Introduction to Woodworking Shaper Cutters
A woodworking shaper cutter is a specialized cutting tool used by craftsmen in metal and woodworking shops. It’s typically powered by an electric motor and utilizes a rotating cutting head with multiple blades for producing intricate patterns, shapes, profiles, rabbets, and even decorative edges on materials such as wood, aluminum, plastics and composites. Depending on the model of the cutter desired, there are a variety of styles that range from small machines to large industrial models.
Shapers can produce grooves, round corners, edge contours and curved surface forms used in furniture making and carpentry. The specific benefit it provides woodworkers over hand tools like chisels is a greater speed of production at better faces or grain finish (quality of which depends upon the operator). Additionally, since some types of cuts can require numerous attempts with chisels, shapers are great for achieving more accurate detail in less time with uniform results.
Types of Shaper Cutters vary from manual hand-cranked versions to powerful machine systems for larger projects. For example, single-spindle cutters have one adjustable cutter head with several recessed carbide blades (a coating material harder than steel), while multiple-spindle cutters feature a few to large number of different cutter heads that can run simultaneously or independently depending on the job size. The most essential accessories would be safety devices including shields and guards to protect the operator from chips flying up during operation due to the high speeds these tools operate at. Additional components include router bits which provide extra options when working on long cuts down the material’s middle or near its edges.
Design Considerations
Woodworking shaper cutters are one of the most important tools in a woodworker’s workshop or factory. Shaper cutters come in a variety of shapes and sizes and can be used to produce various types of cuts, patterns, curved and straight edges, pockets, grooves, slots, profiles and more. The following is an overview of the different shape cutters and their benefits/drawbacks.
Straight-Faced Shapers – Straight-faced shapers are the most basic type of cutter and feature blades that are mainly used for making straight cuts along the length of a board. These cutters typically feature a single set of teeth that guide the cutting action across the board’s face. One benefit to using these cutters is that they can make accurate and smooth cuts without imparting any tearout on the material being machined. Unfortunately, these cutters are only able to work with materials which have pre-milled surfaces on either side due to their relatively low cutting power.
Beveled Edge Cutters – Beveled edge cutters are designed with angled teeth which enable them to create cuts along an angled surface as well as straight edges. This type of cutter provides greater control over cutting along even complex geometries as it offers more accurate depth control as well as superior edge finishes than straight-faced shapers. The downside is that they require larger machines due to their greater cutting power which also means greater expense compared to equivalent straight-faced options.
Mortising & Radius Cutters – Mortisers and radius cutters provide excellent results when creating hole patterns such as those required for mortise joints or pocketing operations. These specialist shape cutters have relatively high cutting spans (deeper than standard cutter diameters) meaning fewer passes need to be made when setting up complex shapes or patterns; reducing time/cost savings in production processes where accuracy matters greatly. The downsides are that due to their size, it may not be possible to fit them into projects where space is limited or access into tight corners is difficult using traditional machinery setups such as spindle moulder machines etc…
Overall, each type of shaper cutter has its own advantages and disadvantages players must take into account when deciding which is best suited for particular projects or scenarios. Choosing the correct shape cutter enables woodworkers attain optimal outputs in terms of accuracy, speed & cost during woodworking operations
How to Choose the Right Shaper Cutter
When choosing a woodworking shaper cutter, it is important to take into consideration a few key points. First, consider the size and type of project you are working on. Different types of projects will call for different shaped cutters. For example, if you are making a cabinet with raised-panel doors, then you’ll need a much larger profile than for making crown moldings or rail and stile joints.
In addition to the specific shape the blade needs to create, there are several other aspects to consider when selecting the right shaper cutter for your project:
1. The overall diameter and length of the cutter – The diameter will determine how big of an area the blade can cover while cutting, while the length will affect its ability to reach into tight corners.
2. The number of teeth on the blade – Different amounts of teeth will influence your choice in order to control tear out and leave a smooth finish on your workpiece. As a general rule, more teeth will produce smoother results but slower feed rates.
3. The material used on the arbor – It is important to ensure that the arbor has enough strength to support whatever cutter style you are using in order to protect both tool and workpiece from damage or excessive wear and tear during use.
4. Consider whether variable speed is available – If so, then this could help facilitate different cuts more quickly according to project specifications by changing feed speeds easily as needed during operations.
These considerations should help you narrow down your choices so that you can find exactly what kind of woodworking shaper cutter works best for your individual projects needs!
How to Use a Woodworking Shaper Cutter
Step 1: Make sure your woodworking shaper and workspace is properly set up and secure. Ensure the wood is strong enough to support the cutter safely and that the entire surface area of operation is level. Also make sure all necessary safety equipment, such as gloves, face shields, and ear protection, are in place before you start.
Step 2: Select the type of cutter needed for your project out of a wide array of available options. Woodworkers often use standard plywood or MDF blades, but there are also more specialized cutters made for certain techniques like rail and stile doors, coves, dadoes, rabbets and more.
Step 3: Mount the cutter onto the spindle shaft and tighten it carefully to ensure a secure fit. The spindle must be parallel to the fence and rotation should be clockwise when facing it from behind the machine.
Step 4: Tighten any guide blocks or bushings on your shaper according to specifications in order to prevent excess side-to-side movement as you’re cutting. This will help keep your cuts straight and smooth along the full length of each pass
Step 5: Turn on your woodworking shaper at a medium speed setting so that it’s comfortable for cutting without overloading its motor or causing vibrations inside the machine.
Step 6: Feeding your workpiece through with steady pressure can now begin. Slow down near cut edges for controlled cuts which will leave cleaner finishes on them as well as help minimize tear out on fine woods like veneer Plywood or maple grain finish veneers.
Step 7: To end a cut safely turn off power switch with slight pressure still applied onto feed rate until full stop while clearing board afterwards slightly pulling it away from blades before reversing it in order not to resharpen its cutting edges
Safety Tips
1. Wear safety glasses and a dust mask when using a woodworking shaper, as there is always the possibility of debris flying into your eyes or small particles being inhaled.
2. Make sure you are familiar with the controls and functions of the shaper before using it. Read the operating manual carefully and if you have any questions, ask someone who has experience with such machines for guidance.
3. Ensure that all safety guards are correctly in place before turning on the machine and keep them engaged throughout your cutting process.
4. Never stand directly behind the cutter head while it is in operation, instead stand slightly to one side so that potential fragments that may be thrown off during cutting can be avoided more easily.
5. Keep hands away from the cutter table to avoid accidental contact with spinning cutters as this could cause serious injury or amputation of fingers/hands. Do not attempt to adjust or clear jammed cutters while they’re spinning either – turn off power to the machine first!
6. Also ensure that other workers maintain a safe distance from your workplace whenever you’re using a woodworking shaper so that no one else is in danger should something go wrong during the cutting process.
Maintenance and Care
To maintain your woodworking shaper cutters for optimal performance, there are specific care steps you should take. Cleaning, installation, and storage should all be included in your routine maintenance for the best results.
Cleaning is essential for keeping debris from becoming stuck against blades or bits. First remove any debris that may have adhered to the surface of its blades by using a stiff brush in a circular motion. You can then increase the effectiveness of cleaning your cutter by using compressed air to blast away any remaining dust particles.
Installation might seem self-explanatory, but make sure to check the material compatibility before mounting it onto an arbor shaft in order to avoid damage or splintering. Additionally, ensure that all of the appropriate safety equipment is installed properly before beginning work with the shaper cutter.
Proper storage can extend the life of your shaper cutters and reduce undesired rusting and corrosion due to moisture or humidity buildup on the blades and other components. Herein lies the importance of storing them at an appropriate temperature with minimal exposure to airborne impurities. Keep all other items related components such as bushings, spacers and set screws stored in moisture proof containers whenever not being used as well.
Tips for Enhancing Your Woodworking Skills
Shaper cutters can be a great way to help improve your woodworking skills and create a more professional finish on projects. It is important to select the right kind of shaper cutter for the project to ensure safe and accurate results. Here are some tips to help you when selecting and using shaper cutters:
1. Research and understand the differences between shaper cutters so you can select one that matches your needs in terms of size, shape, profile and finishing options. There are a variety of options available depending on the type of material being shaped and heavy-duty applications may require specific types for safety reasons.
2. Make sure any new shaper cutter is sharpened properly before use. It’s also important to keep spare parts for chipped or damaged cutters on hand in case replacements are needed quickly.
3. Be mindful of any kickback risk when feeding stock into a shaper cutter and make sure all guards are in place before starting work. Safety glasses should also be worn when using a shaper cutter as debris can fly off materials unexpectedly while they are being shaped.
4. Take advantage of all the ways a single tool or profile kit might provide such as rail and stile door making, molding patterns such as ogee, bead, chamfer cuts as well as fluting and reaming operations that involve milling tapered slots or grooves in stock materials.
5. Using multiple operations on one piece will result in faster production times without sacrificing accuracy, so consider how this could apply on larger projects such as gates or furniture pieces with decorative cornice edges
Conclusion
Woodworking shaper cutters are a versatile tool used by professionals and hobbyists alike to create a variety of different shapes and designs. These tools are available in a wide range of sizes for different types of jobs, and can be used for both decorative purposes as well as functional projects. The key to using the cutter properly is to choose the correct size for the job at hand. Additionally, one should ensure that they use the proper sharpening techniques and maintain the blades with regular oiling or sharpening sessions to extend their lifespan. Furthermore, safety goggles and dust masks should be worn when working with shaper cutters so as not to endanger oneself or those around them.
Overall, woodworking shaper cutters can be an invaluable tool for making intricate furnishings quickly and easily. With a little bit of practice, knowledge about the correct sizes for each respective project, as well as proper maintenance routines and safety procedures, anyone should be able to get beautiful results from using this useful tool. Woodworking is an enjoyable craft that can provide great satisfaction from seeing all your hard work come together in beautiful pieces of furniture or artwork – especially if you have done all the work yourself with your trusty shaper cutter!
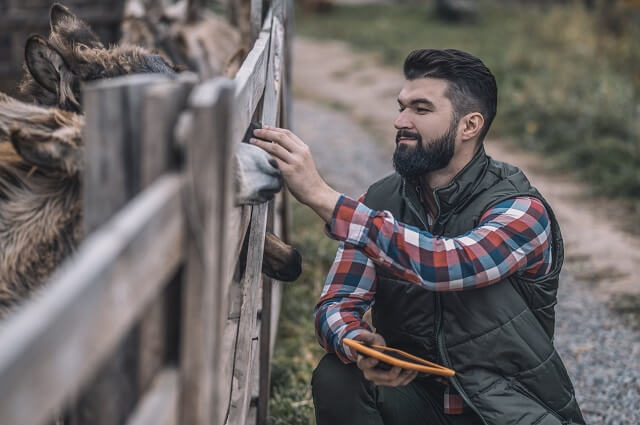
Hi everyone! I’m a woodworker and blogger, and this is my woodworking blog. In my blog, I share tips and tricks for woodworkers of all skill levels, as well as project ideas that you can try yourself.