CNC (Computer Numerical Control) machines have revolutionized various industries, including woodworking. These machines rely on precise and efficient motors to ensure accurate movements and high-quality results. One of the key components that contribute to their performance is the Nema stepper motor. In this article, we will dive into the significance of Nema stepper motors in CNC woodwork and explore the factors to consider when selecting the right one.
Stepper motors play a crucial role in controlling the movement of CNC machines during woodwork processes. Unlike traditional motors, which rotate continuously, stepper motors move in discrete steps or increments. This precision allows for intricate cuts, carvings, and engravings on wood materials. By accurately positioning the cutting tool or workpiece, Nema stepper motors enable woodworkers to achieve detailed designs with ease.
To understand how Nema stepper motors function in CNC woodwork, it is essential to familiarize oneself with Nema standards and various frame sizes. The National Electrical Manufacturers Association (Nema) has set guidelines for motor manufacturers regarding dimensions and performance characteristics. Different Nema frame sizes have specific implications for CNC woodwork applications, such as torque output and physical size limitations.
Choosing the appropriate Nema stepper motor is crucial for achieving optimal performance and efficiency in CNC woodwork projects. Factors such as power requirements, step angle resolution, and holding torque must be carefully considered during selection. An understanding of these factors ensures that the motor can handle the specific demands of woodworking tasks while maintaining accuracy and stability throughout the process.
In the following sections of this article, we will delve deeper into these topics and provide a comprehensive guide on selecting, installing, configuring, maintaining Nema stepper motors for CNC woodwork machines. We will also explore real-life case studies showcasing successful projects made possible by Nema stepper motors. Additionally, we will discuss future developments in Nema stepper motor technology that may further enhance CNC woodwork capabilities.
By gaining a thorough understanding of the importance of Nema stepper motors in CNC woodwork, woodworkers can make informed decisions when it comes to selecting the right motor for their specific needs. With the right Nema stepper motor, CNC woodwork enthusiasts can unlock a world of precision and creativity in their woodworking projects.
Basics of Nema Stepper Motors
Nema stepper motors play a crucial role in CNC woodwork, providing precise and controlled movement for cutting, carving, and shaping wood. In this section, we will explore the basics of Nema stepper motors, including an introduction to National Electrical Manufacturers Association (NEMA) standards for these motors, an explanation of various Nema frame sizes, and a discussion of motor torque in woodwork applications.
NEMA establishes standards for various electrical products, including stepper motors. These standards define the physical dimensions and characteristics of the motors, ensuring compatibility and interchangeability across different manufacturers.
When it comes to Nema stepper motors for CNC woodwork, the most common frame sizes are Nema 17, Nema 23, and Nema 34. The number represents the dimensions of the motor frame in terms of a two-inch square – so a Nema 17 motor has a frame size of approximately 1.7 inches by 1.7 inches.
The frame size has implications for CNC woodwork applications as it determines the overall motor size and its torque capabilities. As a general rule, larger frame sizes have higher torque ratings but may require more powerful drivers and controllers to operate efficiently. Smaller frame sizes are suitable for lighter load applications or where space is limited. Choosing the right frame size ensures optimal performance and compatibility with your CNC woodworking machine.
Motor torque is another important consideration when selecting a Nema stepper motor for CNC woodwork projects. Torque refers to the rotational force that a motor generates to move its shaft or drive mechanisms during cutting or carving processes. Higher torque values allow the motor to exert more force on the tooling bit or spindle, enabling efficient material removal from wooden workpieces.
NEMA Frame Size | Dimensions (inches) | Torque Range (oz-in) |
---|---|---|
Nema 17 | 1.7 x 1.7 | ~20-70 oz-in |
Nema 23 | 2.3 x 2.3 | ~76-200 oz-in |
Nema 34 | 3.4 x 3.4 | ~300-800 oz-in |
It is important to note that torque requirements vary depending on the specific woodworking application and the material being machined. Hardwoods, for example, may require higher torque motors compared to softer woods. Understanding the torque range of different NEMA frame sizes allows woodworkers to choose the appropriate motor to achieve desired cutting power and precision in their CNC woodwork projects.
In the next section, we will discuss factors to consider when choosing a NEMA stepper motor for CNC woodwork, including power requirements, step angle, and holding torque.
Factors to Consider When Choosing a Nema Stepper Motor for CNC Woodwork
Power requirements: Determining the appropriate voltage and current rating
When choosing a Nema stepper motor for CNC woodwork, one important factor to consider is the power requirements of the motor. This includes determining the appropriate voltage and current rating for your specific woodworking needs. Voltage and current are crucial in ensuring that the stepper motor has enough power to drive the cutting tool through the wood material effectively and efficiently.
To determine the appropriate voltage for your stepper motor, it is important to consider the power supply available in your CNC woodworking machine. The motor’s voltage rating should match or be compatible with the power supply voltage to avoid any electrical issues or damage to the motor.
Similarly, considering the current rating of the stepper motor is essential. The current rating determines how much electrical current can flow through the motor windings. Choosing a motor with a higher current rating ensures that it can handle heavier loads and maintain performance during demanding woodwork processes.
Step angle: Understanding the impact of step resolution on woodwork precision
The step angle is another crucial factor to consider when selecting a Nema stepper motor for CNC woodwork. The step angle refers to each individual step that the rotor takes when energized with an electrical pulse. In simpler terms, it determines how accurately the motor can position itself during each movement.
For CNC woodwork applications that require high precision, such as intricate carvings or detailed engravings, a stepper motor with a smaller step angle would be ideal. Smaller step angles provide finer steps, resulting in more precise movements and better control over cutting tools. However, it’s important to note that motors with smaller step angles often have higher costs compared to those with larger step angles.
On the other hand, if you prioritize speed over precision in your woodworking projects, motors with larger step angles may be suitable for your needs. These motors can cover more substantial distances per rotational turn, allowing for faster machining speeds. However, it’s essential to consider the trade-off between speed and precision when selecting a stepper motor for CNC woodwork.
Holding torque: Evaluating the motor’s ability to maintain position during machining
Another critical factor to consider when choosing a Nema stepper motor for CNC woodwork is the holding torque. Holding torque refers to the motor’s ability to maintain its position and resist external forces applied during machining processes.
When cutting through dense or hard wood materials, there can be significant resistance and vibrations that can affect the motor’s position. Therefore, it is important to select a stepper motor with sufficient holding torque to ensure stability and accuracy during operation.
Higher holding torque allows the motor to maintain its position more effectively, reducing the chances of inaccuracies or deviations in woodwork projects. It is advised to carefully evaluate your woodworking requirements and select a stepper motor with suitable holding torque for optimal performance and results.
Considering these factors, power requirements, step angle, and holding torque are important considerations when choosing a Nema stepper motor for CNC woodwork. Each factor plays a crucial role in determining how well the motor performs in various woodworking applications. By taking these factors into account, woodworkers can make informed decisions and select the right stepper motor for their specific needs.
Top Nema Stepper Motor Models for CNC Woodwork
In the world of CNC woodwork, selecting the right Nema stepper motor is crucial for achieving optimal performance. There are various Nema stepper motor models available that are specifically designed for woodworking applications. In this section, we will review and compare some of the top Nema stepper motor models to help you make an informed decision for your CNC woodwork needs.
One of the top Nema stepper motor models for CNC woodwork is the Nema 23 stepper motor. This model offers a good balance between size and power, making it suitable for a wide range of woodwork projects. The Nema 23 stepper motor provides high torque, enabling precise and accurate movements in cutting, carving, and shaping wood.
Another popular option is the Nema 34 stepper motor. This larger-sized motor delivers even higher torque, making it ideal for heavy-duty woodworking applications. The increased power of the Nema 34 allows for faster machining speeds while maintaining accuracy and stability.
For smaller-scale woodworking projects or when space is limited, the Nema 17 stepper motor is a great choice. While it may have a lower torque output compared to larger models, it can still deliver excellent precision and performance in intricate woodwork tasks such as engraving or fine detailing.
Nema Stepper Motor Model | Size (Frame) | Torque (oz-in) | Application |
---|---|---|---|
Nema 23 | 57 mm | 175-200 oz-in | Wide range of woodworking projects |
Nema 34 | 86 mm | 460-565 oz-in | Heavy-duty woodworking applications |
Nema 17 | 42 mm | 46-62 oz-in | Intricate woodwork tasks, limited space |
When selecting a Nema stepper motor for CNC woodwork, it’s important to consider the specific requirements of your projects. Factors such as the size and complexity of your woodworking tasks, desired machining speed, and available space should all be taken into account. By understanding the capabilities and specifications of different Nema stepper motor models, you can make an informed decision that ensures optimal performance and outstanding results in your CNC woodwork endeavors.
Installing and Configuring Nema Stepper Motors in CNC Woodwork Machines
Step-by-step guide on installing Nema stepper motors in CNC woodworking machines
When it comes to installing Nema stepper motors in CNC woodworking machines, following the proper steps is crucial to ensure a successful integration. Here is a step-by-step guide to help you through the process:
- Prepare the workspace: Before beginning the installation, make sure to clear your workspace and remove any obstacles that may obstruct your work area. This will provide you with ample room to maneuver and install the stepper motors properly.
- Identify mounting locations: Determine where the stepper motors will be mounted on your CNC woodworking machine. Consult the manufacturer’s guidelines or user manual for specific recommendations on motor placement.
- Mount the motors: Once you have identified the mounting locations, secure the Nema stepper motors onto your CNC machine frame using appropriate mounting brackets and screws. Ensure that the motors are securely fastened to prevent any vibrations during operation.
- Connect motor wires: Next, connect the motor wires to their respective terminals on your CNC machine’s control board. Check if there are specific instructions or wiring diagrams provided by the manufacturer for proper connection.
Tips for proper alignment and calibration of stepper motors
After installing the Nema stepper motors, it is important to align and calibrate them correctly for optimal performance in your CNC woodworking machine. Here are some tips to follow:
- Alignment: Check that all axes controlled by stepper motors are aligned properly with their corresponding components such as lead screws or belts. Misalignment can result in inaccurate movement and diminished precision.
- Calibration: Use appropriate calibration techniques to achieve accurate movement and positioning of your CNC woodworking machine. This typically involves adjusting settings such as step resolution, velocity, acceleration, and deceleration in your CNC controller software.
- Test movements: Once alignment and calibration steps are completed, perform test movements on each axis of your CNC woodworking machine to verify that the motors are operating smoothly and as expected. Make adjustments as necessary to fine-tune the motor settings.
Overview of necessary software configurations for optimal motor control
To achieve optimal control of your Nema stepper motors in CNC woodworking machines, it is essential to configure the appropriate software settings. Here are some key considerations:
- Motor parameters: Enter the specific motor parameters such as step angle, steps per revolution, and maximum speed into your CNC machine’s controller software. These values will vary depending on the Nema stepper motor model you are using.
- Acceleration and deceleration: Set appropriate acceleration and deceleration values for each axis to ensure smooth and controlled movements of your CNC woodworking machine. This prevents jerky or abrupt motions that may affect the quality of your woodwork.
- Microstepping: Take advantage of microstepping capabilities if available in your stepper motor and CNC controller combination. Microstepping allows for finer resolution of movement by dividing each full step into smaller increments, resulting in smoother motion and improved accuracy.
By following these installation, alignment, calibration, and software configuration guidelines, you can maximize the performance of Nema stepper motors in your CNC woodworking machine setup.
Best Practices for Maintaining Nema Stepper Motors in CNC Woodwork
Nema stepper motors are crucial components in CNC woodwork machines, and proper maintenance is essential to ensure their longevity and optimal performance. This section will provide best practices for maintaining Nema stepper motors in CNC woodwork, including handling and storage tips, regular maintenance routines, and troubleshooting common issues.
To begin with, it is important to handle and store Nema stepper motors properly to avoid any damage. When handling the motor, always hold it by the body and avoid touching the shaft or other sensitive parts. Additionally, make sure to store the motors in a clean and dry environment, away from dust or moisture that could potentially cause damage. It is also recommended to keep them in protective cases or packaging when not in use.
Regular maintenance routines are necessary for ensuring smooth operation and preventing motor failures. One key aspect of maintenance is keeping the motor clean. Regularly inspect the motor for any debris or dirt buildup and use compressed air or a soft brush to remove it carefully. Be cautious not to damage any delicate components while cleaning.
Another important aspect of maintenance is lubrication. Periodically check the manufacturer’s guidelines for the appropriate lubrication schedule and use high-quality lubricants approved for use with stepper motors. Apply lubricant as per the instructions provided without over-lubricating, as this can cause issues such as excessive friction or overheating.
In addition to general maintenance practices, troubleshooting common issues related to stepper motors in CNC woodwork is also crucial. One common problem is motor overheating, which can be caused by factors such as inadequate cooling or incorrect voltage supply. In such cases, checking the cooling system and ensuring that proper voltage levels are being supplied can help resolve the issue.
By following these best practices for maintaining Nema stepper motors in CNC woodwork machines, users can extend their lifespan and ensure reliable performance. However, it is always advisable to consult the manufacturer’s guidelines specific to your motor model for detailed instructions on maintenance procedures, as different motors may have unique requirements.
Case Studies
In this section, we will explore some real-life examples of how Nema stepper motors have been successfully used in CNC woodwork projects. These case studies highlight the capabilities and advantages of using Nema stepper motors in various woodworking applications.
- Example 1: Custom Furniture Production One example of how Nema stepper motors have revolutionized CNC woodwork is in the production of custom furniture. With the use of precise and high-torque Nema stepper motors, furniture manufacturers have been able to create intricate designs and complex joinery with ease. These motors provide exceptional control over the cutting tools, allowing for precise carving and shaping of wood pieces.
- Example 2: Sign Making Another industry that has benefited greatly from Nema stepper motors is the sign-making industry. With the ability to accurately follow design patterns, sign makers can create detailed and professional-looking signs with ease. The wide range of Nema frame sizes available allows for versatility in different types and sizes of signs. Whether it’s small delicate lettering or large illuminated signs, Nema stepper motors deliver consistent results.
- Example 3: Cabinetry Manufacturing Cabinetry manufacturing is another area where Nema stepper motors have had a significant impact. These motors enable smooth and precise cuts for creating intricate cabinet components such as dovetail joints, decorative moldings, and complex drawer systems. The holding torque provided by Nema stepper motors ensures that the motor maintains position during machining operations, resulting in accurate cuts and seamless assembly.
These examples demonstrate how Nema stepper motors have transformed CNC woodwork processes across various industries. By providing precise control, high torque, and reliable performance, these motors have opened up new possibilities for creativity and efficiency in woodworking applications.
Overall, selecting the right Nema stepper motor for CNC woodwork is essential for achieving optimal results. Based on your specific woodworking needs, such as size, complexity, and speed requirements, it is important to consider the features and specifications of different Nema stepper motor models. The next section will provide a detailed review and comparison of various Nema stepper motor models designed specifically for CNC woodwork, helping you make an informed decision.
Future Developments in Nema Stepper Motors for CNC Woodwork
Future Developments in Nema Stepper Motors for CNC Woodwork
As technology continues to advance, so too do the capabilities of Nema stepper motors used in CNC woodwork. The future holds exciting prospects for these motors, with emerging developments set to revolutionize the industry. Here are a few key areas where we can expect to see significant advancements:
Integration with Smart Technology
One of the most notable future developments in Nema stepper motors for CNC woodwork is their integration with smart technology. This integration will allow for improved communication between the motor and other components of the CNC system, resulting in enhanced efficiency and precision. Smart motors will be capable of real-time monitoring and analysis, enabling predictive maintenance and reducing downtime.
Increased Precision and Accuracy
With ongoing research and development efforts, manufacturers are continuously improving the precision and accuracy of Nema stepper motors. These advancements will result in smoother movements, reduced vibration, and higher positioning resolutions. This level of precision will enable woodworking professionals to achieve intricate designs and fine details that were previously difficult or even impossible to accomplish.
Enhanced Durability and Reliability
In the future, Nema stepper motors for CNC woodwork will become even more durable and reliable. This means longer lifespans, reduced wear and tear, and less maintenance required over time. Manufacturers are exploring new materials, design techniques, and lubrication systems to increase motor longevity while ensuring consistent performance under demanding operating conditions.
It’s important for woodworking professionals to keep a close eye on these future developments when considering their options for Nema stepper motors. As new technologies emerge and improve upon existing models, selecting a motor that incorporates these advancements can greatly benefit your CNC woodwork projects.
By staying informed about forthcoming improvements in motor technology, you can make more educated decisions when it comes to choosing the right Nema stepper motor for your CNC woodwork needs. Be sure to consult trusted manufacturers, industry experts, and online resources for the most up-to-date information on these future developments.
Now that we have explored the potential future developments in Nema stepper motors for CNC woodwork, let’s move on to exploring real-life examples of Nema stepper motors in action through case studies in the upcoming section.
Conclusion
In conclusion, selecting the right Nema stepper motor is crucial for achieving optimal results in CNC woodwork. Throughout this article, we have explored the importance of Nema stepper motors in CNC machines and their specific function in woodwork processes. We have also discussed the basics of Nema stepper motors, including Nema frame sizes, motor torque, and the significance of these factors in woodwork applications.
When choosing a Nema stepper motor for CNC woodwork, there are several key factors to consider. Power requirements, step angle, and holding torque all play a role in determining the appropriate motor for your specific needs. It is important to carefully evaluate these specifications to ensure compatibility with your woodworking machine.
To assist you in making an informed decision, we have provided a review of top Nema stepper motor models specifically designed for CNC woodwork. By comparing their features, specifications, and performance in woodwork applications, you can select a motor that aligns with your project requirements such as size, complexity, and speed.
Once you have chosen a suitable Nema stepper motor for your CNC woodwork machine, it is essential to properly install and configure it. We have provided a step-by-step guide on installation procedures as well as tips for alignment and calibration. Additionally, we have highlighted the necessary software configurations for optimal motor control.
Maintaining your Nema stepper motor is essential for its longevity and smooth operation. Proper handling and storage techniques are crucial to prevent damage or failures. Regular maintenance routines should be followed to ensure ongoing performance. In case issues arise with your stepper motor during operation, troubleshooting tips specific to CNC woodwork are available.
We also presented real-life case studies showcasing successful woodwork projects achieved using specific Nema stepper motors along with testimonials from industry professionals. These examples emphasize the capabilities of these motors in unique woodwork applications.
Looking towards the future, advancements in Nema stepper motor design hold promise for improved efficiency, precision, and integration with CNC woodwork systems. Emerging technologies are likely to shape the future of Nema stepper motors, impacting the woodwork industry as a whole.
Frequently Asked Questions
Is NEMA 17 enough for CNC?
NEMA 17 can be enough for certain CNC applications depending on the specific requirements of the machine. The NEMA 17 size refers to the standard dimensions and mounting options of the stepper motor. It has a relatively compact size and offers a good balance between torque and physical space it occupies.
For smaller-scale CNC machines or those that don’t require high torque, a NEMA 17 can provide sufficient power to drive the axes and perform accurate positioning tasks. However, larger and more demanding CNC machines may require stepper motors with higher torque ratings such as NEMA 23 or even NEMA 34 for better performance.
What size stepper motors for CNC?
The appropriate size of stepper motors for CNC depends on various factors including the scale and complexity of the machine, required torque, speed, and accuracy. While there is no one-size-fits-all answer, common sizes used in CNC applications include NEMA 23 and NEMA 34 stepper motors.
These larger motors provide higher torque output compared to smaller sizes like NEMA 17 or NEMA 14, making them suitable for heavier loads or machines that require greater acceleration and precision. Ultimately, selecting the right size of motor involves analyzing the specific requirements of the CNC machine, taking into account factors such as axis mass, lead screw pitch, desired feed rates, and maximum cutting forces.
What is NEMA 17 stepper motor used for?
The NEMA 17 stepper motor is commonly used in various applications due to its compact size and decent torque output capabilities. While it may not be as powerful as larger stepper motors, it finds utility in many low- to mid-range CNC systems where lower torque demands are acceptable. Some typical uses for NEMA 17 stepper motors include small-scale desktop CNC routers or mills used for engraving or light-duty cutting tasks in materials like wood or plastic.
Additionally, they are often employed in automated camera sliders or miniature robotics projects where precise motion control is essential but heavy loads are not involved. The versatility and affordable cost of NEMA 17 stepper motors make them a popular choice in a wide range of applications that don’t require extreme torque requirements.
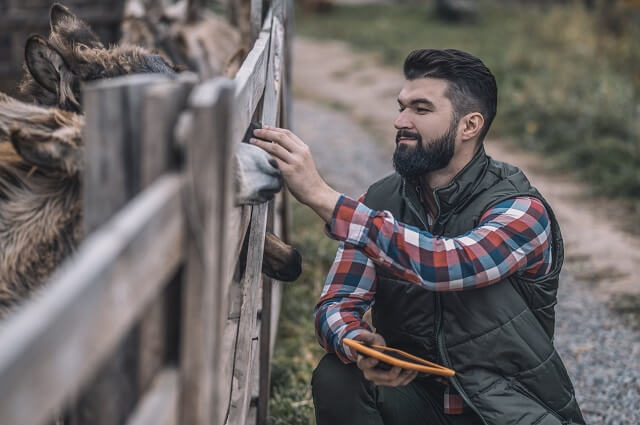
Hi everyone! I’m a woodworker and blogger, and this is my woodworking blog. In my blog, I share tips and tricks for woodworkers of all skill levels, as well as project ideas that you can try yourself.