated on niche markets or custom-made pieces that catered to a niche clientele seeking unique craftsmanship. Regardless, traditional woodworking underwent a transformation due to the emergence of modern techniques and machinery.
The Impact of Mass Production on Traditional Woodworking Practices
One of the key factors that contributed to the decline of traditional woodworking practices is the impact of mass production techniques. With the advent of industrialization and the rise of factories, woodworking shifted from a primarily handcrafted process to one that relied heavily on machines and assembly lines. This revolutionized the industry by increasing efficiency and productivity, but it also marked a significant departure from the meticulous craftsmanship and attention to detail that were inherent in traditional woodworking.
Mass production brought about several changes in woodworking practices. Firstly, it introduced machinery and power tools that could produce woodwork at a faster pace than ever before. These machines allowed for greater precision and consistency in cutting, shaping, and finishing wood pieces. As a result, production times were significantly reduced, allowing manufacturers to meet growing demands for furniture and other wood products.
Secondly, mass production led to standardization in design and construction methods. Instead of creating unique handcrafted pieces tailored to individual needs, manufacturers began producing standardized items that could be replicated easily and distributed on a large scale. This shift towards uniformity meant that traditional woodworking skills such as intricate joinery or complex carvings became less essential.
Additionally, increased automation reduced the need for a skilled workforce in traditional woodworking industries. Many tasks that required years of training and expertise could now be performed by machinery operated by unskilled laborers. This led to a decline in demand for craftsmen with specialized woodworking skills, resulting in traditional workshops closing down or transitioning towards mass-produced items instead of focusing on handmade craftsmanship.
Shifting Consumer Trends
Consumer trends play a significant role in the decline of demand for handcrafted woodworking. In recent years, there has been a shift in consumer preferences towards mass-produced and factory-made furniture and wooden products. This shift can be attributed to various factors, including affordability, convenience, and the influence of modern design aesthetics.
One primary reason for the decline in demand for handcrafted woodworking is the accessibility and affordability of mass-produced products. With advancements in technology and manufacturing techniques, large-scale production has become more efficient and cost-effective. As a result, consumers can purchase ready-made furniture at lower prices compared to the higher costs associated with custom-made or handcrafted pieces.
Convenience is another driving factor behind the decline in demand for handcrafted woodworking. In today’s fast-paced society, consumers value convenience above all else. The ability to order furniture online or visit a big-box store where they can find a wide range of affordable options makes mass-produced products more appealing than seeking out a custom woodworker.
Furthermore, shifting design trends have also contributed to the decline in demand for traditional woodworking. Modern design aesthetics often favor sleek, minimalist styles that prioritize functionality over ornate craftsmanship. This preference for clean lines and simplicity aligns better with factory-made products that can be replicated consistently.
The Influence of Technology
Technology has had a profound impact on the craft of traditional woodworking, transforming the way woodworkers approach their work and interact with their materials. Digitalized craftsmanship, which involves the use of computer-aided design (CAD) software, CNC machines, and other technological advancements, has both positive and negative implications for traditional woodworkers.
One significant influence of technology on traditional woodworking is the increased precision and efficiency it offers. With the help of CAD software, woodworkers can create intricate designs and patterns more easily than ever before. This technology allows them to visualize their projects in 3D before beginning construction, which can help minimize errors and optimize material usage.
Additionally, CNC machines have revolutionized the production process by automating tasks that were once performed by hand. These machines are capable of cutting, carving, and shaping wood with incredible speed and accuracy. As a result, traditional woodworkers can now produce high-quality pieces more efficiently.
However, while technology has undoubtedly improved certain aspects of woodworking, it has also raised concerns about the loss of craftsmanship and personal touch. Some argue that relying too heavily on digital tools detracts from the skill and artistry inherent in traditional woodworking practices. The use of CNC machines, for example, may be seen as an over-reliance on automation at the expense of handcrafted techniques that have been passed down through generations.
To counterbalance this trend towards digitalization, many traditional woodworkers strive to maintain a balance between new technologies and time-honored techniques. They recognize that while technology can enhance productivity and precision, it is crucial to preserve the essence of craftsmanship that sets their work apart from mass-produced furniture.
By integrating modern tools into their workflow without sacrificing the authenticity of their craftmanship traditions, these woodworkers are finding ways to adapt to the changing landscape while staying true to their passion.
In summary,
Positive Implications | Negative Implications |
---|---|
Increased precision and efficiency | Potential loss of craftsmanship and personal touch |
Ability to create intricate designs with CAD software | Concerns about over-reliance on automation |
Efficient production using CNC machines | Perceived devaluation of handcrafted techniques |
Economic and Societal Factors
Traditional woodworkers face numerous challenges due to economic and societal factors that have contributed to the decline of their craft. One significant challenge is the increasingly competitive global market. With the rise of mass production and cheaper options, traditional woodworking has become less economically viable for many consumers. This has led to a decline in demand for handcrafted woodworking and a shift towards more affordable alternatives.
Another challenge faced by traditional woodworkers is the changing consumer preferences and trends. In today’s fast-paced society, convenience and speed are valued over quality and craftsmanship. Many people are now more interested in quick and disposable products rather than investing in handmade, long-lasting furniture or wooden items. This has further diminished the demand for traditional woodworking.
Additionally, societal changes have impacted the demand for traditional woodworking skills. With advancements in technology, there has been a shift towards more white-collar jobs and away from manual labor professions. This shift means that fewer individuals are pursuing careers in traditional woodworking, leading to a shortage of skilled craftsmen.
Furthermore, globalization has also affected traditional woodworkers as imported goods from countries with lower labor costs flood the market. These imported items often emulate the appearance of handcrafted woodworking while being significantly cheaper due to mass production techniques overseas. This makes it difficult for traditional woodworkers to compete on price without compromising on quality or their own livelihoods.
Overall, economic globalization, changing consumer preferences, and societal shifts towards technology-driven careers have presented significant challenges for traditional woodworkers. Adapting to these challenges requires innovative solutions that combine preserving traditional craftsmanship skills with modern technologies and approaches to attract new customers and ensure the survival of this rich craft.
Reviving the Craft
Over the past few decades, traditional woodworking may have experienced a decline in popularity and demand, but there is a growing movement to revive and rejuvenate this craft. Many artisans and enthusiasts are rediscovering the beauty and value of handcrafted woodworking, leading to a modern renaissance of traditional techniques.
One reason for this resurgence can be attributed to an increasing appreciation for craftsmanship and artisanal products. In a world dominated by mass production and disposable goods, there is a growing desire for unique, high-quality items that showcase skillful craftsmanship. Traditional woodworkers are tapping into this demand by creating one-of-a-kind pieces that highlight the natural beauty of wood and emphasize attention to detail.
Another factor driving the revival of traditional woodworking is the rise of do-it-yourself (DIY) culture and the maker movement. People today are seeking hands-on experiences and taking pride in creating things with their own hands. This has sparked an interest in learning traditional woodworking skills as a creative outlet or hobby. DIY workshops and online tutorials have made it more accessible for individuals to learn these age-old techniques and apply them to their own projects.
Trends Driving Renewed Interest in Traditional Woodworking | Examples |
---|---|
Appreciation for craftsmanship | High-end furniture boutiques showcasing handcrafted wooden pieces |
Desire for unique, high-quality items | Artisans creating custom-made wooden home decor products |
Demand for hands-on experiences | DIY workshops offering woodworking classes |
As the modern renaissance of traditional woodworking gains momentum, there are initiatives in place to support and encourage new generations of woodworkers. Education and apprenticeship programs play a crucial role in preserving and passing down traditional woodworking skills. These programs provide aspiring woodworkers with the opportunity to learn from experienced artisans and gain hands-on experience in a supportive environment.
Furthermore, there has been a shift in perception towards traditional woodworking as a viable career path. Rather than being seen as outdated or obsolete, it is now recognized as a valuable and respected craft that requires skill and expertise. This change in perception has led to increased support for traditional woodworkers through local art fairs, craft festivals, and specialized boutiques that showcase their work.
The Role of Education and Apprenticeships in Preserving Traditional Woodworking Skills
Education and apprenticeships play a vital role in preserving traditional woodworking skills. As modern techniques and machinery began to dominate the woodworking industry, there was a real risk of losing centuries-old craftsmanship. However, with the recognition of the importance of preserving these skills, efforts have been made to pass them down through formal education and apprenticeship programs.
Formal Education in Woodworking
One way traditional woodworking skills are being preserved is through formal education programs. Many vocational schools and colleges offer programs that specifically focus on woodworking and traditional craftsmanship. These programs not only teach students the technical skills required for woodworking but also provide them with a deeper understanding of the history and cultural significance of this craft.
Students in these programs learn various aspects of woodworking, such as joinery, carving, wood turning, and finishing techniques. They also gain knowledge about different types of wood, tools, and safety practices. By receiving structured education in woodworking, students acquire a solid foundation of skills that can then be applied to more specialized areas or even serve as a launching pad for their own artistic endeavors.
The Importance of Apprenticeships
While formal education provides a solid theoretical base for aspiring woodworkers, apprenticeships are crucial for honing practical skills in traditional woodworking. These hands-on experiences allow individuals to work alongside experienced craftsmen who have mastered various techniques over years of practice.
Apprenticeships provide an invaluable opportunity for aspiring woodworkers to observe and learn from established professionals. They learn not only technical skills but also gain insight into problem-solving strategies, design principles, and efficient workflow management. The intimate nature of apprenticeship enables mentorship relationships to develop organically and ensures the transfer of specialized knowledge from one generation to another.
Promoting Collaboration Between Education Institutions and Craftspeople
To further enhance the preservation of traditional woodworking skills, it is essential to foster collaboration between educational institutions offering woodworking programs and practicing craftspeople. By establishing partnerships, institutions can enrich their programs with real-world expertise and industry insights, ensuring that students receive a well-rounded education that aligns with the needs and expectations of the craft.
This collaboration can take the form of guest lectures, workshops, or even internships for students. Craftspeople can share their experiences and provide guidance to aspiring woodworkers, helping them bridge the gap between theory and practice. By working together, educational institutions and craftsmen contribute to cultivating a new generation of skilled traditional woodworkers who are equipped to carry on the legacy of this ancient craft.
The Future of Traditional Woodworking
In conclusion, the future of traditional woodworking relies heavily on the ability of craftsmen to adapt to the changing landscape of the craft. While factors such as modern techniques, mass production, and shifting consumer trends have posed challenges for traditional woodworkers, there is still hope for the survival and resurgence of this ancient art form.
One key aspect that will play a pivotal role in preserving traditional woodworking skills is education and apprenticeships. By passing down knowledge and techniques from one generation to another, craftsmen can ensure that the traditions and skills associated with woodworking are not lost. This includes not only technical skills but also an understanding of the historical significance and cultural value of traditional woodworking.
Furthermore, embracing technology can also be a way forward for traditional woodworkers. With digital tools and advancements in manufacturing processes, craftsmen can blend traditional techniques with modern conveniences to create unique pieces that appeal to a wider audience. The integration of technology can enhance productivity and efficiency while still maintaining the essence of craftsmanship.
As consumer demands continue to evolve, it is crucial for traditional woodworkers to remain adaptable and open-minded. By embracing new design trends and exploring alternative markets, craftsmen can find innovative ways to showcase their work and attract a broader range of customers. Additionally, collaboration with other artisans and building networks within the industry can help create new opportunities for growth and success.
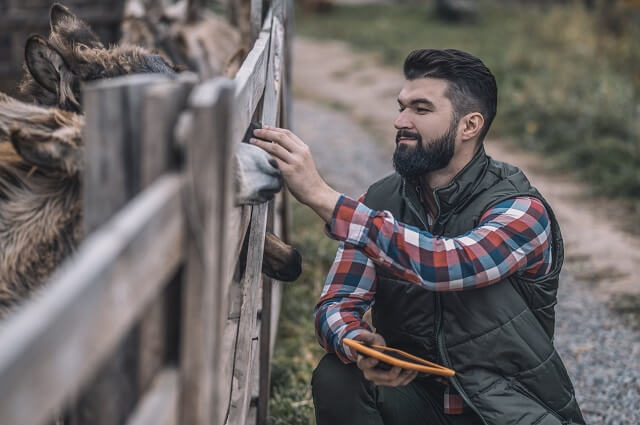
Hi everyone! I’m a woodworker and blogger, and this is my woodworking blog. In my blog, I share tips and tricks for woodworkers of all skill levels, as well as project ideas that you can try yourself.